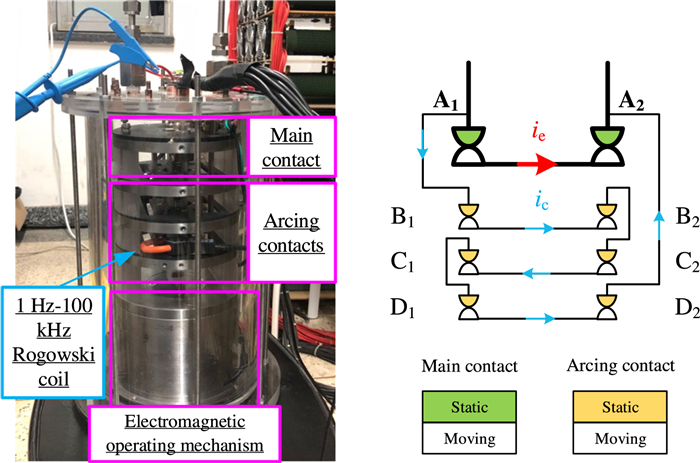
Citation: | Bowen JIA, Jianwen WU, Shu LI, Hao WU, Xiangjun PENG, Jian DAI, Ruang CHEN. Magneto-hydrodynamic simulation study of direct current multi-contact circuit breaker for equalizing breaking arc[J]. Plasma Science and Technology, 2023, 25(2): 025506. DOI: 10.1088/2058-6272/ac910f |
This work is based on a direct current (DC) natural current commutation topology, which uses load-carrying branch contacts carrying rated current and multiple sets of series arcing branch contacts in parallel to achieve circuit breaking. The proposed topology can meet the new requirements of higher voltage DC switches in aviation, aerospace, energy and other fields. First, a magneto-hydrodynamic arc model is built using COMSOL Multiphysics, and the different arc breaking characteristics of the arcing branch contacts in different gas environments are simulated. Then, a voltage uniformity coefficient is used to measure the voltage sharing effect in the process of dynamic interruption. In order to solve the dispersion of arcing contact action, a structural control method is adopted to improve the voltage uniformity coefficient. The uniform voltage distribution can improve the breaking capacity and electrical life of the series connection structure.
Direct current (DC) power supply systems have been widely used in the aerospace, urban rail traction, ship power system and new energy industries due to their outstanding advantages such as good system stability, good load characteristics and simple control [1–3]. However, the further development of medium and low voltage DC power supply systems to a higher voltage level needs a breakthrough in DC breaking technology and the development of environment-resistant and lightweight DC switchgear. In recent years, high voltage DC power supply systems with a rated voltage of 270 V have been used in modern multi-electric and all-electric aircraft. Similarly, in the field of aerospace, solar power stations have been demonstrated to provide the largest power supply for spacecraft [4]. In the future, the power supply of commercial power stations will reach GW level, and adopting high voltage power supply systems will become an important direction of future space technology development [5, 6]. In the fields of urban rail traction, new energy vehicles and the new generation of ship power distribution systems, the trend is for developing the voltage level of DC systems to several kV and above, and medium voltage DC power supply systems at kV level have become the focus for development. It can be predicted that high voltage and large capacity DC power supply systems will be fully applied in military and civil fields in the future [7, 8].
For the protection of DC high voltage levels, the large capacity DC contactor is a key device that plays the role of connecting, carrying and breaking the normal circuit, and its breaking characteristics are important factors restricting the performance of its system. In principle, the high voltage DC circuit breaker is generally composed of three branches: the load-carrying branch (main branch), the transfer (breaking) branch and the energy absorbing branch [9]. Because there is no current zero crossing point in the DC arc, a special method is needed to extinguish the arc [10, 11]. The following methods can be adopted [12, 13]: increasing the arc voltage by using multiple groups of near-pole voltage drop, increasing the electric field intensity of the arc column and lengthening the arc, and forcing the current to cross zero by using a forced branch, etc.
