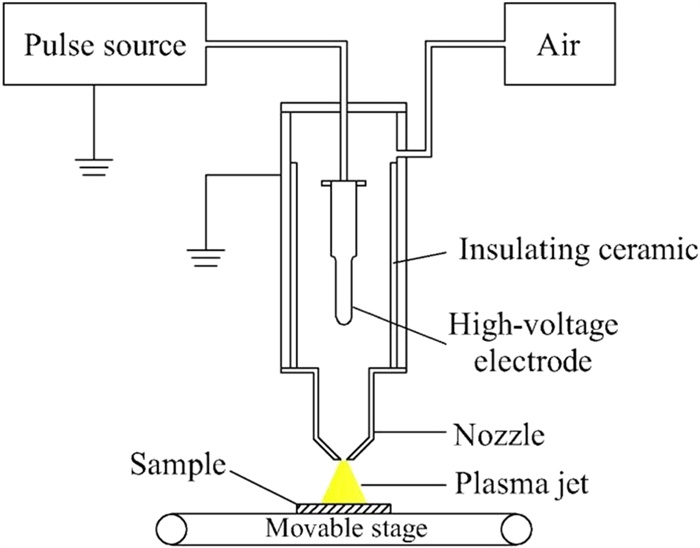
Citation: | Zhijun WANG, Zhongwen CHEN, Hao KANG, Zongbiao YE. Investigation of paint removal by atmospheric pressure plasma jet[J]. Plasma Science and Technology, 2023, 25(8): 085506. DOI: 10.1088/2058-6272/acb38e |
Acrylic polyurethane paint on the surface of 2A12 Al alloy was cleaned utilizing an atmospheric pressure plasma jet in this work. The dynamic evolution of the paint removal process during plasma treatment with time was explored through analysis of morphology and chemical states. The results showed that although the thickness of paint could be reduced effectively with an increase in cleaning time, the removal rate of paint gradually decreased with time. During the initial cleaning process range, its original smooth morphology of paint turned rugged quickly and was almost unchanged with further plasma treatment. Element and chemical state analysis showed that the content of C in the paint layer decreased obviously after plasma treatment. In contrast, the O content increased remarkably. The cleaning mechanism could be mainly attributed to the reaction between active O-containing species in air plasma and organic components in the paint. After removal of superficial organic matter, residue inorganic metal oxide substances aggregated on the base. The exposed metal oxides on the one hand elevated the superficial O content, but on the other hand hindered further plasma penetration, resulting in a gradual decrease in cleaning rate with cleaning time. Therefore, physical wiping was proposed to be incorporated with the plasma method and effective removal of paint was realized.
In the aviation field, aircraft are inevitably affected by external body collision and airflow scouring during flight, resulting in different forms of damage such as cracking, aging, and peeling of the paint layer [1]. Thus, it is necessary to clean the damaged paint layer to facilitate the detection of possible formed defects like corrosion or cracks on the Al alloy substrate [2] and ensure that the new paint layer has enough adhesion during repainting to prevent cracking from the Al alloy matrix. Generally, civilian aircraft need 2‒5 repetitions of overall paint removal and repainting within the service cycle, and military aircraft need paint removal and repainting of the damaged paint after a few hours of flight [3, 4]. Therefore, it is very important to choose an appropriate cleaning technology that can quickly remove the paint without affecting the performance of the substrate.
Traditional methods of paint removal include mechanical cleaning like sandblasting (shot), high-pressure water jets, grinding [5–7] and chemical cleaning like pickling and alkali washing [8, 9]. The main drawbacks of these technologies are the liquid and gas wastes, which cause environmental pollution, increase cleaning cost and bring about a certain risk of deformation due to the stresses of mechanical cleaning or being corroded by chemical substances. Recently, several improved methods such as ultrasonic cleaning [10], laser cleaning [2] and atmospheric pressure plasma cleaning have been proposed. However, each method also has a particular deficiency. The efficiency of ultrasonic cleaning is low and large-scale cleaning is difficult to realize within the consideration of the workpiece size. Laser cleaning is the most widely used cleaning technology for paint removal at present, benefiting from its high energy density and accompanying high cleaning efficiency. However, its power characteristics under undamaged premise are not easy to regulate to balance the removal efficiency and integrity of the base component. An overloaded laser can easily peel off paint and also the anodic oxide film covering the Al alloy surface.
