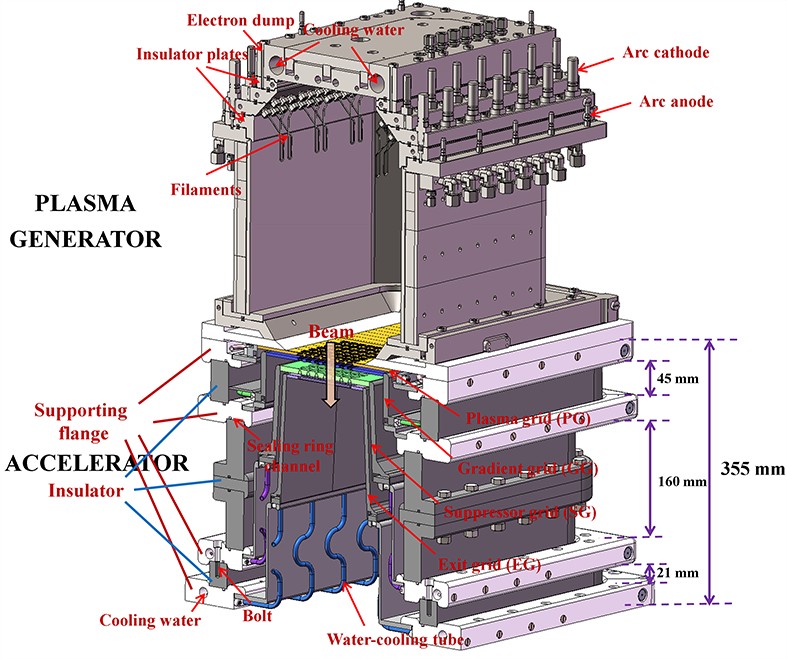
Citation: | Ruihai TONG, Yu ZHOU, Wulyu ZHONG, Jie WEN, Zhongbing SHI, Xiaolan ZOU, Anshu LIANG, Zengchen YANG, Min JIANG, Xin YU, Yuqi SHEN. A new Q-band comb-based multi-channel microwave Doppler backward scattering diagnostic developed on the HL-3 tokamak[J]. Plasma Science and Technology, 2025, 27(1): 015102. DOI: 10.1088/2058-6272/ad8c86 |
The Doppler backscattering (DBS) diagnostic is widely used to measure the localized density fluctuations and the propagation velocity of turbulent structures. Microwave is launched at a frequency that approaches a cutoff layer in the plasma at an angle oblique to the cutoff layer. A new Q-band multichannel DBS system based on a comb generator has been designed and tested for application on the HL-3 tokamak. With the comb generator and heterodyne scheme, the stability and flexibility of the new DBS system are improved. The new DBS diagnostic has a high output power (~ 10 dBm), good power flatness (< 5 dB in Q-band), and frequency stability, and the inter-frequency separation is tunable remotely. This article introduces the system design, laboratory test results, and initial experimental results from the HL-3 tokamak. With the help of the newly developed multichannel DBS, the turbulence information can be studied with high temporal and spatial resolution.
Neutral beam injection is a main auxiliary heating method with the clearest physical mechanism and the highest heating efficiency. It has been widely used in tokamak and other types of magnetic confinement fusion devices. The Experimental Advanced Superconducting Tokamak (EAST) is equipped with two beam lines, each equipped with two sets of 80 keV/50 A hot cathode bucket positive ion sources [1–3]. The designed injection power is 4 MW per beamline, and the total injection power can reach 8 MW [4, 5]. In order to support the physical research on the EAST, a new positive ion source with designed beam energy of 120 keV was proposed to be developed. Accelerator structure is one of the key components of the ion source. When the ion source is upgraded to 120 keV, the voltage applied between different grids is greatly increased. It is necessary to redesign a reasonable insulation support system to ensure the stability of the accelerator. The accelerator insulator must be made of materials with good sealing performance, high strength and good insulation performance. In 1981, Paterson et al designed the insulator structure of positive ion source accelerator of TFTR device, and gave the manufacturing process of Al2O3 ceramic titanium brazing rectangular insulator structure [6]. In 2008, Yamano et al analyzed and compared the vacuum discharge characteristics of fiber reinforced polymer (FRP) and Al2O3 ceramic insulator samples in JT-60U accelerator, and found that the flashover voltage of FRP samples was lower than that of Al2O3 ceramic samples [7]. In 2001, the Korean Atomic Energy Research Institute designed a round-hole type accelerator for the KSTAR neutral beam injection device at 120 keV, and determined the PEEK material insulator and its parameters [8]. Based on the above research, at present, in the engineering application of ion source, the relatively mature insulating materials that can meet the requirements of all aspects include FRP fiber-reinforced epoxy resin, PEEK and Al2O3 ceramics.