Therefore, on the premise of meeting the demand for high voltage and large current DC breaking, this paper firstly proposes a DC natural commutation contactor topology and designs a prototype, which can maintain a low on-state voltage drop when carrying rated current. When breaking the circuit, the asynchronous contact realizes the natural transfer of current, and the arcing contact with high voltage breaking ability completes the breaking of the circuit. Then, based on the Gas Discharge Plasma Database (GPLAS, www.plasma-data.net/index), a two-dimensional magneto-hydrodynamic (MHD) arc model is built by using COMSOL Multiphysics software to simulate the breaking characteristics of multi-contact arcs in series under different background atmospheres. Considering a 1 atm hydrogen environment [14], the dynamic voltage sharing characteristics of arcs under different mechanical action dispersions are studied by designing different initial arc temperature values. Finally, a structural control method is adopted to make the arc voltage of each contact achieve dynamic uniformity in the breaking process, which improved the breaking capacity and switching electrical life.
The contact structure of a DC natural commutation contactor consists of two parts: the load-carrying branch carries rated current, and the arcing branch breaks the circuit. The load-carrying branch and arcing branch are parallel in structure. The assembled contactor prototype and internal current distribution are shown in figure 1. Under the rated condition, a large proportion of the current flows through the load-carrying branch, which limits the improvement of the contact voltage drop and solves the problem of rated temperature rise under large DC current. On contact structure, the moving contacts of the load-carrying branch and the arcing branch are installed on the same electromagnetic operating mechanism, but the design of contacts overtravel is different. The contact overtravel of the load-carrying branch is smaller than that of the arcing branch, so that the main contacts are first opened during the breaking process, and the arcing contacts can still maintain a good circuit conduction state. When breaking the circuit, the internal circuit current will naturally commutate in the contactor. Under certain conditions, the main contact does not ignite an arc during the commutation process. After commutation, the arc voltage can be improved by the sealed gas environment.
As a kind of high temperature plasma which is in a state close to thermodynamic equilibrium, the movement process of an arc can be described by an MHD model during arc extinction. In this paper, the arc MHD model includes the following assumptions. (1) The arc ignition and electrode opening process are ignored, that is, the process of arc extinguishing is simulated under the condition that the opening distance and the initial temperature of the arc are determined. (2) The research object is a macro-neutral Newtonian fluid, and the flow property is weakly compressible. (3) The viscous dissipation and isobaric expansion in the energy equation are neglected. (4) The magnetic field produced by displacement current and arc current is ignored. The movement of the arc depends on the magnetic field generated by the permanent magnet.
Figure 2 shows the geometry of the arc MHD model built using COMSOL Multiphysics and the equivalent process of the model. The voltage, current, derivative of current over time, electrical potential, velocity field, pressure and temperature are calculated by using the electrical circuit, electrical current, laminar flow and heat transfer in fluids interface nodes. The thermal flow and the heat transfer in fluids are coupled through the non-isothermal flow interface, and the electrical current and heat transfer in fluids are coupled through the equilibrium discharge head source interface, where the heat source components consider enthalpy transport and Joule heating.
Due to the symmetry of the structure, the arcs between B1, C1 and D1 contacts are mirror antisymmetric to those between B2, C2 and D2 contacts, so the model can be further simplified. The equivalent process of the cathode and anode terminals is as follows. The static and moving contacts of B2, C1 and D2 in figure 1 are regarded as equipotential, that is, the contacts are kept in contact and no arc is generated. Anode1 and Cathode1 are equivalent to the static and moving contacts of B1 respectively, Anode2 and Cathode2 are equivalent to the static and moving contacts of C2 respectively, Anode3 and Cathode3 are equivalent to the static and moving contacts of D1 respectively, and the equipotential part can be considered to be equivalent to a cylindrical conductor. Since the simplified simulation model corresponds to half of the supply voltage, the external circuit is equivalent to a 1500 V DC power supply, 10 μH equivalent line inductance, and 1.1 Ω load resistance.