As a new technology for paint removal, non-contact atmospheric pressure plasma cleaning can remove paint with no production of liquid or gas waste and no damage to the substrate [11] in nature. The substrate can also be modified to increase cohesiveness and wettability [12] during cleaning, which is conducive to secondary painting. Comparing to low pressure, atmospheric pressure plasma cleaning does not require the use of a vacuum system, thus reducing equipment costs and freeing space constraints in favor of large-scale treatment [13, 14]. Recently, Ali et al studied the fatigue crack growth of 7075-T6 and 2024-T3 Al substrates after paint removal by atmospheric pressure plasma. Their results showed that paint removal by atmospheric pressure plasma has no substantial effect on fatigue crack growth of Al substrates [11] with no adverse effect on fatigue cracks in the substrate, and without changing its tempering and mechanical properties [15]. Nakamura et al irradiated nitrocellulose paint with atmospheric pressure plasma and showed that plasma-induced thermal stress and pulse discharge current could remove a paint layer effectively [16]. At present, research on atmospheric pressure plasma cleaning of paint is primarily focused on engineering applications, including parameter adjustment of the paint removal process and the substrate performance after paint removal. However, a relevant mechanism of the paint removal process is not deeply discussed.
In this work, a cleaning mechanism of atmospheric pressure plasma to remove paint from the surface of 2A12 Al alloy was explored systematically. The physical and chemical property changes of the paint surface with time during the cleaning process were studied. The sample surface temperature during the cleaning process was monitored, and the sample mass, chemical states, superficial and cross-sectional morphology after plasma treatment were analyzed. Moreover, an improved cleaning method was proposed for rapid and efficient removal of paint.
2A12 Al alloy, the most commonly used skin material of aircraft, is selected as the substrate. A layer of porous Al2O3 is deposited on the surface of the Al alloy through anodic oxidation treatment, which is conducive to improving corrosion resistance, wear resistance and adhesion of paint. TB06-9 Zn yellow acrylic polyurethane primer (Tianjin Lighthouse Coating Co. Ltd), two-component paint composed of acrylic resin and isocyanate resin, is utilized on the surface of the 2A12 Al alloy with a thickness of about 30 μm via a helicopter sealant brushing process and paint spraying process. In order to facilitate the subsequent experiment and measurement, the sample is cut into small pieces with sizes of 15 mm × 15 mm × 1 mm.
A schematic of the experimental device is shown in figure 1. A PS2000 high-voltage pulse power supply is used for plasma generation, with a fixed working voltage of 2 kV, frequency of 54 kHz and power of 800 W. The PB3 plasma generator consists of a high-voltage electrode, ground electrode, insulated ceramic tube and nozzle. Compressed air is used as the working medium with a flow rate of 35‒80 l min-1 and inlet pressure of 0.5‒0.8 MPa. In this configuration, the high-voltage electrode connected to the power supply works as the cathode, and the A450 nozzle for generation of a high-frequency electromagnetic field is employed as the anode for grounding. When the compressed air flows through the electric field, a plasma jet is generated through the ionization of molecules by electric power. The distance between the outlet of the nozzle and sample surface is adjusted as 5‒30 mm, with a corresponding beam spot size of 10‒25 mm in diameter. The ZD-331 triaxial motion platform enables movement of the plasma generator and the sample for scanning and cleaning. During the plasma treatment, the purple region (as shown in figure 2) needs to be avoided to contact samples, as the plasma in that region is unstable and the macroscopic electric arcs are liable to bombard and damage the surface of the paint. This purple-region plasma can only be considered in the initial cleaning stage and is not discussed in this paper.
In this experiment, the dynamic changes in the physical and chemical properties of the paint surface at different times during the cleaning process are studied to clarify the mechanism of paint removal by atmospheric pressure plasma cleaning. In order to minimize the influence of other factors on the results, fixed-point cleaning is used in the experiment. The experimental conditions are as follows: the distance between sample surface and the outlet of the nozzle is set as 10 mm, the inlet pressure is 0.5 MPa and the air flow rate is 50 l min-1. Six samples are cleaned continuously for 5, 10, 30, 60, 180 and 360 s, respectively, to study the time-varying paint properties. Images of the plasma jet in the no-load test and during sample cleaning are shown in figures 2(a) and (b) respectively. The samples are insulated to ground floatingly.