In addition, scholars have carried out various studies on the insulation support system of ion sources in major fusion devices. In 2008, Ikeda et al measured the breakdown voltage of FRP insulator with and without grids in order to test the voltage holding capability of the 500 kV, 22 A on the three-grids accelerator in JT-60U [9]. In 2010, Tanaka et al tested the breakdown voltage at different gap lengths by changing the grid gap of the JT-60 negative ion source in order to determine the required grid gap length for stable voltage holding [10]. In 2014, Wei et al investigated the connection design of the insulator of the EAST ion source accelerator. Because the bonding technology has the advantages of simple operation and high strength, the flange and insulator were bonded by using epoxy adhesive, and then different samples were tested by tensile test, so as to determine the optimal bonding structure [11]. Based on the above research, scholars mainly focus on the electric field distribution around the grids and insulators of accelerator. In this paper, the design of the insulation support system of the 120 keV accelerator is introduced firstly, and then based on the structural model of the 120 keV positive ion source accelerator, the electrostatic analyses of the insulators and grids are carried out by using the method of finite element analysis. The voltage resistance characteristics of the insulators are analyzed, and the appropriate insulator material and corresponding design parameters are determined.
The 80 keV hot cathode bucket positive ion source operated in EAST is composed of a bucket plasma generator with a multi-magnet pole field and a four-grids slit-type accelerator [4]. The accelerator is mainly composed of flanges, insulators, grid supports and four grids, including plasma grid (PG), gradient grid (GG), suppression grid (SG) and earth grid (EG). The insulation support system is made of three layers of FRP insulators and four layers of 304 stainless steel flanges bonded by epoxy adhesive, which serves to support the whole beam source system and voltage insulation.
A key issue in the development of EAST ion source is the connection between the insulator and the support flange. The insulation support system needs to meet the requirements of high voltage holding, mechanical strength and vacuum sealing. Although the epoxy adhesive bonding technology used in the 80 keV positive ion source accelerator has the advantages of simple operation and low cost, it is very difficult to repair when the insulation support system leaks under long-term operation. At the same time, when the 80 keV positive ion source accelerator is optimized and upgraded, the disassembly device is also a big problem. Therefore, the insulation support system of 120 keV positive ion source accelerator was optimized and upgraded in these aspects. The 120 keV positive ion source uses a four-grids circular hole accelerator. The insulators and flanges of the 120 keV positive ion source accelerator are fixedly connected by M8 PEEK hex socket head cap screws, and sealed by sealing rings, which is more convenient for disassembly and maintenance. In addition, the 120 keV positive ion source accelerator uses PEEK material with better insulation performance than the FRP material used in the insulator of the 80 keV positive ion source accelerator. The 120 keV positive ion source accelerator has a length of 856 mm, a width of 470 mm and a height of 355 mm. The four layers of grids will be applied with voltages of 120 kV, 93.6 kV, −5 kV and 0 kV respectively. The grid plate of the 120 keV positive ion source accelerator is made of molybdenum material, which has higher hardness and melting point than the copper material used in the grid plate of the 80 keV positive ion source accelerator. The specific structural parameters are shown in the figures 1 and 2.
The 80 keV positive ion source has breakdown and leakage issues during operation in the past few years, which may be due to the breakdown of vacuum gap between the accelerating grid and the grid support structure, as well as vacuum leakage near the insulators. In fact, obvious discharge marks were observed in these areas during the disassembly of the accelerator. Therefore, after completing the design phase, it is necessary to evaluate the insulation characteristics of the 120 keV accelerator and select appropriate insulation materials. There are currently three main types of insulation materials, namely FRP fiber-reinforced epoxy resin, PEEK, and Al2O3 ceramics.
