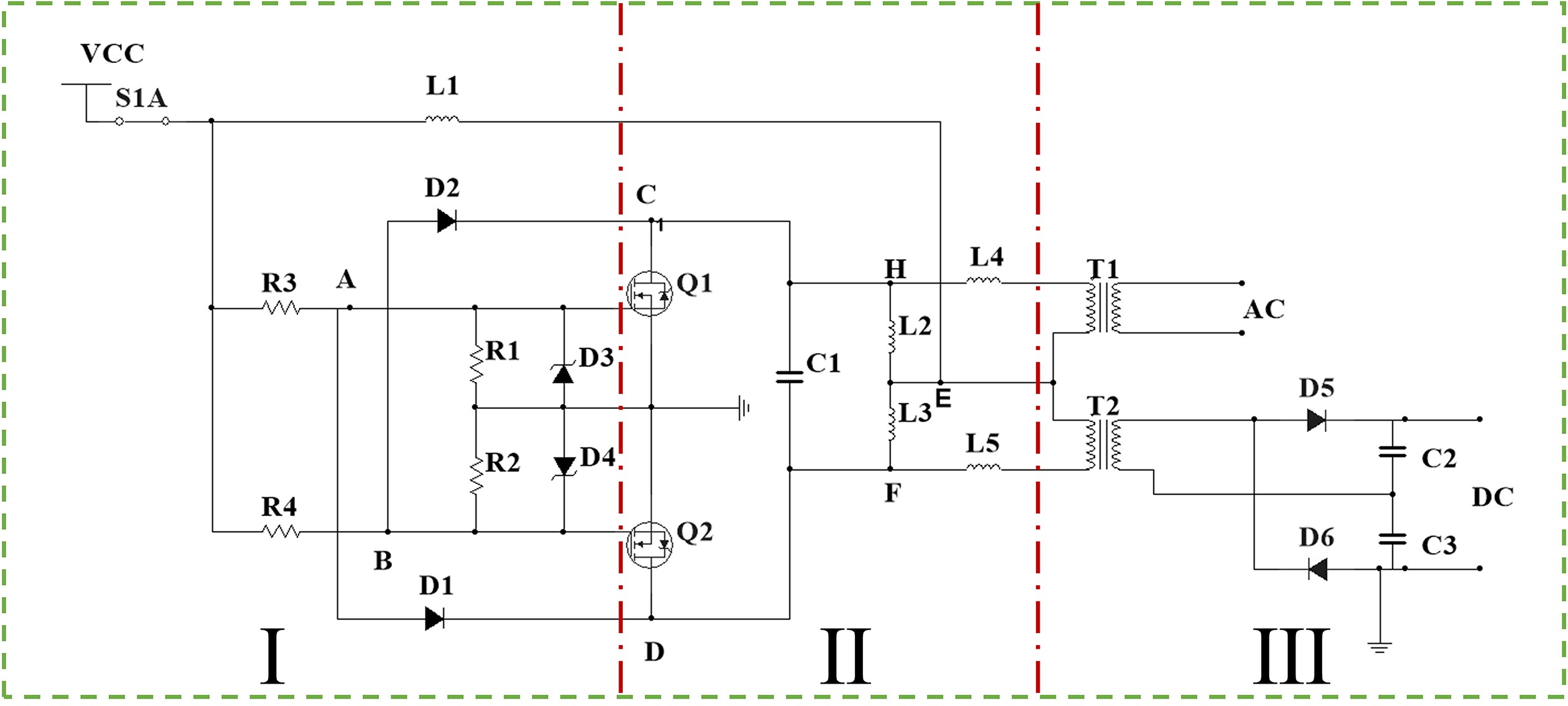
Citation: | Borui ZHENG, Linwu WANG, Jianbo ZHANG, Shaojie QI, Yuhong CHEN, Haodong LIU, Dongliang BIAN. Integrated design and performance optimization of three-electrode sliding discharge plasma power supply[J]. Plasma Science and Technology, 2024, 26(11): 115503. DOI: 10.1088/2058-6272/ad6814 |
The three-electrode sliding dielectric barrier discharge (TES-DBD) plasma actuator significantly enhances the ionization rate and momentum exchange between charged particles and neutral particles by incorporating a parallel DC electrode into the standard DBD design. This design improves the body force and induced jet velocity while allowing flexible control of the induced jet angle, overcoming the limitations of discharge extension and uncontrollable direction in traditional DBD plasma actuators. An integrated plasma power supply has been designed specifically for TES-DBD plasma actuators, streamlining the power supply management. The methodology involves designing the circuit topology for the TES-DBD power supply, followed by simulating and validating its operating principles using Multisim software. The operational performance of the power supply is evaluated through a comprehensive analysis of its electrical, thermal, and aerodynamic properties specific to TES-DBD plasma actuation.