The mass changes of the samples before and after cleaning were analyzed by electronic balance (with a precision of 0.0001 g). Scanning electron microscopy (SEM) was used to observe the changes in the surface and cross-section micro morphology of the samples before and after plasma treatment and the thickness changes of the paint layer after different cleaning times. The fracture surface was obtained by a wire cutting machine and was polished before the test. The surface roughness of the sample after different times of cleaning was measured by a 3D profilometer. The changes in the surface chemical elements and corresponding contents before and after cleaning were analyzed by x-ray photoelectron spectroscopy (XPS) and x-ray energy spectrometry (EDS). The temperature change of the sample surface during cleaning was monitored by an infrared thermal imager (a655sc) to analyze the influence of the surface thermal effect.
Electrons, ions, excited atoms, molecules and free radicals are the main reactive species in plasma [17]. Correspondingly, the types of ions, molecules and neutral particles in plasma are revealed differently depending on the gas medium used. Before the cleaning experiment, the emission spectrum of the air plasma was collected by an optical emission spectrometer (AvaSpec-ULS2048) to study the main components contained in the plasma; a corresponding qualitative spectrum could be helpful in roughly estimating the incident plasma properties for the purpose of understanding its cleaning mechanism.
During the measurement, the optical fiber probe was placed horizontally 50 mm away from the jet in case of direct interaction between the probe and plasma, and the plasma spectrum in the wavelength range of 320‒870 nm was collected at a position 5 mm away from the outlet of the nozzle in the axial direction (located in the purple region; no signal can be detected in the orange region as shown in figure 2). Dry air with an inlet pressure of 0.5 MPa and flow rate of 50 l min-1 was introduced to generate the plasma jet. The exposure time was set to 80 ms; the corresponding spectrum is shown in figure 3.
It can be seen from the spectrum that the first negative band system (N+2B2∑+u→X2∑+g) and the second positive band system (C3Πu→B3Πg) of N2 make the main contributions to the wavelength range of 320‒450 nm [18]. The spectral line at 656.30 nm can be attributed to H I atoms [19]. The spectral lines of O I and N I atoms are mainly located in the range of 740‒870 nm [20].
The weights of the paint samples were monitored throughout the treatment of atmospheric pressure plasma to obtain the mass change caused by plasma cleaning. The mass analysis results are shown in figure 4. It is obvious from figure 4 that the mass change keeps increasing as the plasma-treating time increases. Moreover, the uptrend of mass change is sharp in the first 10 s range. Then it tends to be gradually smooth and saturated in the following 360 s, indicating that the removal efficiency of paint by plasma decreases with cleaning time.
Part of the energy in the plasma system was transferred to the treated sample and brought about the increase in temperature, although most of it was used to maintain the discharge [12]. Hence, an infrared thermal imager was used to monitor the temperature change during cleaning. The obtained time-varying temperature on the sample surface is shown in figure 5. Similar to the varying trend of mass change, the temperature of the tested sample also shows a quick increase and then saturation in a period of 360 s. The maximum temperature of the sample surface reaches more than 300 °C at 10 s. Then the temperature rises slowly and tends to be stable at 390 °C, which is far below the melting point of the Al alloy of the substrate, i.e. 502 °C. In addition, due to the heat insulation of the paint and the Al2O3 film, the temperature generated under the experimental conditions was even lower in comparison to the detected value. The substrate would not be damaged below its melting point [21, 22], and its performance would not be influenced by the thermal effect from atmospheric pressure plasma [23].
The optical images of the sample surface after the treatment of atmospheric pressure plasma are shown in figure 6. It can be seen that the paint on the sample surface could not be completely removed after plasma cleaning. Correspondingly, the color of the surface gradually turned from yellow to yellowish gray, and there was no obvious color change with continuing cleaning till 360 s. The surface profile and roughness of the sample at the center of the cleaned area were tested by a 3D profilometer as shown in figures 7 and 8.