Based on the three-dimensional structural model of the 120 keV positive ion source accelerator, the study of the voltage holding performance of insulators with different heights, structures and materials was carried out by electrostatic simulations with COMSOL Multiphysics finite element software [12]. In order to ensure a certain safety margin, the voltage difference between grids was increased by 20% during simulations respectively, and the voltages of four layers of grids and flanges were set to be 144 kV (PG and flange), 112.32 kV (GG and flange), −6 kV (SG and flange), and 0 kV (EG and flange). The design heights of the three insulators were 55.00 mm (PG-GG insulator), 172.70 mm (GG-SG insulator) and 33.88 mm (SG-EG insulator). Under the condition of steady-state vacuum operation, different insulating materials were simulated by changing the relative dielectric constants of materials in the software, and then the changes of the distribution of electric fields around the insulators were observed by changing the height of the insulators.
In order to save computing time, the accelerator was divided into three parts for electrostatic simulations. As shown in figure 3, the region near the insulators of each layer (blue-boxed region) is selected as the study object, in which the electric field distribution is most obviously affected by the two variables of insulator material and height, and then the maximum electric field (red-boxed region) is searched for in this region. As shown in figure 3(a), since the water-cooling tubes on GG flange are located between PG flange and GG flange, a layer of stainless steel cover plate is added on the surface of GG water-cooling tubes for protection. It can be clearly observed that near the PG-GG insulator, the electric field is the largest at the boundary of the GG flange water pipe protection cover plate, and when the height of the PG-GG insulator is 37 mm, which corresponds to a minimum gap of 9.15 mm in this region, the maximum electric field at this location is 7.4 kV/mm. Since the probability of breakdown increases significantly when the minimum gap between flanges is smaller than the grid gap, we started by increasing the height of the insulator corresponding to the minimum gap between flanges and the grid gap, and continued to increase until the design value is reached. We recorded the maximum electric field in the region at different heights. It can be seen from figure 4: (1) with the increasing of the insulator height, the maximum electric field on the surface decreases gradually, and the two are negatively correlated; (2) at the same insulator height, the PEEK material has the smallest maximum electric field and the best insulation performance among the three materials; (3) when the height of the insulator reaches the design value, the maximum electric field on the surface of PG-GG insulator and GG-SG insulator is around 4 kV/mm.
In summary, PEEK material was ultimately chosen as the insulation material. Moreover, large ceramics are difficult to process, with poor dimensional accuracy and high weight. There are also some defects in the finished product such as cracks, porosity, brittle fracture, etc. PEEK material not only has better insulating properties, but also has better machinability and surface than FRP epoxy resin. The design height of the insulator can meet the withstand voltage requirement of 120 keV, at which time the maximum electric field in the insulator region between each flange is reduced to about 4 kV/mm or less than 4 kV/mm [13].
During the four-year operation period from 1991 to 1994, 6% of the NBI system failure rate of the JT-60 device occurred on the ion source structure, which was mainly caused by the leakage of the cooling channels of the accelerator grids, the vacuum leakage of the insulators, and the voltage breakdown between the grids [14]. Therefore, the electric field concentration between grids is also an important factor affecting the insulation performance of accelerator. Through the beam optical analysis, the grid gap values were set to 3 mm (PG-GG), 10.5 mm (GG-SG), 3 mm (SG-EG), and the voltage values of four layers of grids and flanges were set to 120 kV (PG and flange), 93.6 kV (GG and flange), −5 kV (SG and flange), and 0 kV (EG and flange). Due to the small voltage difference between the SG and the EG, the maximum electric field was within the safe range. Therefore, the main simulations were conducted on the electric field distribution between the PG-GG and GG-SG with a large voltage difference under steady-state vacuum operation conditions.
According to the Clump theory under non-uniform electric field, the local electric field E on the grid surface is an important factor affecting the breakdown voltage, as particles accelerate and bombard the opposite grid with energy QV proportional to the product of EV, where Q is the particle charge, E is the local electric field strength and V is the applied voltage [15]. Therefore, optimizing the geometric shape between grids to improve voltage retention capability is one of the solutions to alleviate strong field distribution. From figure 5, it can be seen that the electric field in the acceleration gap between PG and GG is not uniform, but concentrated in a certain position. The electric fields in positions 1 and 3 are too large, with a maximum value of 15.1 kV/mm, which may cause inter-electrode firing and breakdown in long-term operation. So the structural optimization is needed. However, in beam optical analysis, parameters such as grid gap and aperture have already been determined, so the strong field distribution can only be mitigated by changing the chamfer shape. Positions 1 and 3 between PG and GG are both controlled by the same chamfer. The chamfer value is continuously increased in step of 0.1 mm, and the maximum electric field simulation values of positions 1 and 3 are recorded respectively. As shown in table 1, as the chamfer values increase, the maximum electric fields of positions 1 and 3 decrease. However, when the chamfer value increases to 0.8 mm, the maximum electric field of position 1 increases instead, which is due to the superposition of the chamfers of the neighboring circular holes in the PG plate, resulting in a decrease of the PG-GG gap, so that the electric field begins to increase. It is finally determined that the chamfer values of the positions 1 and 3 between PG and GG are designed to be 0.7 mm.
