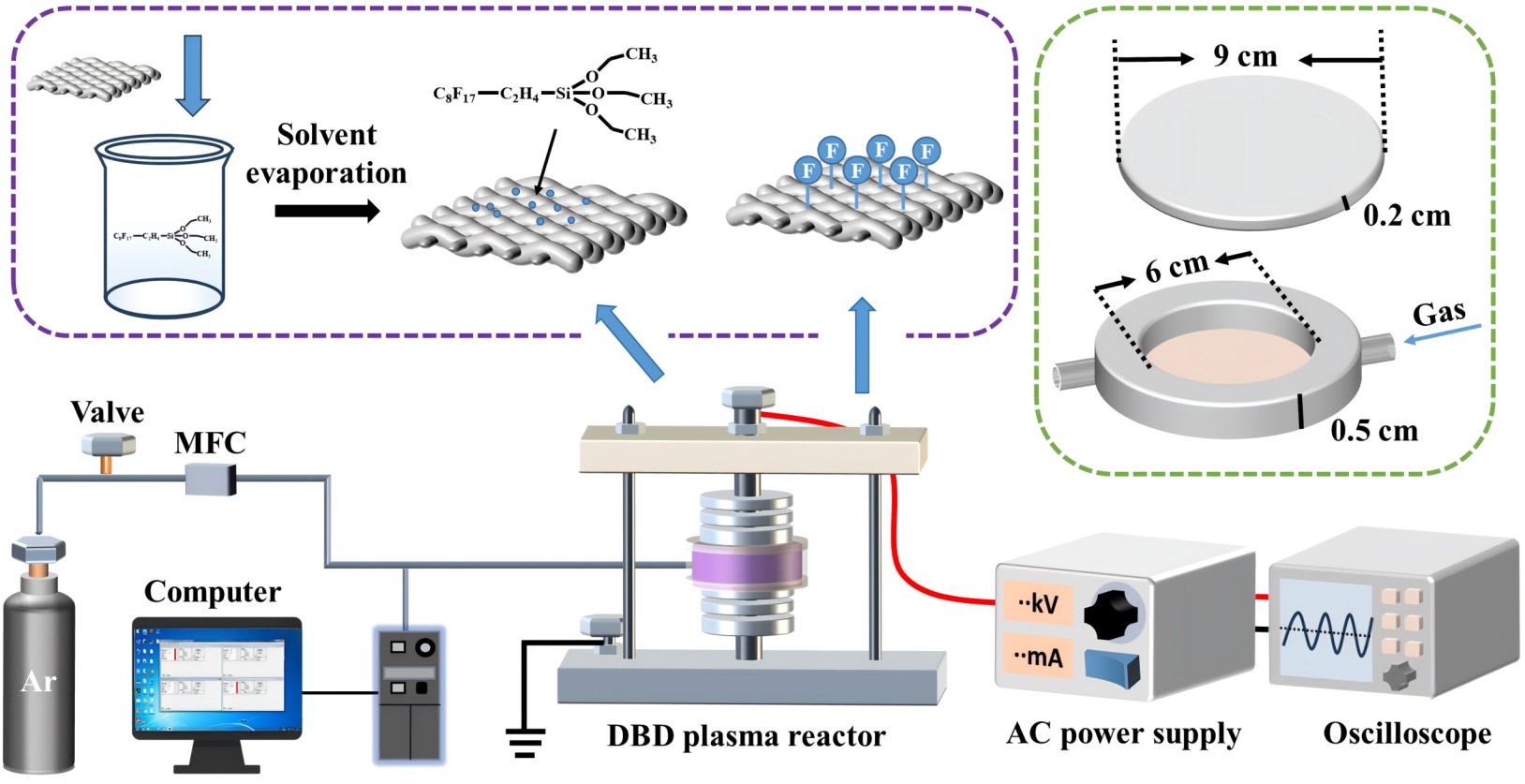
Citation: | Jian SHEN, Fajun WANG, Wei WEI, Jie MA, Junjie WANG, Liangliang LIN. Surface modification of fabrics using dielectric barrier discharge plasma for improved antifouling performance[J]. Plasma Science and Technology, 2025, 27(1): 014001. DOI: 10.1088/2058-6272/ad8da6 |
Surface modification of fabrics is an effective way to endow them with antifouling properties while still maintaining their key advantages such as comfort, softness and stretchability. Herein, an atmospheric pressure dielectric barrier discharge (DBD) plasma method is demonstrated for the processing of silk fabrics using 1H, 1H, 2H, 2H-perfluorodecyltriethoxysilane (PFDS) as the precursor. The results showed the successful grafting of PFDS groups onto the surface of silk fabrics without causing damage. Meanwhile, the gas temperature is rather low during the whole processing procedure, suggesting the non-equilibrium characteristics of DBD plasma. The influence on fabrics of the processing parameters (PFDS concentration, plasma treatment time and plasma discharge power) was systematically investigated. An optimum processing condition was determined to be a PFDS concentration of 8wt%, a plasma processing time of 40 s and a plasma power of 11.87 W. However, with prolonged plasma processing time or enhanced plasma power, the plasma-grafted PFDS films could be degraded. Further study revealed that plasma processing of silk fabrics with PFDS would lead to a change in their chemical composition and surface roughness. As a result, the surface energy of the fabrics was reduced, accompanied by improved water and oil repellency as well as enhanced antifouling performance. Besides, the plasma-grafted PFDS films also had good durability and stability. By extending the method to polyester and wool against different oil-/water-based stains, the DBD plasma surface modification technique demonstrated good versatility in improving the antifouling properties of fabrics. This work provides guidance for the surface modification of fabrics using DBD plasma to confer them with desirable functionalities.
