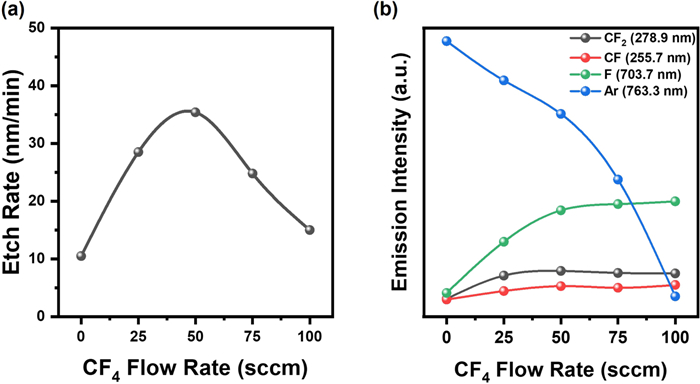
Citation: | Ping WANG, Guanghai HU, Ning YAN, Guosheng XU, Lingyi MENG, Zhikang LU, Lin YU, Manni JIA, Yifeng WANG, Liang CHEN, Heng LAN, Xiang LIU, Mingfu WU, Liang WANG. Experimental investigation of scrape-off layer blob high density transition in L-mode plasmas on EAST[J]. Plasma Science and Technology, 2022, 24(7): 075103. DOI: 10.1088/2058-6272/ac5f82 |
Lithium Beam Emission Spectroscopy systems in the outer midplane and divertor Langmuir probe arrays embedded in the divertor target plates, are utilized to investigate the scrape-off layer (SOL) blob transition and its relation with divertor detachment on EAST. The blob transition in the near SOL is observed during the density ramp-up phase. When the plasma density, normalized to the Greenwald density limit, exceeds a threshold of fGW~0.5, the blob size and lifetime increases by 2 – 3 times, while the blob detection rate decreases by about 2 times. In addition, a weak density shoulder is observed in the near SOL region at the same density threshold. Further analysis indicates that the divertor detachment is highly correlated with the blob transition, and the density threshold of blob transition is consistent with that of the access to the outer divertor detachment. The potential physical mechanisms are discussed. These results could be useful for the understanding of plasma-wall interaction issues in future devices that will operate under a detached divertor and high density conditions (over the blob transition threshold).
Wide bandgap, n-type zinc oxide (ZnO) with a wurtzite crystal structure is utilized in a range of applications such as optical devices, sensors and solar cells [1–4]. ZnO is also a very interesting material due to its advantages such as low cost and high physical and chemical stability [5, 6]. ZnO is also attracting attention as a suitable host material for doping with other metals [7]. Therefore, research into improving the electrical and optical properties by doping ZnO thin films with many metal elements (Al, Ga, B, In, etc) is in progress [8–10]. Al-doped ZnO (AZO), which has high transmittance and very low resistivity (< 8.5×10-5 Ω·cm), has attracted attention as an alternative to indium tin oxide (ITO) films [11, 12]. AZO thin films containing very low proportions of Al are advantageous because the main component is low-cost, non-toxic ZnO-based thin films. AZO is the best candidate as a transparent conductive oxide (TCO) material from the perspective of cost, availability and environmental friendliness [12, 13]. Therefore, AZO is considered as an alternative to TCO for solar cells, light-emitting diodes (LEDs) [14], photodetectors [15] and touch panels [16].
From a manufacturing point of view, TCO films with AZO can be easily etched to form microelectrodes for optoelectronic and display devices. The level of reduction of the pattern size that can be achieved with wet etching is limited due to the isotropic nature of this process, and it is difficult to achieve fine control of the process. In contrast, dry etching is advantageous for obtaining micro/nanoscale patterning due to its anisotropic characteristics and the ability to achieve fine process control. Therefore, the development and optimization of dry etching processes for AZO thin films are important challenges that must be overcome to enable accurate patterning and achieve stable device parameters. Dry etching of AZO has been studied by several groups [17, 18]. The etching properties and mechanism of etching AZO thin films in Cl-based plasma have been studied, demonstrating that Cl radicals play a dominant role in the etching process [19]. In the Cl-based plasma (such as Cl2 or BCl3) etching process, etching generally involves Zn–Cl bonds or compounds containing B [17, 20]. In contrast, the etching properties and etching mechanism of AZO thin films using F-based plasma have received little attention [18, 21]. Most studies focused on improving the device performance rather than the etching mechanism of AZO thin films. Thus, a detailed description of the etching characteristics is required.