The MHD geometric model contains three independent discharge gas regions separated by nylon. The physical parameters of the discharge gas are determined using GPLAS. A magnetic field perpendicular to the plane direction is applied to the three discharge areas, and the magnetic induction intensity is expressed as Bz1, Bz2 and Bz3. In order to realize the reverse motion of the adjacent arc, Bz2 is opposite to the other two magnetic fields. At the initial time of the simulation, the geometric dimension of the arc is set as 2 mm in diameter and 3 mm in length. The initial temperature is T0_arc1, T0_arc2 and T0_arc3. In the MHD model, the magnetic induction intensity is set to 50 mT. The arc initial temperature is set to 13 000 K. In the simulation model, an auxiliary switch is connected at both ends of the contact at different positions, as shown in figure 2(a). Auxiliary switches are used to form different arc motion conditions. In the simulation model, these auxiliary switches are connected in parallel to the gaps at different positions through the 'terminal' interface in the 'electric circuit' module. When the auxiliary switch is closed, since the on-state resistance of the auxiliary switch is much smaller than that of the arc, the current in the circuit will flow through the auxiliary switch, and the arc between the electrodes will not move because there is nearly no current. As shown in figure 2(b), Auxiliary Switch 1 is opened and the current i in the circuit will flow through arc1, resulting in a movement trend under the magnetic field. The time when large current flows into the arc is changed by setting the opening time of the auxiliary switch. The opening sequence of the three auxiliary switches is set respectively to make the arc move at different times under the action of the Lorentz force, resulting in unbalanced voltage. In the simulation model, the opening times of the auxiliary switches are set as 100 μs and 200 μs. Subsequently, the cooled gas gradually recovers its insulation characteristics to complete the circuit disconnection.
The evolution of an arc plasma is the result of the interaction of gas dynamics and an electromagnetic field. According to MHD theory, the Navier–Stokes equation and energy conservation equation can be used to calculate the flow characteristics of the arc extinction process [15, 16]. According to the mass conservation equation, the arc plasma should satisfy the mass continuity theorem, as shown in equation (1).
∂ρ∂t+▽·(ρu)=0 | (1) |
where ρ is the plasma mass density, kg m–3; u is the velocity vector, m s–1.
The velocity distribution of the arc plasma is obtained by solving the momentum equation (Navier–Stokes equation), as shown in equations (2) and (3)
ρ∂u∂t+ρ(u·▽)u=Fm+▽·(-pI+μ[(▽u+(▽u)T)-23(▽·u)I]) | (2) |
Fm=J×B | (3) |
where p is the plasma pressure, Pa; μ is the viscosity, kg (m·s)–1; J is the current density, A m–2; B is the magnetic induction intensity of arc blowing, T. I in equation (2) is a unit matrix of order 3.
The dynamic temperature distribution in the interrupter can be obtained by calculating the energy conservation equation through the coupling of multiple physical interfaces, as shown in equations (4)–(6).
ρCp∂T∂t+ρCpu·▽T=▽·(k▽T)+Q | (4) |
Q=∂∂T(5kBT2q)(▽T·J)+1σJ2 | (5) |
σ=σ(x,y)={σ(T),T≥Tcutoffσmin,T<Tcutoff | (6) |
where Cp is the specific heat at constant pressure, J (kg·K)–1; k is the thermal conductivity, W (m·K)–1; T is the plasma temperature, K. kB is Boltzmann's constant; the variable q in lower case is the elementary charge, equal to 1.602 × 10-19 C; σ is the electrical conductivity, S m–1. In order to obtain the further change of arc plasma temperature at low temperature, the minimum value of electrical conductivity is set in the physical parameters of the arc extinguishing medium. σmin equals 0.02 S m-1, and the corresponding cutoff temperature Tcutoff is 4500 K.