With the development of human society and improved quality of life, there has been increasing demand for comfortable fabrics with desirable functionalities. However, most fabrics can be easily contaminated by water-/oil-based stains, with the stain types varying widely among different conditions and environments [1]. In general, contaminated fabrics not only have poor appearance and low value but also reduced quality, and may even lose their original properties [2]. Thus, washing or other decontamination methods have to be performed in a timely manner to maintain the appearance and performances of fabrics. On the other hand, decontamination of fabrics often consumes large amounts of water, and may cause water and microfiber pollution [3]. Regular washing of fabrics also deteriorates their appearance and properties [4]. To meet consumer demands, great effort has been devoted to developing comfortable and multi-functional fabrics with excellent antifouling properties.
Surface modification of fabrics is an effective way to improve the functionality of textile fibers without affecting their bulk characteristics [5]. By changing the composition or structure of fibers, their properties also change, for example their surface energy, roughness, wettability and dyeability. Water and oil repellency is one of the most common functional properties imparted to protective clothing [6]. When the surface energy of fibers is lower than the surface tension of water or oil, it will cause water and oil droplets to undergo a pearling phenomenon and be repelled from the surface of the fibers, resulting in water and oil repellency and the accompanying antifouling performance [7].
In general, the methods for modifying fabrics can be divided into two groups: chemical modification and physical modification. The former deals with changing fiber composition while the latter addresses changes in fiber structure [8]. Nonetheless, existing approaches still have undesirable consequences such as increased waste production, time- and energy-consuming processing methods, unpleasant working conditions, and so on [9]. Therefore, it is essential to develop a simple, sustainable and efficient method for the modification of fabrics with good water and oil repellency.
Dielectric barrier discharge (DBD) plasma treatment has been regarded as a promising alternative to conventional surface modification methods [10]. Owing to its non-equilibrium characteristic, the electron temperature is extremely high (104‒105 K) while the gas temperature is close to room temperature [11]. Thus, DBD plasma is particularly favored for the surface modification of temperature-sensitive materials such as polymers, fabrics, bio-materials, etc. The introduction of suitable precursors to DBD plasma has the potential for rapid, uniform and cost-effective processing of materials with desirable long-lasting properties [12]. Currently it has been applied for the surface modification of various materials, for example the treatment of basalt fibers with siloxane for enhanced thermal insulation performance [13], the processing of aramid fabrics with a C6 fluorine compound to improve washing durability [14] and the modification of polyimide films with methyltrimethoxysilane for increased thermal conductivity [15]. However, to the best of our knowledge there has still been no work focusing on the treatment of temperature-sensitive silk fabrics to endow them with excellent water and oil repellency, thus improving their antifouling performance.
When it comes to precursors, the grafting of fluorine-based compounds on materials is often characterized by excellent chemical and thermal stability, high durability and reduced surface energy [16]. This is due to the strong C–F bond as well as the large size of the fluorine atoms that can protect the carbon backbone of polymers from chemical attack [17]. Therefore, plasma surface modification of fabrics with fluorine-based compounds can endow them with water and oil repellency and antifouling performance. In the present work, a DBD plasma setup was applied for the surface modification of fabrics using 1H, 1H, 2H, 2H-perfluorodecyltriethoxysilane (PFDS) precursor. The characteristics of the DBD plasma discharge and optical emission spectrum during typical experiments were first analyzed. By selecting silk fabrics as a research model, processing parameters such as the PFDS concentration, plasma treatment time and plasma power were then explored and optimized, followed by an assessment of the durability of the plasma-grafted films. Afterwards, the DBD plasma method was extended to polyester and wool fabrics against different oil-/water-based stains to evaluate the versatility of the technique. Finally, the DBD plasma surface modification process is discussed based on our experimental results.