Chamfer (mm) | Position 1 (kV/mm) | Position 3 (kV/mm) |
0.4 | 15.1 | 14.2 |
0.6 | 14.4 | 13.1 |
0.7 | 14.2 | 12.7 |
0.8 | 15.6 | 12.3 |
As shown in figure 6, the voltage difference between the grids of GG-SG is the largest, with the electric fields at positions 1, 3 and 5 being too large, reaching a maximum value of 18.1 kV/mm. Structural optimization is needed for these three regions. Due to the limitation of the hole spacing of the GG plate, the chamfer value cannot be infinitely increased. Therefore, it is necessary to analyze these regions with larger electric fields within a reasonable range. The positions 1 and 3 between GG and SG are controlled by the same chamfer, and the chamfer value is continuously increased in 0.2 mm step to the maximum chamfer value of 1.6 mm with structural limitation, and the chamfer value of position 5 is continuously increased in 1.0 mm step. The maximum electric field simulation value of each point is shown in table 2. With the continuous increase of chamfer values, the maximum electric fields of positions 1, 3 and 5 are constantly decreasing. However, the chamfer value of position 5 cannot be too large, as it may cause the inner cooling water channel wall to be too thin, affecting the transportation of cooling water. The final determination is to design the chamfer values for positions 1 and 3 between GG and SG to be 1.6 mm, and for position 5 to be 5.0 mm.
Chamfer (mm) | Position 1 (kV/mm) | Position 3 (kV/mm) | Chamfer (mm) | Position 5 (kV/mm) |
1.0 | 14.4 | 13.5 | 2.0 | 18.1 |
1.2 | 14.2 | 13.2 | 2.4 | 17.1 |
1.4 | 14.1 | 13.0 | 3.0 | 16.0 |
1.6 | 13.9 | 12.9 | 4.0 | 14.7 |
- | - | - | 5.0 | 13.7 |
- | - | - | 5.5 | 13.5 |
- | - | - | 6.0 | 12.9 |
On the premise of ensuring the maximum beam density and the minimum beam divergence angle in the beam optical analysis [16], and according to the design reference of the 80 keV positive ion source accelerator, the maximum electric fields in the acceleration gaps between grids need to be less than 14 kV/mm. In summary, it is determined that the chamfer values for positions 1 and 3 between PG and GG are designed to be 0.7 mm, the chamfer values for positions 1 and 3 between GG and SG are designed to be 1.6 mm, and the chamfer value for position 5 is designed to be 5.0 mm. Therefore, the maximum electric fields between the four layers of grids are around 14 kV/mm, or less than 14 kV/mm, which can basically meet the 120 keV withstand voltage requirement. The finalized design values of all the chamfer values between the four layers of grids are shown in figure 7 and table 3. Table 3 includes the preliminary chamfer values determined by beam optical analysis and the final values determined by electrostatic simulation.
Position | Preliminary determined value (mm) | Final value (mm) | Position | Preliminary determined value (mm) |
Final value (mm) |
R1 | 0.5 | 0.5 | R7 | 1.0 | 1.6 |
R2 | 0.5 | 0.5 | R8 | 1.5 | 1.5 |
R3 | 0.4 | 0.7 | R9 | 0.5 | 0.5 |
R4 | 1.0 | 1.0 | R10 | 1.0 | 1.0 |
R5 | 0.2 | 0.2 | R11 | 1.0 | 1.0 |
R6 | 1.4 | 1.4 |
In order to support the physical research on the EAST, a new positive ion source with designed beam energy of 120 keV was proposed to be developed. A key issue in the development of the EAST ion source is the connection between insulator and support flange. The 120 keV positive ion source uses a four-grids circular hole accelerator, and PEEK insulators are fixed with 304 stainless steel flanges through bolts and sealed with sealing rings, which plays the role of supporting the entire beam source system and voltage insulation.