The surface roughness Sa (arithmetic mean height) and Sq (root mean height) of the untreated sample were obtained as 0.481 μm and 0.616 μm, respectively. Both Sa and Sq quickly enlarged until 10 s with respective roughnesses of 0.822 μm and 1.058 μm, then reached saturation and fluctuated only in a small range with increasing cleaning time as shown in figure 8. This is consistent with the mass and color change law, indicating that paint removal mainly happened in the first 10 s and the residue paint could not be cleaned effectively (or the cleaning rate was reduced) for the remaining time although the plasma was sustained.
The surface morphology of the plasma cleaned samples was observed by SEM as shown in figure 9. It can be seen that the surface of the original sample is relatively flat and dense. After plasma treatment, the surface morphology is significantly different from the primary state. The cleaned substrate is composed of spherical, rod-like and lamellar irremovable inactive particles with different sizes ranging from nanometer to micrometer scale. The results show that the surface of the paint layer is destroyed by plasma. The paint layer on the surfaces of all samples is not completely removed under the experimental conditions used. Particles with different sizes and shapes are left on the surface, thus resulting in the increase of surface roughness. However, the surface morphology for all cleaned samples shows no obvious difference and the size of the particles does not change significantly, which is consistent with the roughness results as shown in figure 8.
In order to further characterize the cleaning effect of atmospheric air plasma on paint, the cleaned samples were cut from the central cleaning area using a wire cutting machine to avoid bending of the Al based substrate. The related cross section is shown in figure 10 through SEM observation. The cross section was polished before testing. It can be seen that there is an obvious interface between the paint layer and the Al alloy substrate for the initial sample (red line). The paint layer is relatively dense with a thickness of ~35 μm as shown figure 10(a). After plasma cleaning, newly emerging delamination appeared in the paint layer (yellow line). The superficial layer (blue line) seems loose in comparison to the bottom layer. Moreover, it can be found that the depth of the total paint layer and interface layer gradually decreased. After 360 s of atmospheric pressure plasma cleaning, the remaining paint layer is only about 5 μm in thickness. This reveals that by increasing the cleaning time, the paint layer can be effectively removed. In addition, physical sputtering and airflow by the plasma jet can also remove the loose structure, leading to the reduction of superficial inorganic metal oxide particles.
In order to understand the inherent mechanism of the cleaning process, XPS and EDS were used to analyze the chemical composition of the sample surface. The results of XPS are shown in figure 11 with the corresponding composition of elements listed in table 1. The quantitative results of element composition by EDS are shown in table 2. It can be seen from figure 11 that the elements on the initial sample surface are mainly comprised of C and O. After plasma cleaning, the content of content on the sample surface is significantly reduced. At the same time, peaks of Ti, Ba, Mg, Si, Pb and other elements appear. These elements come from the inorganic components in the paint. Combined with the morphology of paint as shown in figure 10, these elements could be attributed to those unsmooth inorganic particles in a loose structure.