PFDS (⩾ 97%) and ethanol (AR grade, \geqslant 99.7%) were obtained from Adamas Reagents Co., Ltd. Silk, polyester and wool fabrics were purchased from the Shanghai Textile Supervision Institute. High-purity argon gas (> 99.999%) was purchased from Wuxi Taihu Gas Co., Ltd.
In the present work a DBD plasma setup was utilized for the surface modification of fabrics, as shown in figure 1. A detailed configuration of the setup can be found in our previous work [18]. In brief, a quartz reactor that functioned as the dielectric barrier was placed between two stainless-steel (SS) plates. The upper SS plate was connected to a CTP-2000K AC high-voltage power supply (Nanjing Suman Electronics Co., Ltd., China), while the lower SS plate was grounded. The quartz reactor is composed of a dish (diameter 9 cm, thickness 0.5 cm) and a flat plate (diameter 9 cm, thickness 0.2 cm), with a hollow sample cell (diameter 6 cm, depth 0.2 cm) between them in which to place samples. The reactor was also connected to an argon cylinder, and the argon flow rate can be adjusted by a mass flow controller (Bronkhorst High-Tech B.V.).
In a typical procedure, a certain amount of PFDS was dissolved in ethanol to form the reagent solution with different PFDS concentrations. Target fabrics (2 cm × 2 cm) were washed with ethanol solutions to remove possible contaminants. Then the fabrics were immersed in the reagent solution for 1 h to absorb precursors, before being dried in air and carefully transferred to the quartz reactor for plasma processing. Before each operation, an argon flow of 30 sccm was introduced into the reactor for 5 min to get rid of any impurities from the air. Upon the supply of high-voltage power to the electrodes, plasma discharges were formed within the reactor. Precursors are dissociated and grafted onto the surface of fabrics to endow them with water- and oil-repellent properties. During every experiment, waveforms of applied voltage (V) and electric charge (Q) were recorded by a Tektronix-TBS1102 digital oscilloscope. After the desired processing time the plasma was switched off. The plasma-treated samples were removed from the reactor, washed and dried in air for further characterization.
The plasma surface modification process was in situ characterized by an HR4000 optical emission spectrometer (OES; Ocean Optics, Inc.). The functional groups were analyzed using a Nicolet 6700 infrared spectrometer (Seymour Fisher Technology Co., Ltd.). The wettability of samples was evaluated by an FTA 1000 contact angle instrument (First Ten Angstroms, USA). The chemical composition and bonding configuration were characterized by a Kratos Axis Ultra DLD x-ray photoelectron spectrometer (XPS; Shimadzu Kratos Inc., Japan). The surface morphology of fabrics was observed using an S-4800 scanning electron microscope (SEM; Hitachi Corporation, Japan), equipped with an energy dispersive x-ray spectrometer (EDX) to examine the elemental composition and distribution. The surface topography was analyzed by a VHX-1000 super depth-of-field microscope (SDFM; Keyence, Japan) as well as a Multimode 8 atomic force microscope (AFM; Bruker, Germany). Thermogravimetric (TG) analysis was performed using a TGA/1100SF thermal gravimetric analyzer (Mettler-Toledo Inc.) at a heating rate of 10 °C min−1 in an air atmosphere. The durability of the plasma-deposited films was assessed by a M906 vertical decontaminator (Research Institute of Daily Chemical Industry, China), with an agitation speed of 120 r/min at 30 °C and a washing cycle of 20 min.
To gain a general overview of the plasma surface modification process, the discharge characteristics of DBD plasma were studied. Figure 2(a) shows a typical V–Q diagram recorded during an experiment. One can see periodic sinusoidal voltage waveforms with a peak-to-peak value of 8.0 kV and a cycle period of 55 μs. The energy dissipated in the DBD plasma can be calculated from the corresponding Lissajous curve (figure 2(b)) by the following formula [19]:
\overline{P}=\frac{1}{T}\oint V_{\mathrm{a}}\mathrm{d}Q_{\mathrm{m}}, | (1) |
where \overline P is the averaged plasma power, T is the AC cycle period, Va is the instantaneous voltage and Qm is the instantaneous capacitor charge. In this way, the plasma power is calculated to be 11.87 W.
Figure 2(c) shows a representative optical emission spectrum recorded during an experiment. Pronounced peaks of Ar atomic transitions (3p54p–3p54s) are observed in the wavelength range of 690‒950 nm [20]. Emission bands of the nitrogen second positive system are also detected between 330 nm and 410 nm, and can be attributed to N2 from the air [21]. The existence of these spectral features suggests that the DBD plasma has a high density of neutral-reactive particles [22]. However, emission bands of the precursor have not been detected by the OES, which could be due to their rather low content. Figure 2(d) shows the evolution of gas temperature during a typical experiment. The temperature gradually increases from 25.6 °C to 54.0 °C with extension of the plasma processing time from 0 min to 20 min, suggesting the non-equilibrium characteristics of DBD plasma. Such a property is especially favored for the surface modification of fabrics, where plasma will not cause thermal damage to the bulk of the material.