Plasma flow control is an innovative technology for active flow control that utilizes plasma aerodynamic actuation [1]. The fundamental principle is to generate ionic wind through a high-voltage electric field. This ion movement, combined with electromagnetic forces and thermal phenomena, results in plasma discharge [2], creating controlled disturbances in specific local areas of the external flow field. This capability allows for precise manipulation of aerodynamic properties [3].
Plasma flow control offers several advantages, including low cost, lightweight design, simple structure, rapid response, and no mechanical moving parts [4]. The most widely used type of dielectric barrier discharge (DBD) plasma actuator has proven effective in various research applications, such as lift enhancement, drag reduction, aircraft flight control, and flow separation suppression [5]. However, typical DBD plasma actuators have shortcomings, including limited discharge extension, low induced jet velocity, and uncontrollable jet direction [6]. These limitations make applying plasma actuators in scenarios with high external flow velocities difficult, thus restricting their broader engineering use [7]. Consequently, enhancing the efficiency of plasma actuators and improving flow control capabilities is urgently needed [8].
The primary strategies for enhancing plasma actuation efficacy include: (1) optimizing the plasma actuator’s geometric parameters and configuration to increase the surface electric field intensity and boost the resultant body force [9]; (2) minimizing thermal losses within the power supply, concentrating more energy on pneumatic output, and elevating the flow control performance; (3) enhancing the impedance match between the power supply and the plasma actuator to ensure efficient and stable discharge [10].
The three-electrode sliding discharge dielectric barrier discharge (TES-DBD) plasma actuator enhances the standard DBD design by incorporating a direct current (DC) electrode parallel to the alternating current (AC) electrode on its surface [11]. This modification increases the ionization rate on the actuator’s surface and enhances the momentum exchange between ion-generated charged particles and neutral particles. Moreover, the application of distinct DC voltages on the DC electrode side of the TES-DBD plasma actuator yields two discernible discharge effects. When the DC voltage is positive, it effectively augments the body force generated by the actuator and the induced jet velocity [12]. When the DC voltage is negative, it produces a large-area plasma with significant thermal effects and allows the induced jet angle to be flexibly controlled by adjusting the DC voltage. Nonetheless, the TES-DBD plasma actuator requires simultaneous AC and DC power supplies, resulting in increased energy consumption and system complexity due to intricate circuit connections and interactions.
This paper describes the development of an integrated plasma power supply specifically designed for the TES-DBD plasma actuator. By utilizing zero-voltage switching (ZVS) circuit principles [13, 14], this power supply simplifies the external power connections and circuit configuration of the TES-DBD plasma actuator, which traditionally requires multiple power sources. The design employs LC parallel resonance to enhance the ZVS self-oscillating circuit, effectively reducing the output waveform’s oscillation frequency. This modification synchronizes the power supply’s output frequency with the plasma actuator’s operating frequency, improving efficiency and stability. Incorporating a high-frequency transformer with dual output capabilities and a full-bridge inverter circuit enables the simultaneous delivery of high-voltage AC and DC outputs. This versatile and efficient solution meets the diverse requirements of various flow control applications.
The main circuit topology of the TES-DBD plasma supply (figure 1) is divided into three main parts: (1) a protection circuit module, (2) a self-excited oscillation circuit module, and (3) a high-frequency transformer boosting and voltage-doubling rectifier circuit module.
(1) Protection circuit module
The protection circuit module consists of current-limiting resistors (R3 and R4), bias resistors (R1 and R2), and voltage-regulating diodes (D3 and D4). Its primary objective is to protect the MOSFET from breakdown. Voltage-regulating diodes (D3 and D4) are essential for stabilizing the MOSFET’s gate-source (GS) voltage, ensuring that it remains within the specified design limits. The parallel connection of bias resistors (R1 and R2) with the voltage-regulating diodes is an integral part of the protection circuit. This configuration accelerates the MOSFET’s switching speed. It facilitates the discharge of charge accumulated in the GS junction capacitance during circuit shutdown, mitigating the electrostatic breakdown risk. The voltage-regulating diodes are model 1N4742A with a VZ of 12 V, and the bias resistors are 10 kΩ color ring resistors [15].