In this study, the etching characteristics of AZO thin film and changes in the surface properties (e.g. work function, band gap, surface roughness, etc) of the thin film before and after etching were investigated according to the CF4/Ar plasma concentration. The plasma etching process is performed with adaptive coupled plasma (ACP) equipment. After the etching process, the surface roughness was confirmed using atomic force microscopy (AFM) and field emission scanning electron microscopy (FE-SEM), and changes in the chemical composition and work function of the AZO thin film were observed using X-ray photoelectron spectroscopy (XPS) and ultraviolet photoelectron spectroscopy (UPS). In addition, the transmittance and band gap changes of the AZO thin film were confirmed using UV–vis spectrophotometry.
AZO thin films were deposited on n-type Si (100) and glass substrates (Marienfeld, Germany) by radio frequency (RF) magnetron sputtering. Before deposition, the Si and glass substrates were sequentially ultrasonically cleaned with isopropyl alcohol (IPA), and DI water, and finally dried with nitrogen gas. AZO thin films were deposited using a ZnO/Al2O3 (98/2 wt.%) target. The AZO target, 2 inches in diameter and 1/8 inch thick, was bonded to copper-backed plates. The target and substrate were placed parallel to each other at a distance of 10 cm. After maintaining the initial vacuum of the chamber at 5.5×10-5 Torr for 3 h using a rotary pump and diffusion pump, Ar gas was injected using a mass flow controller. The RF magnetron sputtering system applied a power of 13.56 MHz to the electrodes, and the power input was controlled using a matching network system and RF generator. Before deposition of the AZO thin films, chamber stabilization and target cleaning were achieved by 10 min pre-sputtering with Ar plasma. After that, the AZO thin film was deposited on the substrate with an RF power of 60 W, Ar flow of 30 sccm, working pressure of 5×10-3 Torr, deposition temperature of 300 ℃ and deposition time of 60 min. Based on our previous experiments, AZO thin films exhibited the highest transparency and electrical conductivity properties under the above conditions [22].
The plasma etching process was performed using an ACP system. The ACP source consisted of a plate-shaped electrode in the center of the process chamber, which was spirally surrounded by a coil electrode [23]. The ACP source above the main process chamber was connected to a 13.56 MHz RF power supply. Another 2 MHz RF power supply was connected separately to the substrate to induce a bias power across the substrate. The main process chamber maintained the initial vacuum using rotary and turbo molecular pumps. By attaching a load-lock chamber to the ACP system, the system introduced the wafer into the process chamber while maintaining the process chamber under a high vacuum. An optical emission spectroscopy (OES) system was connected to the viewport of the main process chamber. The cooling system cooled the substrate. Since the etching parameters, such as the etch rate and surface roughness, are closely related to the temperature of the substrate surface, it is important to keep the substrate temperature constant [24]. The wafer substrate cooled by the chiller was maintained at 21 ℃.
The effect of the CF4/Ar ratio on the basic etching properties was investigated while maintaining the total flow rate of the gas at 100 sccm. Various etch parameters (RF power, bias power to the substrate, and process pressure) were used to evaluate the etching properties and etching mechanism of the AZO thin film. The etch rate as a function of etch parameters was investigated using a surface profiler (α-step 500, KLA Tencor). In addition, the surface roughness change and morphology of the AZO thin film were confirmed using AFM (NX-10, Park system) in tapping mode and an FE-SEM (Sigma 300, Carl Zeiss). For accurate FE-SEM measurements, a platinum coating was applied to the surface. Transmittance change according to process conditions was measured using a UV–vis spectrophotometer (Lambda 35, Perkin Elmer), and the band gap was calculated using the Tauc equation. XPS and UPS spectra (NEXSA, ThermoFisher Scientific) were acquired to analyze the changes in the chemical bonding and work function of the AZO thin film. The X-ray source for all measurements was the monochromated Al-Kα line at 1486.6 eV. The He I (21.22 eV) excitation line was used for UPS measurement; -10 V was applied to all samples during the UPS measurements to estimate the absolute work function value in the high binding energy (BE) cutoff region and the separation of the secondary electrons in the sample and the spectrometer.