By tuning processing parameters such as the PFDS concentration, plasma treatment time and plasma discharge power, their influence on the wettability of silk fabrics was investigated. Figure 3 shows the evolution of the water contact angle and chili oil contact angle on silk fabrics after DBD plasma processing under different conditions. Both the water and oil contact angles initially increase with the increase in precursor concentration from 2wt% to 8wt%, indicating improved water and oil repellency (figure 3(a)). This is due to the grafting of PFDS onto the surface of the fabrics, leading to a reduced fabric surface energy [23]. With further rise in the precursor concentration, the water and oil contact angles become stable. Therefore, a PFDS concentration of 8wt% is chosen for further study. Figure 3(b) shows the contact angles of water and oil on the surface of fabrics that have been treated with plasma for different times. The original silk fabrics without DBD plasma treatment easily absorb water and oil. After plasma processing, the water and oil contact angles increase and reach maximum values at 40 s. The elevated contact angles with the plasma processing time indicate that PFDS molecules have been successfully grafted onto the fabric surface. However, with prolonged reaction time, the contact angles exhibit a decreasing trend, which is attributed to the degradation of the polymers [24]. The same phenomenon was also observed in our previous research, where the plasma-grafted polymers were degraded after long plasma exposure times [25]. Thus, a plasma processing time of 40 s was selected for further study. Similarly, the contact angles of water and oil on the fabrics initially increase with increase in plasma power, and reach maximum values at 11.87 W. Further increase in the plasma power will lead to reduced water and oil contact angles (figure 3(c)). This is because the density of reactive species is relatively low at small plasma powers [26]. With the increase in plasma power more reactive species are generated, leading to an improved surface modification effect. However, once the plasma power exceeds a certain value, the plasma-grafted polymers will be degraded. Therefore, further study was carried out at a plasma power of 11.87 W. Furthermore, in all cases, the water contact angles are larger than the oil contact angles under the same conditions. This is because silk fabrics are rich in proteins, consisting of hydrophobic groups such as –CH3.
Fourier transform infrared (FTIR) analysis was performed to analyze the functional groups on the surface of fabrics before and after DBD plasma processing, as shown in figure 4. Both samples display a similar IR spectrum, suggesting that the samples have the same main functional groups. Specifically, the strong absorption band at 3276 cm−1 is indexed to the stretching vibration of the N–H group. The prominent bands at 1617 cm−1 and 1518 cm−1 are attributed to the C=O stretching vibration of amide I and the N–H bending vibration of amide II, respectively, whereas the band at 1226 cm−1 is assigned to the C–N stretching vibration of amide III [27, 28]. After plasma treatment these bands are unchanged, revealing that the bulk material has not been affected. On the other hand, plasma processing also leads to the generation of new absorption bands in the 850‒1300 cm−1 range, which can be related to the Si–C, Si–O–Si and C–F groups. In detail, the appearance of new absorption bands at 1153 cm−1 and 1206 cm−1 can be explained by the C–F stretching vibration [29]. Two new absorption bands at 1078 cm−1 and 1104 cm−1 are due to the stretching vibration of Si–O–Si skeleton. A prominent band at 893 cm−1 is attributed to the Si–C stretching vibration. Therefore, the FTIR spectrum confirms the graft of PFDS molecules onto the surface of silk fabrics [30].
By tuning the plasma processing time in the range of 40‒120 s, its influence on the chemical composition and distribution of silk fabrics was examined using SEM-EDX analysis (figure 5). The bare silk fabrics merely consist of C, O and N elements, which is reasonable since silk is a natural protein fiber (figure 5(a)). However, after plasma processing, one can clearly see the existence of F and Si elements in all EDX spectra. These elements fit well with the overall region of the fabrics, suggesting that the PFDS-based compounds have been uniformly and effectively grafted onto their surface. Furthermore, with the extension of the plasma processing time from 40 to 120 s, the intensities of Si and F signals decrease (figures 5(b)‒(d)). The reduced content of Si and F with a prolonged processing time suggests that the plasma-grafted polymers were degraded by plasma impacts, in agreement with the wettability test.