The concentration of electric field is an important factor affecting the insulation performance of accelerator. In order to ensure the stability of the beam, a three-dimensional 120 keV positive ion source accelerator model was established, and the withstand voltage performance of insulations and grids was analyzed through electrostatic simulations. The electrostatic simulations of insulators show that: (1) the height of the insulator is negatively correlated with the maximum electric field of its surface in the region; (2) among the three materials, PEEK material has the best insulating property, so PEEK material is selected for insulators of the 120 keV accelerator; (3) when the heights of insulators are the design values, the maximum electric fields on the surface of the PG-GG insulator and GG-SG insulator are about 4 kV/mm, which is able to meet the pressure resistance requirement of 120 keV. In addition, the electric fields in the acceleration gaps between grids are not uniform, so grids need to be optimized in structure. Electrostatic simulations of grids show that: (1) the chamfer values between PG and GG in positions 1 and 3 are designed to be 0.7 mm; (2) the chamfer values for positions 1 and 3 between GG and SG are designed to be 1.6 mm, and the chamfer value for position 5 is designed to be 5.0 mm; (3) after optimizing the structures between grids, the maximum electric fields between the four layers of grids are around 14 kV/mm, or less than 14 kV/mm, which can meet the 120 keV withstand voltage requirement.
This work was supported by National Natural Science Foundation of China (Nos. 12105087, 12275096, and 11922503), the Joint Funds of the National Natural Science Foundation of China (No. U21A20440), and the Science and Technology Planning Project of Sichuan Province (No. 2023YFG0139).
[1] |
Conway G D et al 2004 Plasma Phys. Control. Fusion 46 951 doi: 10.1088/0741-3335/46/6/003
|
[2] |
Hirsch M et al 2001 Plasma Phys. Control. Fusion 43 1641 doi: 10.1088/0741-3335/43/12/302
|
[3] |
Pratt Q et al 2022 Plasma Phys. Control. Fusion 64 095017 doi: 10.1088/1361-6587/ac8614
|
[4] |
Conway G et al 2006 Nucl. Fusion 46 S799 doi: 10.1088/0029-5515/46/9/S15
|
[5] |
Pinzón J R et al 2019 Plasma Phys. Control. Fusion 61 105009 doi: 10.1088/1361-6587/ab394d
|
[6] |
Pinzón J R et al 2019 Nucl. Fusion 59 074002 doi: 10.1088/1741-4326/ab227e
|
[7] |
Yashin A et al 2023 Appl. Sci. 13 3430 doi: 10.3390/app13063430
|
[8] |
Peebles W A et al 2010 Rev. Sci. Instrum. 81 10D902 doi: 10.1063/1.3464266
|
[9] |
Damba J et al 2022 Rev. Sci. Instrum. 93 103549 doi: 10.1063/5.0101864
|
[10] |
Yashin A Y et al 2022 J. Inst. 17 C01023 doi: 10.1088/1748-0221/17/01/C01023
|
[11] |
Hu J Q et al 2017 Rev. Sci. Instrum. 88 073504 doi: 10.1063/1.4991855
|
[12] |
Shi Z et al 2018 Rev. Sci. Instrum. 89 10H104 doi: 10.1063/1.5035260
|
[13] |
Kohagura J et al 2022 Rev. Sci. Instrum. 93 123507 doi: 10.1063/5.0101893
|
[14] |
Happel T et al 2009 Rev. Sci. Instrum. 80 073502 doi: 10.1063/1.3160106
|
[15] |