In order to evaluate the basic etching characteristics of the AZO thin films under CF4/Ar gas, the etch rate of the AZO thin films was investigated as a function of the gas (CF4/Ar) composition. The other parameters were kept constant (total gas flow rate, RF power, bias power, process pressure and substrate temperature are 100 sccm, 500 W, 150 W, 15 mTorr and 21 ℃, respectively) during the etching process to investigate the effect of the CF4/Ar gas ratio.
Figure 1 shows the etch rate and OES for the AZO thin film with a variation in the CF4/Ar gas mixture ratio. To elucidate the etching mechanism of the AZO thin film, OES was used to analyze the active species in the CF4/Ar plasma. From the OES in figure 1(b), the dissociated species were identified as Ar (763.3 nm), CF (255.7 nm), CF2 (278.9 nm) and F (703.7 nm) [25, 26].
Figure 1(a) shows that the etch rate of the AZO thin film increases from 10.13 to 36.2 nm min-1 as the flow rate of CF4 gas increases from 0 to 50 sccm in the CF4/Ar plasma. The etch rate decreased from 36.2 to 16.8 nm min-1 as the flow rate of CF4 increased from 50 to 100 sccm. As shown in figure 1(b), the emission of the F radical was most intense when the CF4 flow rate was 100 sccm, whereas the emission of CF and CF2 did not change significantly with variation in the flow rate of the CF4 gas. After CF4/Ar plasma etching, the F components form non-volatile by-products, such as Al-F3 (melting point: 2250 ℃) and Zn-F2 (melting point: 872 ℃), on the surface of the AZO thin film. By-products with a high melting point remain on the surface of the AZO thin film and interfere with the etching process. These non-volatile by-products are easily removed by Ar+ sputtering. If the by-products are not strongly bombarded by the Ar+ ions, they remain on the surface of the AZO thin film. When the flow rate of CF4 is more than 50 sccm, the etch rate is reduced because of the lower Ar+ sputtering effect and increased production of F radicals. Therefore, increasing the number of chemical reactions does not affect the etch rate in the absence of strong ion bombardment. In addition, oxygen reacts with CF4 plasma to generate volatile by-products (such as COF) [27]. Consequently, etching is possible even when the flow rate of Ar is 0 sccm. The etch rate is maximal when the chemical reactions with CFx and F, and physical reactions such as Ar sputtering act simultaneously.
The change in the etch rate with variation in the other parameters is illustrated in figure 2. The CF4/Ar gas flow rate was fixed at 50/50 sccm for all conditions in figure 2. The correlation between the RF power and etch rate is shown in figure 2(a). The etch rate was measured by increasing the RF power in the range of 400–600 W. Bias power and process pressure were fixed at 150 W and 15 mTorr, respectively. As the RF power increased, the etch rate of the AZO thin film increased proportionally. Consequently, increasing the RF power increases the density of CFx, F radicals and Ar+ ions in the plasma. Higher RF power creates more radicals that can reach the surface of the AZO thin film, increasing the chemical and physical reactions. Figure 2(b) shows the change in the etch rate of the AZO thin film according to the increase in bias power from 50 to 150 W. The RF power was 500 W and the process pressure was 15 mTorr. As the bias power increased, the etch rate increased dramatically. Bias power is a process variable that controls the average energy of Ar+ ions participating in ion bombardment, which is a physical etching element, and the average energy of Ar+ ions increases in proportion to the applied bias power. This means that the ion sputtering effect increases as the bias power increases. As the bias power increases, the etch rate increases since the surface residues are easily removed by Ar+ sputtering. Figure 2(c) shows the change in the etch rate of the AZO thin film with variation in process pressure. The etch rate was measured by increasing the process pressure in the range of 10–20 mTorr. The RF power and bias power were 500 and 150 W, respectively. As the process pressure increases, the etch rate decreases. As the pressure increases, collisional recombination between particles increases. Consequently, the efficiency of the RF power is reduced [28]. Moreover, the effect of physical sputtering decreases because the DC bias across the sheath decreases as the pressure increases. The reduction in these physical effects and chemical reactions leads to a decrease in etch rate at higher process pressure [29].
XPS was used to observe the change in the composition of the AZO thin film according to the flow rate of CF4 gas. Samples were prepared under three conditions: (a) before etching, (b) after etching in CF4/Ar (= 50/50 sccm) plasma and (c) after etching in CF4 (= 100 sccm) plasma. For the etch process, RF power, bias power and process pressure were fixed at 500 W, 150 W and 15 mTorr, respectively.