Resistors R3 and R4 are strategically employed to limit the current flowing through the MOSFET gate, thereby preventing excessive current from damaging the MOSFET. It is crucial to strike a balance in selecting resistor values; excessively high resistance would impede MOSFET conduction, whereas too low resistance would increase circuit power consumption. Therefore, a moderate resistance value ranging from 300 Ω to 500 Ω is recommended. In this circuit, the resistance value is specified as 390 Ω.
(2) Self-excited oscillation circuit module
The self-excited oscillation circuit module, consisting of an LC parallel resonant circuit and MOSFET transistors Q1 and Q2, is designed to efficiently convert DC input into high-frequency AC. This conversion process is initiated when circuit switch S1A closes, allowing the power supply current to flow through resistors R3 and R4 to the gate and source terminals of MOSFET transistors Q1 and Q2. Both MOSFET transistors conduct, but due to the asymmetry of the circuit wiring and the discreteness of component parameters, the conduction speeds of the two transistors are different, resulting in varying currents between the drain and source terminals. Assuming Q2 conducts faster, a larger current flows through Q2. Since the inductive current cannot change abruptly, an induced electromotive force is generated between points H and E, with point H being positive and point E being negative. Consequently, the voltage at point B further increases, accelerating the conduction of Q2 [16].
With Q2 conducting, the potential at point D drops to 0, thereby reducing the potential at point A. Under positive feedback, this ultimately leads to Q2 conducting and Q1 being cut off. At this time, the charging voltage of capacitor C1 increases sinusoidally. Upon reaching its peak voltage, the capacitor discharges, causing the voltage to decrease sinusoidally. The inductor charges between points H and F as the capacitor discharges. As the capacitor discharges, the voltage at point H gradually decreases, as does at point B. When the capacitor finishes discharging, and the capacitor energy reaches its maximum, the inductor charges the capacitor in the reverse direction. The voltage at point F gradually increases, and simultaneously, the voltage at point A also increases. Q1 transitions from a cutoff state to an amplifying state as the inductor continues to charge the capacitor. When the charging is complete, the voltage at point F is the highest, and the voltage at point H is the lowest, resulting in Q1 conducting and Q2 being cut off. Inductor L1 continuously injects energy into the LC circuit to maintain the oscillation process, ultimately achieving stable oscillation.
(3) High-frequency transformer boost and voltage-doubling rectifier circuit module
The high-frequency transformer boost circuit module includes two transformers. The magnetic core of the high-frequency transformer is made of UY10 manganese-zinc, with a primary wire diameter of 0.8 mm and nine primary turns. The secondary wire diameter is 0.09 mm, with 1600 secondary turns, resulting in a turn ratio of 178.
The voltage-doubling rectifier circuit module consists of diodes D5 and D6 and capacitors C2 and C3. Its function is to convert the transformer’s AC output into high-voltage DC through voltage doubling, meeting the power supply’s design requirement to output high-voltage AC and DC simultaneously. Diodes 2CL2FL are chosen as high-frequency, high-voltage diodes, with a withstand voltage of 20 kV and a current rating of 100 mA. Capacitors are selected as high-voltage ceramic capacitors, with a withstand voltage of 20 kV and a capacitance of 10 nF.
The central circuit topology and device parameter selection for the sliding discharge plasma power supply were determined and verified using Multisim simulation software. The simulated circuit of the sliding discharge plasma power supply is depicted in figure 2.
The self-excited oscillation process of the MOSFETs in the circuit and the final output waveforms are simulated using Multisim software. During the simulation, a DC input voltage of 15 V is applied. A four-channel oscilloscope (XSC2) measures the gate and drain voltages of the two MOSFETs to observe the self-excited oscillation process of the circuit. The waveforms are shown in figure 3. From the waveforms, it can be seen that the gate voltages of MOSFET transistors Q1 and Q2 oscillate between 10 V and 0 V, indicating that Q1 and Q2 alternately turn on. Capacitor C1 repeatedly charges and discharges through Q1 and Q2, and the drain voltages of Q1 and Q2 exhibit a sinusoidal half-cycle with a maximum voltage of 52.4 V. This ultimately realizes self-excited oscillation, converting the DC to high-frequency AC.