Tokuzawa T et al 2014 Plasma Fusion Res. 9 1402149 doi: 10.1585/pfr.9.1402149
|
[16] |
Hillesheim J C et al 2015 Nucl. Fusion 55 073024 doi: 10.1088/0029-5515/55/7/073024
|
[17] |
Bulanin V V et al 2021 Rev. Sci. Instrum. 92 033539 doi: 10.1063/5.0030307
|
[18] |
Crocker N A et al 2011 Plasma Phys. Control. Fusion 53 105001 doi: 10.1088/0741-3335/53/10/105001
|
[19] |
Vayakis G et al 2006 Nucl. Fusion 46 S836 doi: 10.1088/0029-5515/46/9/S20
|
[20] |
Shi Z et al 2016 Rev. Sci. Instrum. 87 113501 doi: 10.1063/1.4966680
|
[21] |
Soga R et al 2016 J. Instrum. 11 C02009 doi: 10.1088/1748-0221/11/02/C02009
|
[22] |
Cabrera M et al 2023 Rev. Sci. Instrum. 94 083504 doi: 10.1063/5.0151271
|
[23] |
Happel T et al 2020 Plasma Sci. Technol. 22 064002 doi: 10.1088/2058-6272/ab618c
|
[24] |
Molina Cabrera P et al 2018 Rev. Sci. Instrum. 89 083503 doi: 10.1063/1.5007433
|
[25] |
Tokuzawa T et al 2022 Appl. Sci. 12 4744 doi: 10.3390/app12094744
|
[26] |
Tokuzawa T et al 2018 Rev. Sci. Instrum. 89 10H118 doi: 10.1063/1.5035118
|
[27] |
Wang M Y et al 2018 Rev. Sci. Instrum. 89 093501 doi: 10.1063/1.5033968
|
[28] |
Wu M F et al 2020 J. Instrum. 15 P12009 doi: 10.1088/1748-0221/15/12/P12009
|
[29] |
Xiang H et al 2018 Rev. Sci. Instrum. 89 10H103 doi: 10.1063/1.5035445
|
[30] |
Ren X et al 2021 Rev. Sci. Instrum. 92 033545 doi: 10.1063/5.0040915
|
[31] |
Wen J et al 2021 Rev. Sci. Instrum. 92 063513 doi: 10.1063/5.0043676
|
[32] |
Breitbarth J 2006 “Design and Characterization of Low Phase Noise Microwave Circuits”.
|
[33] |
Duan X et al 2022 Nucl. Fusion 62 042020 doi: 10.1088/1741-4326/ac3be6
|
[34] |
Zhong W et al 2024 Innovation 5 100555 doi: 10.1016/j.xinn.2023.100555
|
[35] |
Xue L et al 2019 Nucl. Fusion 60 016016 doi: 10.1088/1741-4326/ab4c65
|
[36] |
Marki Microwave. “https://markimicrowave.com” 2024.
|
[37] |
Zhou Y et al 2023 Rev. Sci. Instrum 94 013508 doi: 10.1063/5.0126970
|
[38] |
Seol J et al 2013 Phys. Plasmas 20 042504 doi: 10.1063/1.4795731
|
[39] |
Rouphael T J 2014 Wireless Receiver Architectures and Design: Antennas, RF, synthesizers, mixed signal, and digital signal processing: Academic Press, 2014
|
[40] |
Tektronix. “https://www.tek.com/en” 2024.
|
[41] |
Zhong X et al 2023 Plasma Sci. Technol 25 095104 doi: 10.1088/2058-6272/acc8ba
|
[42] |
Wang G et al 2024 Nucl. Fusion 64 066024 doi: 10.1088/1741-4326/ad4046
|
[43] |
Mou J et al 2024 Plasma Sci. Technol. 26 034013 doi: 10.1088/2058-6272/ad127a
|
[44] |
Gong S et al 2023 Plasma Sci. Technol. 25 075601 doi: 10.1088/2058-6272/acbd8d
|
[1] | A. PONOMARENKO, A. YASHIN, V. GUSEV, E. KISELEV, G. KURSKIEV, V. MINAEV, Y. PETROV, N. SAKHAROV, P. SHCHEGOLEV, E. TKACHENKO, N. ZHILTSOV. First results of turbulence investigation on Globus-M2 using radial correlation Doppler reflectometry[J]. Plasma Science and Technology, 2024, 26(10): 105101. DOI: 10.1088/2058-6272/ad5fe5 |