Figure 3(a) shows the XPS narrow scan profile of the surface of the AZO thin film in the Al 2p region. The Al 2p peak is located at ~73.95±0.1 eV, which corresponds to the characteristic peak of Al–Ox before CF4/Ar plasma etching. The peak of metallic aluminum at 72.7±0.06 eV did not appear in the XPS profile [30]. As the flow rate of CF4 increased, this peak was observed at 75.2 eV, related to Al–Fx [31]. A comparison between the Al 2p profiles of the as-deposited and etched surfaces shows that the Al–Ox peak became less intense in the case of the etched surface. This indicates that Al–Ox bonds are broken, Al reacts with F radicals, and O also reacts with F and CFx to form COF bonds. Figure 3(b) shows the XPS narrow scan profile of the Zn 2p peak. The two peaks at 1044.54 and 1021.32 eV are characteristic of the Zn 2p1/2 and Zn 2p3/2 states, respectively. After etching in CF4/Ar and CF4 plasma, the Zn 2p peak was shifted by 1.3 and 1.4 eV towards higher BE, respectively (figure 3(b)). This BE shift is attributed to a change in the chemical binding state caused by the reaction of F and CFx radicals with Zn atoms on the surface of the AZO thin film. Because Zn binds more stably with F than with O (zinc fluoride ∆fGo=-713.3 kJ mol-1, zinc oxide ∆fGo=-320.5 kJ mol-1), the O atom is more likely to be substituted by F [32, 33].
Figures 4(a)–(c) show the narrow scan spectra of the O 1 s region for the surface of the AZO thin film before and after etching in CF4/Ar and pure CF4 plasma, respectively. For all samples, the O 1s peak was deconvoluted into three peaks. The low BE component centered at 530.1±0.2 eV is assigned to metal-oxide bonds (denoted as OⅠ). The middle BE component centered at 531±0.2 eV is attributed to O vacancies (denoted as OⅡ). The high BE component at 532.1±0.2 eV is assigned to hydroxyl (OH) on the surface of the AZO thin film (denoted as OⅢ) [34]. When the flow rate of CF4 was increased to 50 sccm, the intensity of the OⅠ peak first decreased, and increased again when the flow rate of CF4 exceeded 50 sccm. This trend indicates that the metal-oxide bonds are broken by Ar+ sputtering, which increases the rate of the reaction of the F and CFx radicals with metal or O. The OⅡ peak became less intense as the flow rate of CF4 increased. F atoms can substitute oxygen or occupy oxygen vacancies in the ZnO structure. It is well known that F and O have a similar ionic radius, and the Zn–F bond is more stable than the Zn–O bond [35–37]. The OⅢ peak first gained intensity and then became less intense as the flow rate of CF4 increased. This is because the ratio of F present in the AZO thin film increases for the same reason as above. The F ion, which is the most electronegative ion, can also attract H atoms in the hydroxyl group that bind to the nearest O dangling bond to form an intermolecular F–HO H bond [35]. Table 1 shows the atomic percentage and relative strength of the O 1 s peak. Table 1 shows that as the atomic percentage of F increased, the atomic percentage of O decreased. The detailed changes in the intensity of the OⅠ, OⅡ and OⅢ peaks are presented in table 1. Through XPS analysis, it was confirmed that when the AZO thin film was etched using CF4/Ar plasma, Al–O and Zn–O bonds were broken and metal-F bonds were generated on the surface. It was also confirmed that F removed the O vacancies.
Atomic Percentage (%) | Relative Strength (%) | |||||||
Etching Condition | Al | Zn | O | F | OⅠ | OⅡ | OⅢ | |
As-dep | 4.09 | 48.7 | 47.21 | 0 | 45.86 | 35.66 | 18.47 | |
CF4/Ar | 3.12 | 35.11 | 22.6 | 39.17 | 39.81 | 30.56 | 29.62 | |
Pure CF4 | 2.98 | 35.27 | 22.5 | 38.2 | 51.44 | 23.94 | 23.64 |
The change in the work function was measured using UPS analysis. Since it is very difficult to measure the Fermi edge of the oxide films, the work function was determined based on the Fermi level of Au, as a reference sample. The work function (Φ) was obtained according to equation (1).