For the wall condition in the model, the no-slip condition is selected, with a no-slip wall where the fluid velocity relative to the wall velocity is zero [17]. For a stationary wall that means that u = 0. The open boundary condition describes a boundary in contact with a large volume of fluid, and fluid can both enter and leave the domain on boundaries with this type of condition.
In this section, under the same initial conditions, MHD modeling and simulation are carried out using the gas physical parameters of H2, N2 and H2–N2 (7:3 mixture ratio, represented by H7N3) in the plasma database under different gas pressures, and the simulation results of voltage distribution during the interruption process are obtained. In order to define the effect of dynamic voltage sharing in the process of breaking, a normalized voltage uniformity coefficient k is used in this work, as shown in equation (7).
k=(1-1n+1n∑i=1|ui(t)-ˉu(t)ˆu|)×100% | (7) |
where n is the number of arcing contacts, which is 3 in this paper;
The simulation results for arc temperature under different pressures in the H2 environment are shown in figure 3. The solid lines in the figure represent the arc current and the arc voltage at different positions (using three colors to distinguish the positions) under the 4 atm condition, the dashed lines indicate the arc current and the arc voltage at different positions under the 2 atm condition and the dot-dashed line indicates the arc current and the arc voltage at different positions under the 1 atm condition.
According to the simulation results, H2 has a good arc extinguishing effect, and the total arcing time is less than 1.22 ms at three pressure points. In particular, the arcing conditions at the maximum power point (Pmax) under each pressure point are marked in figures 3(a)–(c). The arc is elongated under the action of a magnetic field. When the arc voltage increases, the current gradually decreases, and the insulation performance of the gas medium is restored, which realizes the circuit breaking. In addition, when the gas pressure increases, the arc burning time will be decreased correspondingly, and the arc temperature at Pmax is decreased at the same time.
Dynamic voltage sharing coefficients of multi-contact arcs under different gas pressures in the H2 environment are shown in figure 4. Due to the short arcing time, the voltage of each contact is uneven during the breaking process, and the minimum value of the voltage uniformity coefficient is less than 70%. The overvoltage between some contacts is high, so the energy absorbing element should be considered properly.
The simulation results for arc temperature at Pmax under different pressures in the N2 environment are shown in figure 5. Unlike in H2, the arcing time in N2 increases significantly, ranging from 4.94 to 7.8 ms. The arc temperature at the maximum power point of the arc increases slightly with the arcing time. Similarly, the overvoltage between some contacts is also high, so the energy absorbing element should be considered properly.
As shown in figure 6, dynamic voltage sharing coefficients of multi-contact arcs under different gas pressures in N2 can also be maintained at about 85%. The effect of arc dynamic voltage sharing is obvious.
In view of the high overvoltage problem of a single gas in the circuit breaking process, H7N3 is selected as the arc extinguishing medium to study the breaking characteristics and voltage sharing characteristics of a mixed gas. The simulation results for arc temperature at Pmax under different pressures in an H7N3 environment are shown in figure 7.
Compared with the single component gas, the arcing time of the mixed gas is closer to that of the H2 environment, ranging from 1.87 to 3.79 ms. The arc temperature at the maximum power point of the arc is slightly lower, and the dynamic voltage sharing coefficients of the multi-contact arc under different gas pressures in H7N3 have been significantly improved, as shown in figure 8. The voltage uniformity coefficient is about 90%, and it is less affected by gas pressure. In the same way, the overvoltage of the mixed gas arc is obviously lower than that of the single gas arc.
Under the same initial conditions, table 1 summarizes the arcing characteristics of arc extinguishing media under different gas pressures, including the average temperature at the moment of maximum arc power and the arcing time.