In the Multisim simulation software, the output waveform of the sliding discharge plasma power supply was detected using oscilloscope XSC1, and the simulation results are shown in figure 4(a). The power supply simultaneously outputs high-voltage AC and high-voltage DC, with Vpp = 25 kV and VDC = 10 kV. Figure 4(b) depicts the actual measurement results, where Vpp = 38 kV, VDC = 11 kV, and the carrier frequency is 22 kHz. The experimental results demonstrate that the designed power supply meets simultaneous AC and DC output requirements.
The TES-DBD plasma actuator consists of two upper electrodes and one lower electrode. The upper electrodes are made of 0.02 mm thick copper foil and are spaced 20 mm apart along the surface of the actuator. The insulating dielectric layer is made of 1 mm thick acrylic glass. The width of the upper electrodes is 4 mm, while the width of the lower electrode is 20 mm. All electrodes have a length of 40 mm. Figure 5(a) shows the actuator’s three-dimensional structure, while figure 5(b) depicts its discharge image.
The sliding discharge plasma supply discharge characterization system mainly includes a voltage probe, a current probe, an oscilloscope, a sliding discharge plasma supply, and a sliding discharge plasma actuator. The total power consumption of the sliding discharge plasma supply is the sum of the power consumption at the AC and DC ends. (1) Measurement of AC power consumption: connect the voltage probe (Tektronix P6015A) and current probe (Tektronix TCP0030A) to the high-voltage output of the sliding discharge plasma supply and utilize the voltage probe and current probe to measure the sliding discharge plasma supply AC voltage Va and AC current Ia [17]. (2) Measurement of DC power consumption: the voltage probe (Tektronix P6015A) is used to measure the DC voltage Vb, and the passive probe (PVP2350) is connected in parallel with a 1 kΩ resistor to measure the DC current Ib. An oscilloscope (MDO3014) displays the output voltage waveforms, current, and other parameters. The measurement system of electrical characteristics is shown in figure 6.
Figure 7 illustrates the relationship between the output AC and DC voltages of the TES-DBD power supply under load. Since the power supply is designed to output AC and DC voltages synchronously, changing the AC voltage will also cause synchronous changes in the DC voltage. Third-order curve fitting shows that the DC voltage is approximately linearly correlated with the AC voltage. All experiments presented in this paper employ AC voltage as a reference for convenience in measurement. Consequently, the term “actuation voltage”, as used in the text, refers to AC voltage.
Figure 8 depicts the output voltage-current curves when the power supply is connected to the actuator. At this point, the output AC voltage (Vpp) is 8.74 kV, with a maximum AC current of 60 mA and an AC frequency of 65.5 kHz. The output DC voltage is −10 kV, with a maximum DC current of approximately 20 mA. Furthermore, the AC voltage-current curve indicates that the discharge in the actuator primarily occurs during the transition from negative to positive polarity. The peak discharge of the DC current is generally synchronized with the peak discharge of the AC current.
The total power consumed by the TES-DBD actuator is the sum of AC and DC power. The formula for calculating the AC power of the plasma actuator is as follows [18]:
Pa(t)=Va(t)×Ia(t), | (1) |
where Pa(t) represents the AC power consumed by the TES-DBD, Va(t) is the AC current, Ia(t) is the AC voltage, and the total AC power consumed is given by:
¯Pa=1T∫T0Va(t)×Ia(t)dt. | (2) |
Here, T denotes the time of a sinusoidal cycle of the peak-to-peak voltage curve.
To ensure the calculated power is more accurate, a more extended period containing about 3–5 sinusoidal cycles of current and voltage is measured in practice. The data within n cycles are selected, the starting moment of integration t0 is determined, the ending moment of n cycles tn is determined, and the integration is performed for that period as follows, ¯Pa is the AC power consumed by the TES-DBD actuator:
¯Pa=1nT∫tnt0Va(t)×Ia(t)dt. | (3) |
The DC power consumed by the TES-DBD actuator is calculated as follows:
Pb(t)=Vb(t)×Ib(t), | (4) |
¯Pb=1(tn−t0)∫tnt0Vb(t)×Ib(t)dt. | (5) |
In the equation Pb(t) is the DC power consumed by the actuator, Vb(t) is the DC voltage and Ib(t) is the DC current. The total power consumption of the sliding discharge plasma supply was calculated to be 27.02 W.