Element | Untreated | 5 s | 10 s | 30 s | 60 s | 180 s | 360 s |
C | 68.41 | 7.24 | 6.60 | 7.15 | 7.94 | 8.74 | 8.03 |
O | 24.78 | 65.54 | 63.71 | 62.76 | 62.79 | 62.85 | 62.29 |
Ti | — | 2.1 | 1.87 | 1.91 | 2.12 | 2.17 | 1.93 |
Ba | 0.05 | 1.71 | 1.61 | 1.62 | 1.72 | 1.41 | 1.47 |
Mg | 0.34 | 6.69 | 8.89 | 8.6 | 7.95 | 7.77 | 7.06 |
Si | 1.23 | 7.49 | 8.17 | 8.66 | 6.98 | 7.01 | 1.52 |
Others | 5.19 | 9.23 | 9.15 | 9.3 | 10.5 | 10.05 | 17.7 |
Element | Untreated | 5 s | 10 s | 30 s | 60 s | 180 s | 360 s |
C | 64.64 | 11.53 | 7.06 | 9.72 | 8.88 | 8.36 | 8.33 |
O | 19.92 | 56.93 | 59.61 | 60.15 | 59.52 | 56.1 | 60.38 |
Ti | 6.21 | 13.34 | 15.45 | 12.33 | 14.33 | 15.79 | 14.4 |
Ba | 1.89 | 3.89 | 4.42 | 3.39 | 3.64 | 4.28 | 3.96 |
Mg | 2.63 | 5.6 | 4.67 | 5.74 | 4.93 | 5.68 | 4.97 |
Si | 2.35 | 3.81 | 3.33 | 4.23 | 3.87 | 4.56 | 2.78 |
Others | 2.36 | 4.9 | 5.46 | 4.44 | 4.83 | 5.23 | 5.18 |
Since the detection depth of XPS is several nanometers on the surface, while that of EDS can reach several micrometers, the combination of XPS and EDS analysis can characterize the changes in surface element content from nanometer to micrometer depth caused by plasma cleaning. By comparison of tables 1 and 2, the element content change can mainly be located in the increase in O and decrease in C, suggesting that the C-containing organic components such as resin in paint were effectively removed through their interactions with N or O reactive species in the formation of gaseous products (H2O, CO2, etc) [15, 24]. The increased O could be assigned to the injected O atoms [25] and their solidification with bare metal elements, like Ti, Ba and Mg. Since these inorganic substances cannot be removed by chemical reaction with reactive species, it also induces an increase in metal content in turn. As the electrode of the plasma gun is mainly made of Cu, these metal elements could be attributed to the component of the paint substrate but not from electrode sputtering. The residual inorganic substances on the sample surface may gradually accumulate and hinder the further permeation of plasma particles, which explains the gradually attenuated cleaning efficiency with treating time.
Moreover, the high-resolution (step size 0.1 eV) XPS spectrum of C 1s was obtained as shown in figure 12. It is known that acrylic resin and isocyanate resin are the main organic components in the paint, and hence C–C/C–H, C–O and COOH/N=C=O bonds are mainly detected in the paint with binding energies of 284.7 eV, 286 eV and 289.5 eV, respectively [25, 26]. After atmospheric pressure plasma cleaning, the C content decreases significantly, consistent with the above analysis. However, a new functional group C=O with a binding energy of 287.5 eV appears in the C 1s peak, and the proportions of C–O and COOH/N=C=O bonds increase as shown in table 3. The reason for the change of chemical bonds during cleaning might be ascribed to the reaction between reactive O species and broken C–C/C–H bonds [25, 27] in the C chains of resin.
C 1s bonds | Untreated | 5 s | 10 s | 30 s | 60 s | 180 s | 360 s |
C–C/C–H | 71 | 49.72 | 39.34 | 42.3 | 41.16 | 38.84 | 40.39 |
C–O | 23.47 | 29.16 | 41.14 | 38.85 | 36.67 | 39.57 | 39.98 |
C=O | — | 11.01 | 11.58 | 11.44 | 11.53 | 11.05 | 11.44 |
COOH/NCO | 5.53 | 10.11 | 7.95 | 7.4 | 10.64 | 10.54 | 8.19 |
It is reported that appropriately high temperature can promote the fracture and decomposition of chemical bonds in organic paint components [16], leading to gradual adhesion reduction and eventual removal of the paint from the substrate. In this study, the stable temperature of the sample surface is monitored and reaches ~400 °C during a cleaning time of 360 s, as shown in figure 5. In order to figure out whether the temperature could lead to break of chemical bonds and paint removal, the effect of temperature in cleaning was studied. In the experiment, the sample was heated at 400 °C in a thermostatic furnace for 360 s. The images of the sample after the heating treatment are shown in figure 13(c). It can be seen that the paint layer on the surface of the samples after the heating treatment did not show significant changes compared with the original samples, nor did the color fade. Combined with the surface morphology as shown in figure 14, it can be found that the sample surface after heating at the constant temperature was basically the same as the original sample. It shows a dense surface and no paint peeling or granulation is found, indicating that the active species in plasma is the main reason for the roughening of the paint surface rather than the temperature effect.