Gas | Pressure (×1.01 MPa) | Tave at Pmax (K) | Arcing time (ms) |
H2 | 1 | 9672.5 | 1.22 |
2 | 8939.4 | 0.92 | |
4 | 8367.8 | 0.7 | |
N2 | 1 | 7015.9 | 7.8 |
2 | 6803.2 | 5.97 | |
4 | 6442.5 | 4.94 | |
H7N3 | 1 | 8072.5 | 3.79 |
2 | 7646 | 2.67 | |
4 | 7247.4 | 1.87 |
In this section, research on the voltage equalizing breaking of structural regulation is carried out for an H7N3 arc extinguishing medium under 4 atm. Because of the mechanical dispersion of the opening process, the arc energy between different contacts is not average in the initial stage of arc ignition.
In the simulation process, three structural regulation methods are designed to study the effect of voltage equalizing breaking. Different auxiliary switch breaking intervals are set as follows. Structural control Ⅰ: 100 μs and 200 μs; structural control Ⅱ: 50 μs and 100 μs; and structural control Ⅲ: 30 μs and 60 μs. The initial temperature of the arc at different positions is set as T0_arc1 = T0_arc2 =T0_arc3 = 13 000 K, and the magnetic induction is set as Bz1 = Bz2 = Bz3 = 50 mT. Based on the above simulation conditions, the simulation results for dynamic voltage sharing under structural control are shown in figure 9.
According to figure 9, it can be seen that under the condition of the same arc blowing magnetic induction intensity, the first arc always bears a higher voltage during the dynamic breaking process; the contact breaking time sequence is tB < tC < tD. The uneven arcing energy will lead to a difference in contact material ablation, which acts against improving the electrical life of the switchgear, and also limits the breaking capacity. The dynamic voltage sharing coefficients of multi-contact arcs under different structural control methods are shown in figure 10.
According to the simulation results, three kinds of structural control method can affect the dynamic voltage sharing during the breaking process. However, there is a reasonable structural control range for making the voltage uniformity coefficient reach a higher level. When the contact breaking interval is set from 100 μs/200 μs to 50 μs/100 μs, the voltage uniformity coefficient increases from 44.5% to 76.5%. When the contact breaking interval is set from 50 μs/100 μs to 30 μs/60 μs, the voltage uniformity coefficient increases from 76.5% to 83.8%.
In this work, based on a proposed topology of a DC natural commutation contactor, the voltage sharing breaking simulation of series multi-contact asynchronous breaking is carried out using MHD theory. It can be concluded that:
(1) Based on the MHD theory, a simulation model of three series multi-contact breaking processes is established. Using H2, N2, and H2–N2 mixed gas as the arc extinguishing medium, the arc simulation studies under different gas pressure conditions are carried out and the arc characteristics under different gas types are obtained.
(2) Under the same initial conditions, the arc dynamic voltage uniformity characteristics between different contacts under a series of gas parameters are obtained. Considering the uneven voltage distribution caused by series multi-contact asynchronous breaking, a structural control method is proposed, and a normalized dynamic voltage uniformity coefficient is used to obtain the dynamic voltage sharing effect after regulation.
(3) In view of the mechanical dispersion of the opening process, there is a reasonable structural control range to make the voltage uniformity coefficient reach a higher level. The voltage uniformity coefficient is increased from 44.5% to 76.5% when the contact breaking interval is set from 100 μs/200 μs to 50 μs/100 μs, and correspondingly from 76.5% to 83.8% when the contact breaking interval is set from 50 μs/100 μs to 30 μs/60 μs.
This work is supported by National Natural Science Foundation of China (No. 51977002). This manuscript is recommended by the Third International Symposium on Insulation and Discharge Computation for Power Equipment (IDCOMPU2021). The physical parameters of the discharge gas were determined by GPLAS (www.plasma-data.net/index).