Studies have shown that the energy conversion rate of the plasma actuator, converting electrical energy into mechanical energy of the induced jet, is less than 2%, with most of the energy lost as thermal energy [19]. When generating the induced jet, the surface temperature of the DBD plasma actuator also increases. However, this thermal energy is often ignored in flow control studies. In recent years, utilizing the thermal characteristics of DBD plasma actuator for anti-/de-icing has attracted significant interest from researchers in plasma flow control and flight icing, leading to corresponding research by several teams.
In this experiment, an infrared camera (Testo882) was used to measure the surface temperature of the TES-DBD plasma actuator. The imaging size is 640×480 pixels, the measurement accuracy is ±2 °C, the frame rate is 9 Hz, and the temperature measurement ranges are from −20 °C to +100 °C and from 0 °C to +350 °C. The initial ambient temperature was 20.5 °C. The layout of the temperature characterization experiment system is shown in figure 9.
The temperature measurement zone is shown in figure 10. The figure displays the AC and DC electrodes as dashed boxes, with the temperature measurement zone shown in purple. Point O is located at the midpoint of the DC electrode, with coordinates (0, 0), point B has coordinates (0, 20), and point A has coordinates (20, 0). The X-axis indicates the temperature profile direction of the actuator.
The thermal imaging results are shown in figure 11. After actuation, the surface of the insulating dielectric layer’s surface begins to warm up, with the maximum temperature during the entire actuation process appearing near the AC electrode and spreading in an arc-shaped isotherm from the AC electrode to the DC electrode, indicating that the surface temperature primarily concentrates in the middle section of the AC electrode. As the actuation time increases, the dielectric layer temperature gradually rises, and by t = 90 s, the surface temperature reaches its maximum, stabilizing as the energy injected by the power supply equals the thermal dissipation of the dielectric layer’s surface.
Observation of discharge images indicates the absence of pronounced sliding discharge phenomena when the voltage is below 8 kV, with the generated plasma predominantly concentrated on the side of the AC electrode. However, when the voltage exceeds 8 kV, the temperature distribution on the dielectric layer surface becomes more uniform, accompanied by distinct sliding discharge phenomena. The temperature rise on the dielectric layer surface primarily originates from the energy released by the plasma discharge, including wall heating caused by ion impact on the TES-DBD surface and heat loss from the insulating dielectric layer. When the actuation voltage is below 8 kV, the plasma generated by discharge is mainly concentrated near the AC electrode, resulting in an uneven temperature distribution on the dielectric layer surface and a limited heat transfer range. Conversely, when the actuation voltage exceeds 8 kV, pronounced sliding discharge phenomena occur, leading to a more uniform distribution of plasma discharge. This results in a more even temperature distribution and a wider heat transfer range [20].
Figure 12 shows the temperature variation curves at different measurement points within the test zone. Figure 12(a) shows the temperature variation at point B, where the experimental results indicate that the temperature at point B increases with both actuation time and voltage. At 90 s, the temperature at point B is 38 °C at 7 kV, 42.6 °C at 8 kV, 52.5 °C at 9 kV, and 81.1 °C at 10 kV. Additionally, at actuation voltages of 7 kV, 8 kV, and 9 kV, the temperature rises gradually from 0 to 60 s and stabilizes from 60 to 90 s. However, at 10 kV, the temperature increases rapidly throughout the 0–90 s timeframe.
Figure 12(b) shows the temperature variation at point O, which exhibits a similar trend to point B but with higher temperatures. At 90 s, the temperature at point O is 38.9 °C at 7 kV, 44.6 °C at 8 kV, 61.1 °C at 9 kV, and 97.2 °C at 10 kV.
Figure 12(c) shows the temperature variation curve at point A. The experimental results indicate that the temperature at point A increases rapidly within the first 0–45 s, with a change in temperature (ΔT) of 35.4 °C at 7 kV, 46.8 °C at 8 kV, 63 °C at 9 kV, and 89.8 °C at 10 kV. From 45 to 90 s, the temperature tends to stabilize. At 90 s, the temperature at point A is 58.9 °C at 7 kV, 67.4 °C at 8 kV, 93.5 °C at 9 kV, and 128.5 °C at 10 kV.