The elemental composition and bonding configuration of the bare silk fabrics as well as the silk fabrics modified by DBD plasma for 40 s and 120 s were further studied by XPS characterization (figure 6). For the silk fabrics without plasma treatment, only C, N and O were detected, which are the main constituents of the silk fiber itself. After plasma processing, elemental signals relating to Si and F are seen (figure 6(a)). This suggests that PFDS molecules have been grafted onto the surface of the fabrics. The rather strong F signal is because XPS is a highly surface-specific analytical technique for probing the elemental composition and bonding states in the outermost 2‒10 nm of a solid surface. In this work, PFDS molecules are grafted onto the surface of the silk fabrics, thus giving a strong F signal in the XPS spectra. Compared with the sample modified by plasma for 40 s, a prolonged plasma processing time (120 s) leads to a decrease in the Si and F content, which is ascribed to the degradation of plasma-grafted films. High-resolution C 1s XPS spectra of the above samples were used to better understand the bonding configurations. For the silk fabrics prior to plasma treatment, the C 1s band can be deconvoluted into three components, namely C=O (288.1 eV), C–O/C–O–C (286.1 eV) and C–C bonds (284.7 eV), which are typical chemical bonds of silk fibers (figure 6(b)) [31, 32]. As to the silk fabrics processed by plasma for 40 s, deconvolution of the C 1s band suggests the formation of fluorinated groups on the surface of the silk fabrics, as reflected by the presence of CF2 (291.3 eV) and CF3 (293.5 eV) bonds (figure 6(c)) [33, 34]. However, after plasma processing for 120 s, the intensities of the CF2 and CF3 bonds considerably decrease, due to the degradation of the PFDS films (figure 6(d)).
The morphology of silk fabric samples before and after DBD plasma modification for 40 s was first examined by SDFM, as shown in figures 7(a)‒(d). Both samples exhibit similar morphology in the SDFM images, where highly oriented fibers of triangular shape and with a shiny surface are seen. However, no visual difference is discerned from the microscope images, which can be attributed to the rather low resolution of the microscope. This in turn suggests that plasma processing will not damage the fabrics and cause a reduced appearance. SEM and AFM analysis were further applied to better examine the surface morphology and topography of the samples. The SEM images of both samples exhibit a smooth appearance at the micron scale [35]. Closer observation reveals that plasma processing will introduce a thin layer onto the silk fabrics (figures 7(e) and (f)). However, AFM images at the nanoscale show that the sample prior to plasma processing displays a rough surface, in contrast to the smooth surface of the sample after plasma surface modification (figures 7(g) and (h)). This can be explained by the deposition of a thin layer onto the fabrics. The morphological difference between the samples is also clearly seen in the three-dimensional AFM images, in which the surface of the fabrics becomes more uniform and smoother after plasma processing (figures 7(i) and (j)).
TG analysis was performed to evaluate the thermal behavior and decomposition process of silk fabrics before and after plasma treatment, as shown in figure 8. The mass loss of both samples is measured to be 8% in the temperature range of 50 °C‒100 °C, with an endothermic peak observed in the differential thermogravimetry (DTG) curve. This is due to the dehydration of free water from the samples. The second endothermic peak appears at 270 °C‒380 °C, and is attributed to the thermal decomposition of silk proteins [36]. As mentioned for figure 2(d), the gas temperature during the reaction is lower than 100 °C during a typical experiment and will not damage the silk proteins. Furthermore, compared with the sample without plasma treatment, the endothermic peaks of the plasma-modified sample are located at higher temperatures, with reduced mass loss observed in the TG curve, indicating that DBD plasma processing leads to improved thermal stability.
To evaluate the practicality of the developed technique, the durability of water and oil repellency of plasma-modified silk fabrics was investigated. Figure 9(a) shows the evolution of the water and oil contact angles of the samples stored at ambient temperature for 30 d, in which a slightly decreasing trend is observed. Specifically, the water contact angle decreases from 151.0° to 143.1°, and the oil contact angle decreases from 139.5° to 133.1°. Therefore, the sample still possesses good water and oil repellency properties after 30 d. Figure 9(b) shows the evolution of the water and oil contact angles of the samples washed by a vertical decontaminator for 10 cycles. Each cycle lasts for 20 min. It is seen that both the water and oil contact angles remain larger than 130° even after 10 cycles, suggesting stable water and oil repellency of the plasma-modified samples. Therefore, the developed DBD plasma surface modification can confer silk fabrics with durable and stable water and oil repellency.