Φ=hv-|Ecutoff-EF|. | (1) |
Here, hv is the photon energy of the He I source (21.2 eV). Ecutoff and EF represent the cutoff energy and Fermi-level energy, respectively.
Figure 5 shows the changes in the work function (from the UPS data) with variation in the flow rate of CF4 gas. The work function increased from 4.19 to 4.44 eV as the flow rate of CF4 gas increased. The CF4 plasma affects the formation of F radicals and metal bonds on the surface of the AZO thin film and reduces the number of O vacancies. This reaction contributed significantly to the change in the work function. Moreover, free electrons may be generated by replacing O ions with F ions because of the difference in the electrovalency of the O ions (
OxO+F-→F·O+e- | (2) |
Therefore, the electron concentration of AZO increased, shifting the Fermi level to the conduction band, and the work function also increased.
Figure 6 shows changes in the transmittance spectra with variation in the flow rate of CF4 gas. Figures 6(a) and (b) show the transmittance and optical bandgap energy, respectively. In figure 6(a), the transmittance in the visible light region is maintained at 80% or more even after plasma etching. The optical band gap can be determined from the transmittance spectra. The optical band gap was calculated using the tauc equation (equation (3)).
(αhv)=A(hv-Eg)n. | (3) |
Here, α is the absorption coefficient, A is a proportionality constant, Eg is the band gap of the material, and n depends on the type of transition. The optical bandgap energy of the AZO thin film in the 'As-dep' sample was 3.46 eV. As the flow rate of CF4 gas increased, the bandgap energy increased by 0.06 eV (from 3.46 to 3.52 eV). The optical bandgap energy appeared to increase due to a reduction in the number of O vacancies by F radicals on the AZO surface.
The surface roughness of transparent conductive thin films is an important feature for many applications and is well known to have a significant impact on device performance [38]. Therefore, it is important to measure the surface roughness of the AZO thin film after plasma etching.
Figure 7 shows the surface roughness of the AZO thin film with variation in the flow rate of CF4 gas. After etching with CF4/Ar plasma, the roughness of the film was reduced under all conditions compared to that of the As-dep thin film. In the CF4/Ar plasma, the AZO thin film is etched by the sputtering effect and chemical reaction, resulting in reduced surface roughness. In addition, as the flow rate of CF4 increased, the surface roughness appeared to increase due to an increase in the amount of by-products on the surface of the AZO thin film.
Figure 8 is an FE-SEM image of the surface of the AZO thin film before and after plasma etching. The surface of the AZO thin film is changed and becomes smooth after plasma etching. In particular, it is confirmed that the surface of the AZO thin film etched at the CF4/Ar ratio of 50:50 is the smoothest. This result supports the change in surface roughness after etching using AFM analysis.
This study shows the etching characteristics and surface properties of AZO thin films in CF4/Ar plasma. The highest etch rate was achieved with a CF4/Ar ratio of 50:50 sccm. When the flow rate of CF4 gas exceeded 50 sccm, the etch rate decreased because the non-volatile by-products generated on the AZO surface increased as the flow rate of CF4 gas increased, and the Ar sputtering effect decreased. Thus, the by-products were not easily removed. XPS analysis demonstrates that when the AZO thin film is etched using CF4/Ar plasma, metal-F bonds are formed by the F radicals to generate a non-volatile by-product. Moreover, the F ion replaces the O ion to create a free electron in the AZO thin film. This causes an increase in the work function and bandgap energy from 4.19 to 4.44 eV and 3.46 to 3.52 eV, respectively. In contrast, after plasma etching, the surface roughness decreased under all conditions, where the minimum roughness was 6.04 nm.
The authors would like to acknowledge the support and contributions of the EAST team. The work is supported by the National Key R&D Program of China (Nos. 2017YFE0301300, 2017YFA0402500, 2019YFE03030000), Institute of Energy, Hefei Comprehensive National Science Center (Nos. GXXT2020004, 12105187), National Natural Science Foundation of China (Nos. 11922513, U19A20113, 11905255, 12005004), Anhui Provincial Natural Science Foundation (No. 2008085QA38), and China Postdoctoral Science Foundation (No. 2021M702245).