[1] |
Shang Y X et al 2020 IEEE Trans. Ind. Electron. 67 2991 doi: 10.1109/TIE.2019.2905834
|
[2] |
Zhang X Y et al 2019 IEEE Trans. Ind. Electron. 66 7653 doi: 10.1109/TIE.2018.2886787
|
[3] |
Gouda O E, Awaad M I and Afifi Z E 2021 Electr. Power Syst. Res. 199 107442 doi: 10.1016/j.epsr.2021.107442
|
[4] |
Jia B W et al 2020 IEEE Access 8 186540 doi: 10.1109/ACCESS.2020.3030660
|
[5] |
Belda N A, Smeets P P P and Nijman R M 2020 IEEE Trans. Power Deliv. 35 2762 doi: 10.1109/TPWRD.2020.2979934
|
[6] |
Sima W et al 2019 IEEE Trans. Ind. Electron. 66 6979 doi: 10.1109/TIE.2018.2878115
|
[7] |
Qu L et al 2020 Electr. Power Syst. Res. 179 106075 doi: 10.1016/j.epsr.2019.106075
|
[8] |
Wen W J et al 2018 IEEE Trans. Ind. Appl. 54 5456 doi: 10.1109/TIA.2018.2791404
|
[9] |
Li P Y et al 2021 Int. J. Electr. Power Energy Syst. 131 107019 doi: 10.1016/j.ijepes.2021.107019
|
[10] |
Wu R H et al 2019 Plasma Sci. Technol. 21 044002 doi: 10.1088/2058-6272/aafbc7
|
[11] |
Guo Q L et al 2017 IEEJ Trans. Electr. Electron. Eng. 12 465 doi: 10.1002/tee.22401
|
[12] |
Wu Y F et al 2019 IEEE Trans. Ind. Electron. 66 6055 doi: 10.1109/TIE.2018.2870387
|
[13] |
Lindmayer M 2018 IEEE Trans. Plasma Sci. 46 444 doi: 10.1109/TPS.2017.2788450
|
[14] |
Chao X et al 2014 IEEE Trans. Plasma Sci. 42 2722 doi: 10.1109/TPS.2014.2340432
|
[15] |
Niu C P et al 2016 Plasma Sci. Technol. 18 241 doi: 10.1088/1009-0630/18/3/05
|
[16] |
Ma R G et al 2013 IEEE Trans. Plasma Sci. 41 2551 doi: 10.1109/TPS.2013.2273832
|
[17] |
Karetta F and Lindmayer M 1998 IEEE Trans Compon. Packag. Manuf. Technol. Part A 21 96 doi: 10.1109/95.679038
|
[1] | ZHANG Junmin (张俊民), LU Chunrong (卢春荣), GUAN Yonggang (关永刚), LIU Weidong (刘卫东). Calculation of Nozzle Ablation During Arcing Period in an SF6 Auto-Expansion Circuit Breaker[J]. Plasma Science and Technology, 2016, 18(5): 506-511. DOI: 10.1088/1009-0630/18/5/11 |
[2] | ZHONG Jianying (钟建英), GUO Yujing (郭煜敬), ZHANG Hao (张豪). Pressure and Arc Voltage Measurement in a 252 kV SF6 Puffer Circuit Breaker[J]. Plasma Science and Technology, 2016, 18(5): 490-493. DOI: 10.1088/1009-0630/18/5/08 |
[3] | ZHANG Junmin (张俊民 ), CHI Chengbin (迟程缤), GUAN Yonggang (关永刚), LIU Weidong (刘卫东), WU Junhui (吴军辉). Simulation of Arc Rotation and Its Effects on Pressure of Expansion Volume in an Auto-Expansion SF6 Circuit Breaker[J]. Plasma Science and Technology, 2016, 18(3): 287-291. DOI: 10.1088/1009-0630/18/3/12 |
[4] | LIN Xin (林莘), WANG Feiming (王飞鸣), XU Jianyuan (徐建源), XIA Yalong (夏亚龙), LIU Weidong (刘卫东). Study on the Mathematical Model of Dielectric Recovery Characteristics in High Voltage SF6 Circuit Breaker[J]. Plasma Science and Technology, 2016, 18(3): 223-229. DOI: 10.1088/1009-0630/18/3/02 |