In addition, the chemical composition of the furnace-heated sample was also analyzed by XPS and EDS as shown in figure 15. Quantitative element results are shown in tables 4 and 5, respectively. It can be seen from figure 15 that the XPS spectral lines on the surface of the sample after the thermostatic furnace treatment are basically the same as those on the original sample, and there is no change in the wave peaks and content of Ti, Ba, Pb and other elements, indicating that decomposition of organic components is very limited under ~400 °C. Under the same conditions of temperature and time, the C content of the plasma-cleaned sample decreases significantly, manifesting that the removal of paint is dominated by the interaction between the reactive species in plasma and the organic components.
Element | Untreated | Plasma-cleaned | Furnace-heated |
C | 68.41 | 8.03 | 74.34 |
O | 24.78 | 62.29 | 18.29 |
N | 2.67 | 1.38 | 4.1 |
Ti | — | 1.93 | — |
Ba | 0.05 | 1.47 | — |
Mg | 0.34 | 7.06 | 0.22 |
Si | 1.23 | 1.52 | 2.83 |
Others | 2.52 | 16.32 | 0.22 |
Element | Untreated | Plasma-cleaned | Furnace-heated |
C | 64.64 | 8.33 | 66.75 |
O | 19.92 | 60.38 | 19.72 |
Ti | 6.21 | 14.4 | 6.66 |
Ba | 1.89 | 3.96 | 1.81 |
Mg | 2.63 | 4.97 | 1.47 |
Si | 2.35 | 2.78 | 1.42 |
Others | 2.36 | 5.18 | 2.17 |
According to the above analysis, the process of paint removal by atmospheric pressure air plasma can be understood as follows. Electrons, excited ions and atoms are contained in plasma. The chemical bonds (C–C/C–H) in the organic component of the paint are first broken. Then the broken bonds react with the active species (mainly O atoms) and are removed in the form of volatile gases, accounting for the important removal process of paint. At the same time, partial reactive O atoms react with dangling bonds and generate a new form of C=O on the surface, which cannot be further removed by the plasma. In addition, the residue inorganic metal oxide components of the paint cannot react with the active species in the plasma. They can only be removed by limited physical sputtering or airflow blowing. Therefore, metal oxides gradually accumulate on the surface of the substrate and weaken the cleaning effect of the plasma accordingly. The increase in the O/C ratio also reveals that the organic component of paint can be quickly cleaned once plasma is injected and then gradually saturated. Therefore, the atmospheric pressure plasma selectively cleans the organic components in the paint. To improve the removal of paint, physical wiping (without a chemical solvent) is a conceivable cleaning method. Relevant experiments show that physical wiping has a good removal effect on inorganic particles for the loose paint layer after atmospheric pressure plasma treatment. Specific experimental results are shown in figure 16. The incorporation of alternate plasma cleaning and physical wiping could efficiently obliterate the accumulated inorganic metal oxide components after plasma treatment. After short-term multiple operation, the paint can be completely removed.
The above results show that an atmospheric pressure plasma jet could be an effective cleaning method to remove the paint on the surface of the Al alloy. For large-scale application, the cleaning efficiency and uniformity need to be optimized. Therefore, in the future an array of plasma guns with a programmable mobile platform or robot arm could be employed on the basis of application scenarios to enhance its applicability.
In this work, paint removal of TB06-9 Zn yellow acrylic polyurethane primer on 2A12 Al alloy by atmospheric pressure air plasma was investigated. The change in paint removal efficiency with time and the related cleaning mechanism were analyzed through mass, roughness, morphology and chemical state change analysis before and after plasma cleaning. The cleaning rate decreased gradually with increasing cleaning time, consistent with the significant change in surface morphology and roughness. The change in element content during cleaning manifested as a decrease in C content and an increase in O content, indicating that the paint removal mainly depends on the reaction between active species in plasma and organic components in paint. Moreover, a high-temperature test confirmed the dominant cleaning role of plasma rather than the thermal effect. Moreover, the inorganic metal oxide in paint could not react with the plasma and was accumulated on the matrix surface, which weakened further cleaning with the plasma. To completely remove the paint, a combination of short-term plasma cleaning and physical wiping was used alternately to avoid the accumulation of inorganic components. Our results reveal that an atmospheric pressure plasma jet could be an alternative technology for cleaning paint.