[1] |
Antar G Y et al 2001 Phys. Rev. Lett. 87 065001 doi: 10.1103/PhysRevLett.87.065001
|
[2] |
Goodall D H J 1982 J. Nucl. Mater. 111–112 11 doi: 10.1016/0022-3115(82)90174-X
|
[3] |
Zweben S J 1985 Phys. Fluids 28 974 doi: 10.1063/1.865069
|
[4] |
Endler M et al 1995 Nucl. Fusion 35 1307 doi: 10.1088/0029-5515/35/11/I01
|
[5] |
Endler M 1999 J. Nucl. Mater. 266–269 84 doi: 10.1016/S0022-3115(98)00659-X
|
[6] |
Umansky M V et al 1998 Phys. Plasmas 5 3373 doi: 10.1063/1.873051
|
[7] |
LaBombard B et al 2001 Phys. Plasmas 8 2107 doi: 10.1063/1.1352596
|
[8] |
Neuhauser J et al 2002 Plasma Phys. Control. Fusion 44 855 doi: 10.1088/0741-3335/44/6/316
|
[9] |
Boedo J A et al 2001 Phys. Plasmas 8 4826 doi: 10.1063/1.1406940
|
[10] |
Xu G S et al 2010 Phys. Plasmas 17 022501 doi: 10.1063/1.3302535
|
[11] |
Asakura N et al 2009 J. Nucl. Mater. 390–391 364 doi: 10.1016/j.jnucmat.2009.01.073
|
[12] |
Garcia O E et al 2006 Plasma Phys. Control. Fusion 48 L1 doi: 10.1088/0741-3335/48/1/L01
|
[13] |
McCormick K et al 1992 J. Nucl. Mater. 196–198 264 doi: 10.1016/S0022-3115(06)80043-7
|
[14] |
D'Ippolito D A, Myra J R and Krasheninnikov S I 2002 Phys. Plasmas 9 222 doi: 10.1063/1.1426394
|
[15] |
Garcia O E et al 2007 J. Nucl. Mater. 363–365 575 doi: 10.1016/j.jnucmat.2006.12.063
|
[16] |
Rudakov D L et al 2005 Nucl. Fusion 45 1589 doi: 10.1088/0029-5515/45/12/014
|
[17] |
Greenwald M 2002 Plasma Phys. Control. Fusion 44 R27 doi: 10.1088/0741-3335/44/8/201
|
[18] |
Carralero D et al 2015 Phys. Rev. Lett. 115 215002 doi: 10.1103/PhysRevLett.115.215002
|
[19] |
Carralero D et al 2014 Nucl. Fusion 54 123005 doi: 10.1088/0029-5515/54/12/123005
|
[20] |
Carralero D et al 2017 Nucl. Fusion 57 056044 doi: 10.1088/1741-4326/aa64b3
|
[21] |
Vianello N et al 2017 Nucl. Fusion 57 116014 doi: 10.1088/1741-4326/aa7db3
|
[22] |
Loarte A et al 1998 Nucl. Fusion 38 331 doi: 10.1088/0029-5515/38/3/303
|
[23] |
Schwörer D et al 2020 Nucl. Fusion 60 126047 doi: 10.1088/1741-4326/ab8776
|
[24] |
Carralero D et al 2015 J. Nucl. Mater. 463 123 doi: 10.1016/j.jnucmat.2014.10.019
|
[25] |
Nielsen A H et al 2017 Plasma Phys. Control. Fusion 59 025012 doi: 10.1088/1361-6587/59/2/025012
|
[26] |
Wynn A et al 2018 Nucl. Fusion 58 056001 doi: 10.1088/1741-4326/aaad78
|
[27] |
Kirk A et al 2016 Plasma Phys. Control. Fusion 58 085008 doi: 10.1088/0741-3335/58/8/085008
|
[28] |
Kuang A Q et al 2019 Nucl. Mater. Energy 19 295 doi: 10.1016/j.nme.2019.02.038
|
[29] |
Yan N et al 2013 Plasma Phys. Control. Fusion 55 115007 doi: 10.1088/0741-3335/55/11/115007
|
[30] |
Wang Q et al 2019 Phys. Plasmas 26 072305 doi: 10.1063/1.5093790
|
[31] |
Xu J C et al 2016 Rev. Sci. Instrum. 87 083504 doi: 10.1063/1.4960181
|
[32] |
Zoletnik S et al 2018 Rev. Sci. Instrum. 89 063503 doi: 10.1063/1.5017224
|
[33] |
Wang Y F et al 2019 Fusion Eng. Des. 144 133 doi: 10.1016/j.fusengdes.2019.05.002