As demonstrated, the grafting of PFDS molecules onto the surface of silk fabrics leads to reduced surface energy as well as increased water and oil repellency, thus improving the antifouling performance of fabrics. To study the versatility of the plasma surface modification method, polyester and wool fabrics were studied as substrates. All samples were processed in the same manner, and treated by DBD plasma for 40 s, with a PFDS concentration of 8wt% and plasma power of 11.87 W. Meanwhile, different types of stains were dropped onto the fabrics to examine the water and oil repellency, including milk, soy sauce, peanut oil, reactive blue dye and chili oil. For the silk and polyester fabrics without plasma processing, all the stains penetrated the fabrics easily, making them heavily contaminated (rows 1 and 2 in figures 10(a) and (b)). As for the wool fabrics, due to the existence of a natural hydrophobic layer that can repel moisture they are able to prevent water-based stains to some extent, but are still easily contaminated by oil-based stains (row 3 in figures 10(a) and (b)) [37]. After plasma processing, all the samples demonstrate much improved water and oil repellency. The drops of water-/oil-based stains form a spherical shape on the surface of the fabrics instead of penetrating them (figures 10(c) and (d)). This is due to the reduced surface energy of fabrics after plasma grafting of PFDS molecules. Thus, the plasma surface modification technique can improve the antifouling performance of fabrics, which holds great promise for the generation of antifouling coatings on the surface of target materials.
Based on the above results, figure 11 shows a schematic process for DBD plasma surface modification of fabrics. In a plasma medium a series of reactive species exist, such as electrons, metastable argon atoms (Ar*) and ions (Ar2+, Ar+) [38]. They can not only dissociate PFDS molecules to generate diverse fragments, but are also capable of activating the surface of fabrics by plasma impact. These PFDS fragments will then be grafted onto the surface of the fabrics to form a polymer layer and change the surface properties, such as surface composition, surface energy, surface roughness and wettability [39]. Compared with hydrocarbon structures, the fluorinated carbon structures of PFDS fragments have a lower surface free energy and higher hydrophobicity [40]. As a result, the water and oil repellency of fabrics are improved, and this is associated with their increased antifouling performance. On the other hand, due to the non-equilibrium feature of DBD plasma, the gas temperature remains close to room temperature and will not damage the bulk fabrics. Such characteristics are particularly favorable for the surface modification of temperature-sensitive materials.
Regarding the scaling-up strategies of the DBD plasma method, there are already some creative solutions. For instance, different configurations of DBD plasma reactor have been designed for industrial processing, such as a roll-to-roll DBD plasma reactor [41], a multiple parallel DBD plasma reactor [42], a DBD plasma-induced jet [43] and a DBD reactor with rotating dielectric barriers [44]. Another possible solution for scaling up of DBD plasma reactors is to maximize their operational potential, for example the optimization of reactor size, the gap between the electrodes, gas flow rate and gas composition [45].
In this work, an atmospheric pressure DBD plasma method was applied for the surface modification of fabrics using PFDS as the precursor, with the aim of reducing the surface energy of fabrics and improving their water and oil repellency. The discharge characteristics of DBD plasma and the optical emission spectrum recorded during plasma processing were studied, revealing the non-equilibrium characteristics of the plasma and the existence of a high density of reactive radicals. Silk fabrics were chosen as a research model. Processing parameters such as the PFDS concentration, plasma treatment time and plasma discharge power were studied and optimized. The optimum condition was found to be a PFDS concentration 8wt%, a plasma processing time of 40 s and a plasma power of 11.87 W. Complementary characterization was performed to analyze the fabrics before and after plasma treatment, suggesting the successful grafting of PFDS onto the surface of fabrics by plasma within a short time (40 s). As a result, the chemical composition and surface roughness of fabrics were altered, leading to reduced surface energy as well as improved water and oil repellency. The plasma-grafted PFDS films also demonstrate good durability and stability. On the other hand, it is noted that the plasma-grafted PFDS films could be degraded with prolonged plasma processing time. By extending the method to polyester and wool fabrics, the DBD plasma proved to have good versatility in enhancing the water and oil repellency of fabrics, endowing them with good antifouling performance against different oil-/water-based stains. The non-equilibrium feature of DBD plasma together with the green and efficient surface modification process is expect to raise interest in both the scientific research and industrial communities.
We would like to acknowledge the financial support from National Natural Science Foundation of China (Nos. 22078125 and 52004102) and Postdoctoral Science Foundation of China (No. 2023M741472).