This work was supported by National Natural Science Foundation of China (No. U21A20438) and the Foundation of Key Laboratory of Radiation Physics and Technology of the Ministry of Education (No. 2021SCURPT03).
[1] |
Wang Z J 2011 J. Civil Aviat. Flight Univ. China
22 31(in Chinese)
|
[2] |
Li X Y et al 2020 Materials
13 5363 doi: 10.3390/ma13235363
|
[3] |
Zhang S L and Yang W F 2020 Yunnan Chem. Technol.
47 15(in Chinese) doi: 10.2495/SDP-V15-N1-95-106
|
[4] |
Liu P F et al 2020 Mater. Rep.
34 24121(in Chinese)
|
[5] |
Xiong S et al 2021 Sustainability
13 2900 doi: 10.3390/su13052900
|
[6] |
Luan W L Tu S D 2005 China Mech. Eng.
16 1405(in Chinese) doi: 10.1093/annonc/mdi286
|
[7] |
Lu F et al 2013 Fluid Mach.
41 6(in Chinese) doi: 10.3724/SP.J.1096.2013.20935
|
[8] |
Kittisupakorn P and Kaewpradit P 2003 Korean J. Chem. Eng.
20 985 doi: 10.1007/BF02706926
|
[9] |
Daosud W et al 2005 Comput. Chem. Eng.
29 2110 doi: 10.1016/j.compchemeng.2005.06.007
|
[10] |
Bretz N et al 2005 Numerical simulation of ultrasonic waves in cavitating fluids with special consideration of ultrasonic cleaningProc. IEEE Ultrasonics Symp. Rotterdam: IEEE 703
|
[11] |
Merati A et al 2017 J. Miner. Mater. Charact. Eng.
5 161–73
|
[12] |
Mui T S M et al 2016 J. Adhes. Sci. Technol.
30 218 doi: 10.1080/01694243.2015.1099863
|
[13] |
Senokosov E S and Senokosov A E 2005 Metallurgist
49 117 doi: 10.1007/s11015-005-0064-4
|
[14] |
Jin Y et al 2015 IEEE Trans. Plasma Sci.
43 3193 doi: 10.1109/TPS.2015.2459080
|
[15] |
Merati A et al 2017 J. Miner. Mater. Charact. Eng.
5 223
|
[16] |
Nakamura T et al 2019 IEEE Trans. Plasma Sci.
47 1051 doi: 10.1109/TPS.2018.2860624
|
[17] |
Pan H et al 2015 Dent. Mater. J.
34 529 doi: 10.4012/dmj.2015-035
|
[18] |
Laux C O et al 2003 Plasma Sources Sci. Technol.
12 125 doi: 10.1088/0963-0252/12/2/301
|
[19] |
KramidaA2020NIST Atomic Spectra Database (ver. 5.8), [Online]. Available: https://physics.nist.gov/asd [2021, August 31]. National Institute of Standards and Technology, Gaithersburg, MD (https://doi.org/10.18434/T4W30F)
|
[20] |
Ralchenko Y, Kramida A E and Reader J 2012[online] Available: http://physics.nist.gov/asd
|
[21] |
Zhao W Q et al 2020 Materials
13 31 doi: 10.3390/ma13010031
|
[22] |
Li X K et al 2018 Optik
156 841 doi: 10.1016/j.ijleo.2017.11.010
|
[23] |
Yanishevsky M, Merati A and Bombardier Y 2018 J. Miner. Mater. Charact. Eng.
6 15
|
[24] |
Bónová L et al 2015 Appl. Surf. Sci.
331 79 doi: 10.1016/j.apsusc.2015.01.030
|
[25] |
Shao T et al 2017 IEEE Trans. Dielectr. Electr. Insul.
24 1557 doi: 10.1109/TDEI.2017.006321
|
[26] |
Narimisa M et al 2021 Polymer
215 123421 doi: 10.1016/j.polymer.2021.123421
|
[27] |
Coulon J F, Tournerie N and Maillard H 2013 Appl. Surf. Sci.