|
[34] |
Aumayr F and Winter H 1985 Ann. Phys. 497 228 doi: 10.1002/andp.19854970304
|
[35] |
Ming T F et al 2009 Fusion Eng. Des. 84 57 doi: 10.1016/j.fusengdes.2008.10.005
|
[36] |
Wang L et al 2019 Nucl. Fusion 59 086036 doi: 10.1088/1741-4326/ab1ed4
|
[37] |
Xu J C et al 2019 J. Instrum. 14 P06028 doi: 10.1088/1748-0221/14/06/P06028
|
[38] |
Stangeby P C 1993 Nucl. Fusion 33 1695 doi: 10.1088/0029-5515/33/11/I10
|
[39] |
Pitcher C S and Stangeby P C 1997 Plasma Phys. Control. Fusion 39 779 doi: 10.1088/0741-3335/39/6/001
|
[40] |
Birkenmeier G et al 2014 Plasma Phys. Control. Fusion 56 075019 doi: 10.1088/0741-3335/56/7/075019
|
[41] |
Huber A et al 2005 Plasma Phys. Control. Fusion 47 409 doi: 10.1088/0741-3335/47/3/002
|
[42] |
Ghim Y C et al 2012 Plasma Phys. Control. Fusion 54 095012 doi: 10.1088/0741-3335/54/9/095012
|
[43] |
Johnsen H, Pécseli H L and Trulsen J 1987 Phys. Fluids 30 2239 doi: 10.1063/1.866158
|
[44] |
Grulke O et al 2014 Nucl. Fusion 54 043012 doi: 10.1088/0029-5515/54/4/043012
|
[45] |
Zhang S B et al 2014 Plasma Sci. Technol. 16 311 doi: 10.1088/1009-0630/16/4/02
|
[46] |
Wang Y M et al 2013 Fusion Eng. Des. 88 2950 doi: 10.1016/j.fusengdes.2013.06.004
|
[47] |
Theiler C et al 2009 Phys. Rev. Lett. 103 065001 doi: 10.1103/PhysRevLett.103.065001
|
[48] |
Krasheninnikov S I, D'ippolito D A and Myra J R 2008 J. Plasma Phys. 74 679 doi: 10.1017/S0022377807006940
|
[49] |
Myra J R, Russell D A and D'Ippolito D A 2006 Phys. Plasmas 13 112502 doi: 10.1063/1.2364858
|
[50] |
Shesterikov I et al 2012 Nucl. Fusion 52 042004 doi: 10.1088/0029-5515/52/4/042004
|
[1] | Wei LIU (刘伟), Chundong HU (胡纯栋), Sheng LIU (刘胜), Shihua SONG (宋士花), Jinxin WANG (汪金新), Yan WANG (王艳), Yuanzhe ZHAO (赵远哲), LizhenLIANG (梁立振). Development of data acquisition and over-current protection systems for a suppressor-grid current with a neutral-beam ion source[J]. Plasma Science and Technology, 2017, 19(12): 125605. DOI: 10.1088/2058-6272/aa8cc1 |
[2] | CHANG Pengxiang (常鹏翔), WU Bin (吴斌), WANG Jinfang (王进芳), LI Yingying (李颖颖), WANG Xiaoguang (王小光), XU Handong (徐旵东), WANG Xiaojie (王晓洁), LIU Yong (刘永), ZHAO Hailin (赵海林), HAO Baolong (郝宝龙), YANG Zhen (杨振), ZHENG Ting (郑婷), HU Chundong (胡纯栋). The Influence of Neutral Beam Injection on the Heating and Current Drive with Electron Cyclotron Wave on EAST[J]. Plasma Science and Technology, 2016, 18(11): 1064-1068. DOI: 10.1088/1009-0630/18/11/02 |
[3] | CHEN Yuqian (陈俞钱), HU Chundong (胡纯栋), XIE Yahong (谢亚红). Analysis of Effects of the Arc Voltage on Arc Discharges in a Cathode Ion Source of Neutral Beam Injector[J]. Plasma Science and Technology, 2016, 18(4): 453-456. DOI: 10.1088/1009-0630/18/4/21 |
[4] | XIAO Jixiong (肖集雄), ZENG Zhong (曾中), XIA Donghui (夏冬辉), WANG Zhijiang (王之江), LIU Changhai (刘昌海). Effects of Boundary Current on Electromagnetic Dispersion Characteristics for a Relativistic Electron Beam[J]. Plasma Science and Technology, 2016, 18(1): 51-57. DOI: 10.1088/1009-0630/18/1/09 |