[1] |
Guan L Y, Shi M W and Long J J 2023 J. CO2 Util. 67 102316 doi: 10.1016/j.jcou.2022.102316
|
[2] |
Xu Q B et al 2022 Fibers Polym. 23 944 doi: 10.1007/s12221-022-4624-z
|
[3] |
Volgare M et al 2021 Sci. Rep. 11 19479 doi: 10.1038/s41598-021-98836-6
|
[4] |
Cai G Q et al 2016 J. Surfactants Deterg. 19 901 doi: 10.1007/s11743-016-1823-x
|
[5] |
Shahidi S, Wiener J and Ghoranneviss M 2013 Surface modification methods for improving the dyeability of textile fabrics In: Günay M Eco-Friendly Textile Dyeing and Finishing Rijeka: InTech 2013: 270
|
[6] |
Ferrero F, Periolatto M and Tempestini L 2017 Coatings 7 60 doi: 10.3390/coatings7050060
|
[7] |
Kowalski M et al 2022 Materials 15 3825 doi: 10.3390/ma15113825
|
[8] |
Ahmad R, Hamid R and Osman S A 2019 Adv. Civ. Eng. 2019 5185806 doi: 10.1155/2019/5185806
|
[9] |
Lin H P et al 2020 Polymers 12 833 doi: 10.3390/polym12040833
|
[10] |
Morent R et al 2011 Plasma Process. Polym. 8 171 doi: 10.1002/ppap.201000153
|
[11] |
Lin L L and Wang Q 2015 Plasma Chem. Plasma Process. 35 925 doi: 10.1007/s11090-015-9640-y
|
[12] |
Rui L C et al 2022 Chem. Eng. Res. Des. 186 125 doi: 10.1016/j.cherd.2022.07.038
|
[13] |
Xiong C F et al 2024 Appl. Surf. Sci. Adv. 21 100594 doi: 10.1016/j.apsadv.2024.100594
|
[14] |
Sidding E A A et al 2020 Plasma Sci. Technol. 22 055503 doi: 10.1088/2058-6272/ab65dd
|
[15] |
Xiong C F et al 2023 Surf. Interfaces 37 102758 doi: 10.1016/j.surfin.2023.102758
|
[16] |
Dargaville T R et al 2003 Prog. Polym. Sci. 28 1355 doi: 10.1016/S0079-6700(03)00047-9
|
[17] |
Henry B J et al 2018 Integr. Environ. Asses. 14 316 doi: 10.1002/ieam.4035
|
[18] |
Tao Y M et al 2023 Plasma Sci. Technol. 25 085504 doi: 10.1088/2058-6272/acc14c
|
[19] |
Jiang H et al 2013 IEEE Trans. Diel. Elect. Insul. 20 1101 doi: 10.1109/TDEI.2013.6571423
|
[20] |
Crintea D L et al 2009 J. Phys. D: Appl. Phys. 42 045208 doi: 10.1088/0022-3727/42/4/045208
|
[21] |
Zhang Z Y et al 2024 React. Chem. Eng. 9 1541 doi: 10.1039/D4RE00011K
|
[22] |
Schuman T and Wolf R A 2020 Surf. Interfaces 18 100461 doi: 10.1016/j.surfin.2020.100461
|
[23] |
Molina R et al 2017 ACS Appl. Mater. Inter. 9 5513 doi: 10.1021/acsami.6b15812
|
[24] |
Zhang Y L et al 2016 Surf. Coat. Technol. 296 104 doi: 10.1016/j.surfcoat.2016.04.036
|
[25] |
Lin L L et al 2021 J. CO2 Util. 53 101752 doi: 10.1016/j.jcou.2021.101752
|
[26] |
Zhang X Y et al 2023 J. Mater. Res. Technol. 27 4213 doi: 10.1016/j.jmrt.2023.10.302
|
[27] |
Zhou W, Chen X and Shao Z Z 2006 Prog. Chem. 18 1514 (in Chinese) doi: 10.3321/j.issn:1005-281X.2006.11.014
|
[28] |
Wang S D and Zhang Y Z 2014 Fibers Polym. 15 1129 doi: 10.1007/s12221-014-1129-4
|
[29] |
Chen L et al 2015 RSC Adv. 5 40148 doi: 10.1039/C5RA00910C
|
[30] |
Medina-Dzul K et al 2015 J. Polym. Res. 22 45 doi: 10.1007/s10965-015-0677-7
|
[31] |
Song Y J et al 2023 Plasma Sci. Technol. 25 114001 doi: 10.1088/2058-6272/acd32b
|
[32] |
Lee J et al 2013 Materials 6 2007 doi: 10.3390/ma6052007
|
[33] |
Colin M et al 2023 Carbon 202 137 doi: 10.1016/j.carbon.2022.10.082
|
[34] |
Hozumi A, Kim B and McCarthy T J 2009 Langmuir 25 6834 doi: 10.1021/la804127z
|
[35] |
Hodak S K et al 2008 Appl. Surf. Sci. 254 4744 doi: 10.1016/j.apsusc.2008.01.110
|
[36] |
Mehraz L and Nouri M 2020 J. Nat. Fibers 17 371 doi: 10.1080/15440478.2018.1492492
|
[37] |
Hassan M M 2019 Colloids Surf. A: Physicochem. Eng. Aspects 581 123819 doi: 10.1016/j.colsurfa.2019.123819