[2] | Weiwei FAN (范伟伟), Bowen ZHENG (郑博文), Jing CAO (曹靖), Shibiao TANG (唐世彪), Qingwei YANG (杨青蔚), Zejie YIN (阴泽杰). Development of a fast electron bremsstrahlung diagnostic system based on LYSO and silicon photomultipliers during lower hybrid current drive for tokamak[J]. Plasma Science and Technology, 2019, 21(6): 65104-065104. DOI: 10.1088/2058-6272/ab0a77 |
[3] | Zhongbing SHI (石中兵), Wulyu ZHONG (钟武律), Min JIANG (蒋敏). Progress of microwave diagnostics development on the HL-2A tokamak[J]. Plasma Science and Technology, 2018, 20(9): 94007-094007. DOI: 10.1088/2058-6272/aad27b |
[4] | Lei YE (叶磊), Xiaotao XIAO (肖小涛), Yingfeng XU (徐颖峰), Zongliang DAI (戴宗良), Shaojie WANG (王少杰). Implementation of field-aligned coordinates in a semi-Lagrangian gyrokinetic code for tokamak turbulence simulation[J]. Plasma Science and Technology, 2018, 20(7): 74008-074008. DOI: 10.1088/2058-6272/aac013 |
[5] | Lu WANG (王璐), Shuitao PENG (彭水涛), P H DIAMOND. Gyrokinetic theory of turbulent acceleration and momentum conservation in tokamak plasmas[J]. Plasma Science and Technology, 2018, 20(7): 74004-074004. DOI: 10.1088/2058-6272/aab5bc |
[6] | H R MIRZAEI, R AMROLLAHI. Design, simulation and construction of the Taban tokamak[J]. Plasma Science and Technology, 2018, 20(4): 45103-045103. DOI: 10.1088/2058-6272/aaa669 |
[7] | ZHU Yilun (朱逸伦), ZHAO Zhenling (赵朕领), TONG Li (仝丽), CHEN Dongxu (陈东旭), XIE Jinlin (谢锦林), LIU Wandong (刘万东). Optics System Design of Microwave Imaging Reflectometry for the EAST Tokamak[J]. Plasma Science and Technology, 2016, 18(4): 449-452. DOI: 10.1088/1009-0630/18/4/20 |
[8] | LI Gongshun (李恭顺), YANG Yao (杨曜), LIU Haiqing (刘海庆), JIE Yinxian (揭银先), ZOU Zhiyong (邹志勇), WANG Zhengxing (王正兴), ZENG Long (曾龙), WEI Xuechao (魏学朝), LI Weiming (李维明), LAN Ting (兰婷), ZHU Xiang (朱翔), LIU Yukai (刘煜锴), GAO Xiang (高翔). Bench Test of the Vibration Compensation Interferometer for EAST Tokamak[J]. Plasma Science and Technology, 2016, 18(2): 206-210. DOI: 10.1088/1009-0630/18/2/19 |
[9] | GAO Xiang (高翔), ZHANG Tao (张涛), HAN Xiang (韩翔), ZHANG Shoubiao (张寿彪), et al.. Observation of Pedestal Plasma Turbulence on EAST Tokamak[J]. Plasma Science and Technology, 2013, 15(8): 732-737. DOI: 10.1088/1009-0630/15/8/03 |
[10] | Naohiro KASUYA, Seiya NISHIMURA, Masatoshi YAGI, Kimitaka ITOH, Sanae-I ITOH. Heavy Ion Beam Probe Measurement in Turbulence Diagnostic Simulator[J]. Plasma Science and Technology, 2011, 13(3): 326-331. |
Chamfer (mm) | Position 1 (kV/mm) | Position 3 (kV/mm) |
0.4 | 15.1 | 14.2 |
0.6 | 14.4 | 13.1 |
0.7 | 14.2 | 12.7 |
0.8 | 15.6 | 12.3 |
Chamfer (mm) | Position 1 (kV/mm) | Position 3 (kV/mm) | Chamfer (mm) | Position 5 (kV/mm) |
1.0 | 14.4 | 13.5 | 2.0 | 18.1 |
1.2 | 14.2 | 13.2 | 2.4 | 17.1 |
1.4 | 14.1 | 13.0 | 3.0 | 16.0 |
1.6 | 13.9 | 12.9 | 4.0 | 14.7 |
- | - | - | 5.0 | 13.7 |
- | - | - | 5.5 | 13.5 |
- | - | - | 6.0 | 12.9 |
Position | Preliminary determined value (mm) | Final value (mm) | Position | Preliminary determined value (mm) |
Final value (mm) |
R1 | 0.5 | 0.5 | R7 | 1.0 | 1.6 |
R2 | 0.5 | 0.5 | R8 | 1.5 | 1.5 |
R3 | 0.4 | 0.7 | R9 | 0.5 | 0.5 |
R4 | 1.0 | 1.0 | R10 | 1.0 | 1.0 |
R5 | 0.2 | 0.2 | R11 | 1.0 | 1.0 |
R6 | 1.4 | 1.4 |