[5] | WANG Lei(王磊), HUANG Yiyun(黄懿赟), ZHAO Yanping(赵燕平), ZHANG Jian(张健), YANG Lei(杨磊), GUO Wenjun(郭文军). Structure Design and Analysis of High-Voltage Power Supply for ECRH[J]. Plasma Science and Technology, 2014, 16(11): 1079-1082. DOI: 10.1088/1009-0630/16/11/15 |
[6] | CAO Lihua(曹莉华), WANG Huan(王欢), ZHANG Hua(张华), LIU Zhanjun(刘占军), WU Junfeng(吴俊峰), LI Baiwen(李百文). Two-Dimensional Hybrid Model for High-Current Electron Beam Transport in a Dense Plasma[J]. Plasma Science and Technology, 2014, 16(11): 1007-1012. DOI: 10.1088/1009-0630/16/11/03 |
[7] | XIE Yahong(谢亚红), HU Chundong(胡纯栋), LIU Sheng(刘胜), JIANG Caichao(蒋才超), LIANG Lizhen(梁立振), LI Jun(李军), XIE Yuanlai(谢远来), LIU Zhimin(刘智民). The Arc Regulation Characteristics of the High-Current Ion Source for the EAST Neutral Beam Injector[J]. Plasma Science and Technology, 2014, 16(4): 429-432. DOI: 10.1088/1009-0630/16/4/24 |
[8] | HUANG Haihong(黄海宏), YAN Teng(晏腾), WANG Haixin(王海欣). Application of a Current and Voltage Mixed Control Mode for the New Fast Control Power Supply at EAST[J]. Plasma Science and Technology, 2014, 16(4): 420-423. DOI: 10.1088/1009-0630/16/4/22 |
[9] | CHENG Xian (程显), DUAN Xiongying (段雄英), LIAO Minfu (廖敏夫), et al.. The Voltage Distribution Characteristics of a Hybrid Circuit Breaker During High Current Interruption[J]. Plasma Science and Technology, 2013, 15(8): 800-806. DOI: 10.1088/1009-0630/15/8/16 |
[10] | Wu Di (吴迪), Lei Ming Kai (雷明凯), Zhu Xiao Peng (朱小鹏), Gong Ye (宫野). Numerical Study on the Two-Dimensional Temperature Fields of Titanium/Aluminum Double-Layer Target Irradiated by High-Intensity Pulsed Ion Beam[J]. Plasma Science and Technology, 2010, 12(5): 581-584. |
1. | Joo, Y.-H., Choi, J.-W., Hou, B. et al. Etching characteristics and surface modification of InGaSnO thin films under Cl2/Ar plasma. Plasma Science and Technology, 2023, 25(10): 105502. DOI:10.1088/2058-6272/acd588 |
2. | Li, Z., Li, L., Zhang, G. et al. AZO work function enhanced by oxygen plasma immersion ion implantation. Vacuum, 2023. DOI:10.1016/j.vacuum.2023.112038 |
3. | Petrova, D., Napoleonov, B., Minh, C.N.H. et al. The Effect of Post Deposition Treatment on Properties of ALD Al-Doped ZnO Films. Nanomaterials, 2023, 13(5): 800. DOI:10.3390/nano13050800 |
4. | Xu, K., Li, P., Wang, S. et al. Passivation of oxygen vacancy defects in conductive ZnO nanoparticles via low-temperature annealing in NF3. Journal of Physics D: Applied Physics, 2023, 56(8): 085301. DOI:10.1088/1361-6463/acb4a5 |
Atomic Percentage (%) | Relative Strength (%) | |||||||
Etching Condition | Al | Zn | O | F | OⅠ | OⅡ | OⅢ | |
As-dep | 4.09 | 48.7 | 47.21 | 0 | 45.86 | 35.66 | 18.47 | |
CF4/Ar | 3.12 | 35.11 | 22.6 | 39.17 | 39.81 | 30.56 | 29.62 | |
Pure CF4 | 2.98 | 35.27 | 22.5 | 38.2 | 51.44 | 23.94 | 23.64 |