283 843 doi: 10.1016/j.apsusc.2013.07.028
|
1. | Wang, Z., Mao, X., Lou, Y. et al. Protective film on cerium metal through in-situ formation of a dense CeO2 oxide layer using air plasma. Chemical Engineering Journal, 2025. DOI:10.1016/j.cej.2024.158285 |
2. | Zhao, Y., Yue, X., Zhang, P. et al. Removal mechanism and cleaning method of electroplating masking paint with a microwave plasma jet. Journal of Manufacturing Processes, 2024. DOI:10.1016/j.jmapro.2024.07.020 |
1. | Wang, Z., Mao, X., Lou, Y. et al. Protective film on cerium metal through in-situ formation of a dense CeO2 oxide layer using air plasma. Chemical Engineering Journal, 2025. DOI:10.1016/j.cej.2024.158285 |
2. | Zhao, Y., Yue, X., Zhang, P. et al. Removal mechanism and cleaning method of electroplating masking paint with a microwave plasma jet. Journal of Manufacturing Processes, 2024. DOI:10.1016/j.jmapro.2024.07.020 |
Element | Untreated | 5 s | 10 s | 30 s | 60 s | 180 s | 360 s |
C | 68.41 | 7.24 | 6.60 | 7.15 | 7.94 | 8.74 | 8.03 |
O | 24.78 | 65.54 | 63.71 | 62.76 | 62.79 | 62.85 | 62.29 |
Ti | — | 2.1 | 1.87 | 1.91 | 2.12 | 2.17 | 1.93 |
Ba | 0.05 | 1.71 | 1.61 | 1.62 | 1.72 | 1.41 | 1.47 |
Mg | 0.34 | 6.69 | 8.89 | 8.6 | 7.95 | 7.77 | 7.06 |
Si | 1.23 | 7.49 | 8.17 | 8.66 | 6.98 | 7.01 | 1.52 |
Others | 5.19 | 9.23 | 9.15 | 9.3 | 10.5 | 10.05 | 17.7 |
Element | Untreated | 5 s | 10 s | 30 s | 60 s | 180 s | 360 s |
C | 64.64 | 11.53 | 7.06 | 9.72 | 8.88 | 8.36 | 8.33 |
O | 19.92 | 56.93 | 59.61 | 60.15 | 59.52 | 56.1 | 60.38 |
Ti | 6.21 | 13.34 | 15.45 | 12.33 | 14.33 | 15.79 | 14.4 |
Ba | 1.89 | 3.89 | 4.42 | 3.39 | 3.64 | 4.28 | 3.96 |
Mg | 2.63 | 5.6 | 4.67 | 5.74 | 4.93 | 5.68 | 4.97 |
Si | 2.35 | 3.81 | 3.33 | 4.23 | 3.87 | 4.56 | 2.78 |
Others | 2.36 | 4.9 | 5.46 | 4.44 | 4.83 | 5.23 | 5.18 |
C 1s bonds | Untreated | 5 s | 10 s | 30 s | 60 s | 180 s | 360 s |
C–C/C–H | 71 | 49.72 | 39.34 | 42.3 | 41.16 | 38.84 | 40.39 |
C–O | 23.47 | 29.16 | 41.14 | 38.85 | 36.67 | 39.57 | 39.98 |
C=O | — | 11.01 | 11.58 | 11.44 | 11.53 | 11.05 | 11.44 |
COOH/NCO | 5.53 | 10.11 | 7.95 | 7.4 | 10.64 | 10.54 | 8.19 |
Element | Untreated | Plasma-cleaned | Furnace-heated |
C | 68.41 | 8.03 | 74.34 |
O | 24.78 | 62.29 | 18.29 |
N | 2.67 | 1.38 | 4.1 |
Ti | — | 1.93 | — |
Ba | 0.05 | 1.47 | — |
Mg | 0.34 | 7.06 | 0.22 |
Si | 1.23 | 1.52 | 2.83 |
Others | 2.52 | 16.32 | 0.22 |
Element | Untreated | Plasma-cleaned | Furnace-heated |
C | 64.64 | 8.33 | 66.75 |
O | 19.92 | 60.38 | 19.72 |
Ti | 6.21 | 14.4 | 6.66 |
Ba | 1.89 | 3.96 | 1.81 |
Mg | 2.63 | 4.97 | 1.47 |
Si | 2.35 | 2.78 | 1.42 |
Others | 2.36 | 5.18 | 2.17 |