The results indicate that point A has the highest temperature while point B has the lowest. This can be attributed to the fact that the plasma is primarily generated near the AC electrode, with point A situated at the midpoint of the AC electrode, leading to the highest temperature at point A. Conversely, point B, located at the edge of the DC electrode, experiences less plasma generation and thus exhibits a slower temperature rise.
Figure 13 shows the temperature profiles of the TES-DBD along the x-direction at different times and voltages. Overall, the temperature profiles under the same actuation conditions show a consistent trend: the lowest temperature is near x = 0 mm (DC electrode), followed by a slow increase along the x direction, and a steeper increase after x = 15 mm, with the highest temperature at x = 20 mm (AC electrode). As the actuation time increases, the overall profile temperature also increases, with the changes in the temperature profile curves remaining consistent at different times.
Figures 13(a) and (b) show the temperature profiles at actuation voltages of 7 kV and 8 kV. The temperature profile curves at these voltages increase slowly with time. Figures 13(c) and (d) show the temperature profiles at actuation voltages of 9 kV and 10 kV, where the temperature profiles increase rapidly with time. For the same actuation time, the temperature profiles also grow more quickly along the x-direction, with a steep increase in temperature after x = 15 mm.
Particle Image Velocimetry (PIV) can capture instantaneous flow information of the entire flow field. It calculates fluid velocities at particle positions by detecting the displacement of tracer particles over a short period. The PIV measurement system mainly consists of a dual-pulse laser and a high-speed dual-frame camera (Imager Pro LX). When the experimental system is set up, the laser plane of the PIV is perpendicular to the TES-DBD plasma actuator, with the thinnest part of the laser plane positioned at the center of the TES-DBD.
A square glass cover (600 mm long, 300 mm wide, and 350 mm high) is placed in the test area to prevent interference from external flow fields. Smoke cakes are used as tracer particles. To obtain a stable flow field, the ignited smoke cake is placed inside the glass box, and the glass cover is placed over the box. The experimental testing commences after allowing the glass box to stand for 5 min. PIV data acquisition is performed approximately 10 s after plasma actuation is applied. Simultaneously, the discharge voltage is measured using a Tektronix P6015A high-voltage probe. After a test condition, the plasma actuator surface is cleaned to prevent the accumulation of smoke dust from affecting the plasma discharge. The actuator structure in the experiment is the same as shown in figure 5. The PIV experiment layout is shown in figure 14.
PIV experiments investigated the effect of induced jets produced by sliding discharge plasma supply with different actuation voltages (9–12 kV). In figure 15, the AC electrode generates the induced jet and directs it toward the DC electrode. The jet angle increases with the actuation voltage. When the actuation voltage is lower than 9 kV, the induced jet the TES-DBD generates is a near-wall jet. Due to the low negative DC voltage, the TES-DBD does not generate sliding discharge, and the negative DC has little effect on the flow field. At this time, the direction of the induced jet is mainly determined by the AC electrode. When the actuation voltage is greater than 9 kV, the direction of the induced jet is determined by the AC and the negative DC electrodes combined force. The induced jet velocity and flow field influence zone also increase with the actuation voltage [21].
The relationship between the actuation voltage and the induced jet angle is shown in figure 16. The induced jet angle is 14.8° at 9 kV, 63.4° at 10 kV, 90° at 11 kV, and 114.5° at 12 kV. The angular increment of the induced jet decreases with increasing actuation voltage: 52° between 9 and 10 kV, 26.6° between 10 and 11 kV, and 24.5° between 11 and 12 kV.
This paper presents the design of a three-electrode sliding dielectric barrier discharge (TES-DBD) plasma power supply based on the zero-voltage switching (ZVS) circuit principle. The power supply achieves simultaneous output of high-voltage AC and DC through innovative designs of a dual-output high-frequency transformer boost circuit and a full-bridge inverter circuit, meeting the requirements of various application scenarios. The power supply’s electrical characteristics were evaluated using multisim simulation software and an electrical testing system. The actuation characteristics were also assessed using a temperature testing system and a PIV experimental system. The main experimental conclusions are as follows:
(1) The electrical characteristics show that the power supply’s maximum output AC voltage is Vpp = 38 kV, and the DC voltage is 11 kV. Due to the unique design of the dual-output AC and DC power supply, the output DC voltage and AC voltage change linearly. The power supply output power is 27.02 W.