|
[38] |
Wang J S et al 2018 Membranes 8 56 doi: 10.3390/membranes8030056
|
[39] |
Lin L L et al 2022 J. Taiwan Inst. Chem. Eng. 138 104467 doi: 10.1016/j.jtice.2022.104467
|
[40] |
Hayes L J 1976 J. Fluorine Chem. 8 69 doi: 10.1016/S0022-1139(00)82900-0
|
[41] |
Starostin S A et al 2015 Plasma Process. Polym. 12 545 doi: 10.1002/ppap.201400194
|
[42] |
Kazemi M and Taghvaei H 2021 Sep. Purif. Technol. 260 118236 doi: 10.1016/j.seppur.2020.118236
|
[43] |
Khan T M, Alves G A S and Iqbal A 2023 Sci. Rep. 13 77 doi: 10.1038/s41598-022-27294-5
|
[44] |
Liang C et al 2020 Sep. Purif. Technol. 235 116141 doi: 10.1016/j.seppur.2019.116141
|
[45] |
Lin L L et al 2021 Chem. Eng. J. 417 129355 doi: 10.1016/j.cej.2021.129355
|
[1] | Cheng FENG (冯诚), Yibo HU (胡一波), Chenggang JIN (金成刚), Lanjian ZHUGE (诸葛兰剑), Xuemei WU (吴雪梅), Wenli WANG (王文利). The effect of atmospheric pressure glow discharge plasma treatment on the dyeing properties of silk fabric[J]. Plasma Science and Technology, 2020, 22(1): 15503-015503. DOI: 10.1088/2058-6272/ab4c4e |
[2] | Amin JIANG (蒋阿敏), Chao YE (叶超), Xiangying WANG (王响英), Min ZHU (朱敏), Su ZHANG (张苏). Ion property and electrical characteristics of 60 MHz very-high-frequency magnetron discharge at low pressure[J]. Plasma Science and Technology, 2018, 20(10): 105401. DOI: 10.1088/2058-6272/aad379 |
[3] | XIN Qing (辛青), LI Zhongjian (李中坚), LEI Lecheng (雷乐成), YANG Bin (杨彬). Inactivation of Bacteria in Oil Field Injected Water by a Pulsed Plasma Discharge Process[J]. Plasma Science and Technology, 2016, 18(9): 943-949. DOI: 10.1088/1009-0630/18/9/11 |
[4] | LIU Wenzheng (刘文正), LEI Xiao (雷晓), ZHAO Qiang (赵强). Study on Glow Discharge Plasma Used in Polyester Surface Modification[J]. Plasma Science and Technology, 2016, 18(1): 35-40. DOI: 10.1088/1009-0630/18/1/07 |
[5] | CHANG Zhengshi(常正实), YAO Congwei(姚聪伟), MU Haibao(穆海宝), ZHANG Guanjun(张冠军). Study on the Property Evolution of Atmospheric Pressure Plasma Jets in Helium[J]. Plasma Science and Technology, 2014, 16(1): 83-88. DOI: 10.1088/1009-0630/16/1/18 |
[6] | LIU Wenzheng(刘文正), LI Chuanhui(李传辉). Study on the Generation Characteristics of Dielectric Barrier Discharge Plasmas on Water Surface[J]. Plasma Science and Technology, 2014, 16(1): 26-31. DOI: 10.1088/1009-0630/16/1/06 |
[7] | S. SHAHIDI, M. GHORANNEVISS. Sterilization of Cotton Fabrics Using Plasma Treatment[J]. Plasma Science and Technology, 2013, 15(10): 1031-1033. DOI: 10.1088/1009-0630/15/10/13 |
[8] | A. RASHIDI, S. SHAHIDI, M. GHORANNEVISS, S. DALALSHARIFI, J. WIENER. Effect of Plasma on the Zeta Potential of Cotton Fabrics[J]. Plasma Science and Technology, 2013, 15(5): 455-458. DOI: 10.1088/1009-0630/15/5/12 |
[9] | LIU Hongxia (刘红霞), LIU Yun (刘云). Investigation on the Effects and Mechanisms of PTFE Surface Modification by Low Pressure Plasma?[J]. Plasma Science and Technology, 2012, 14(8): 728-734. DOI: 10.1088/1009-0630/14/8/09 |
[10] | ZHONG Shao-Feng (钟少锋). Surface Modification of Polypropylene Microporous Membrane by Atmospheric- Pressure Plasma Immobilization of N,N-dimethylamino ethyl methacrylate[J]. Plasma Science and Technology, 2010, 12(5): 619-627. |
1. | Lin, A., Chen, L., Song, P. et al. Comparative study of dielectric barrier discharge characteristics of methane-air mixed He/Ar. Physics of Plasmas, 2025, 32(3): 033501. DOI:10.1063/5.0250842 |