(2) The temperature characteristics show that the TES-DBD actuator surface temperature is conducted from the AC electrode side to the DC electrode side, with the highest temperature at the AC electrode. The temperature front forms an arc shape.
(3) Under the same actuation conditions, the temperature profile changes consistently. The lowest temperature is near x = 0 mm (DC electrode), followed by a slow increase along the x-direction and a steep increase after x = 15 mm, with much faster temperature growth. The temperature is the highest at x = 20 mm (AC electrode).
(4) The PIV experiments show that the induced jet generated when the actuation voltage is lower than 9 kV is a near-wall jet. The deflection angle of the induced jet increases with the actuation voltage after it exceeds 9 kV. The maximum deflection angle reaches 114.5°.
The experiments conducted have verified the reliability and practicality of the TES-DBD power supply. The subsequent plan involves installing the TES-DBD power supply onto drones for flow control and anti-icing/de-icing experiments. The TES-DBD power supply cannot independently control its AC and DC outputs, so future work will focus on improving this functionality to enable independent control of the outputs.
This work was supported by National Natural Science Foundation of China (Nos. 61971345 and 52107174).
[1] |
Wu Y and Li Y H 2016 Plasma flow control In: Shohet J L Encyclopedia of Plasma Technology - Two Volume Set Boca Raton: CRC Press 2016: 1016
|
[2] |
Leonov S B, Adamovich I V and Soloviev V R 2016 Plasma Sources Sci. Technol. 25 063001 doi: 10.1088/0963-0252/25/6/063001
|
[3] |
Konstantinidis E 2019 Actuators 8 66 doi: 10.3390/act8030066
|
[4] |
Zheng B R et al 2020 AIAA J. 58 733 doi: 10.2514/1.J058424
|
[5] |
Kriegseis J, Simon B and Grundmann S 2016 Appl. Mech. Rev. 68 020802 doi: 10.1115/1.4033570
|
[6] |
Liu Y et al 2018 Int. J. Heat Mass Transfer 124 319 doi: 10.1016/j.ijheatmasstransfer.2018.03.076
|
[7] |
Yang B et al 2023 Aerospace 10 1016 doi: 10.3390/aerospace10121016
|
[8] |
Lei Yuan et al 2024 IEEE Trans. on Plasma Sci. 52 867 doi: 10.1109/TPS.2024.3357747
|
[9] |
Baranov S A et al 2021 Aerosp. Sci. Technol. 112 106643 doi: 10.1016/j.ast.2021.106643
|
[10] |
Nunes-Pereira J et al 2022 Polym. Adv. Technol. 33 1278 doi: 10.1002/pat.5600
|
[11] |
Zheng B R et al 2023 Chin. Phys. B 32 095203 doi: 10.1088/1674-1056/acae76
|
[12] |
Kourtzanidis K and Raja L L 2017 AIAA J. 55 1393 doi: 10.2514/1.J055473
|
[13] |
Sathyan S et al 2016 IEEE Trans. Ind. Electron. 63 6898 doi: 10.1109/TIE.2016.2582460
|
[14] |
Zhao Lisheng et al 2024 IEEE Transactions on Industrial Electronics 71 12086 doi: 10.1109/TIE.2023.3342283
|
[15] |
Liu F, Liu P Z and Chai W Y Design of high voltage surge suppression circuit for unmanned ground vehicle computer system In: 2017 IEEE International Conference on Unmanned Systems Beijing: IEEE 2017: 539
|
[16] |
Ekhtiari M et al 2018 IEEE Trans. Power Electron. 33 8101 doi: 10.1109/TPEL.2017.2771297
|
[17] |
Ashpis D E, Laun M C and Griebeler E L 2017 AIAA J. 55 2254 doi: 10.2514/1.J055816
|
[18] |
Zhang T F et al 2022 Plasma Sci. Technol. 24 114004 doi: 10.1088/2058-6272/ac742c
|
[19] |
Rodrigues F, Pascoa J and Trancossi M 2018 Exp. Therm. Fluid Sci. 90 55 doi: 10.1016/j.expthermflusci.2017.09.005
|
[20] |
Shen L, Chen Z N and Wen C Y 2020 AIAA J. 58 3368 doi: 10.2514/1.J059264
|
[21] |
Nishida H, Nakai K and Matsuno T 2017 AIAA J. 55 1852 doi: 10.2514/1.J055560
|