[5] | A. K. FEROUANI, M. LEMERINI, L. MERAD, M. HOUALEF. Numerical Modelling Point-to-Plane of Negative Corona Discharge in N2 Under Non-Uniform Electric Field[J]. Plasma Science and Technology, 2015, 17(6): 469-474. DOI: 10.1088/1009-0630/17/6/06 |
[6] | WEI Hao (魏浩), SUN Fengju (孙凤举), YIN Jiahui (尹佳辉), HU Yixiang (呼义翔), LIANG Tianxue (梁天学), CONG Peitian (丛培天), QIU Aici (邱爱慈). Numerical Simulation of Azimuthal Uniformity of Injection Currents in Single-Point-Feed Induction Voltage Adders[J]. Plasma Science and Technology, 2015, 17(3): 235-240. DOI: 10.1088/1009-0630/17/3/11 |
[7] | CHENG Xian (程显), DUAN Xiongying (段雄英), LIAO Minfu (廖敏夫), et al.. The Voltage Distribution Characteristics of a Hybrid Circuit Breaker During High Current Interruption[J]. Plasma Science and Technology, 2013, 15(8): 800-806. DOI: 10.1088/1009-0630/15/8/16 |
[8] | Vahid ABBASI, Ahmad GHOLAMI, Kaveh NIAYESH. The Effects of SF6-Cu Mixture on the Arc Characteristics in a Medium Voltage Puffer Gas Circuit Breaker due to Variation of Thermodynamic Properties and Transport Coefficients[J]. Plasma Science and Technology, 2013, 15(6): 586-592. DOI: 10.1088/1009-0630/15/6/18 |
[9] | YIN Mingli (阴明利), TIAN Canxin (田灿鑫), WANG Zesong (王泽松), FU Dejun (付德君). Influences of Bias Voltage and Target Current on Structure, Microhardness and Friction Coefficient of Multilayered TiAlN/ CrN Coatings Synthesized by Cathodic Arc Plasma Deposition[J]. Plasma Science and Technology, 2013, 15(6): 582-585. DOI: 10.1088/1009-0630/15/6/17 |
[10] | YANG Fei(杨飞), MA Ruiguang ( 马瑞光), WU Yi( 吴翊), SUN Hao( 孙昊), NIU Chunping( 纽春萍), RONG Mingzhe(荣命哲). Numerical study on arc plasma behavior during arc commutation process in direct current circuit breaker[J]. Plasma Science and Technology, 2012, 14(2): 167-171. DOI: 10.1088/1009-0630/14/2/16 |
1. | Lin, J., Wu, J., Tong, Z. et al. Parametric characterization of arcs in semi-sealed splitter plate DC circuit breakers. Journal of Physics D: Applied Physics, 2024, 57(27): 275202. DOI:10.1088/1361-6463/ad39f8 |
2. | Li, J., Peng, S., Yi, C. et al. Optimization Research on DC Air Circuit Breaker at High Altitudes Based on Arc Root Stagnation and Arc Reverse Movement Phenomena. Journal of Electrical Engineering and Technology, 2024, 19(5): 3551-3568. DOI:10.1007/s42835-023-01633-6 |
3. | Junaid, M., Zhao, J., Cao, S. et al. Simulation Study of External Coil on Discharge Characteristics of Liquid Nitrogen Switch Under Multi-Electrode Conditions. IEEE Transactions on Applied Superconductivity, 2024, 34(8): 5000705. DOI:10.1109/TASC.2024.3443016 |
4. | Li, X., Liu, X., Xu, Z. Simulation and Research on Short Circuit Breaking Arc Characteristics of Micro Circuit Breaker. Lecture Notes in Electrical Engineering, 2024. DOI:10.1007/978-981-97-1351-6_3 |
5. | Wang, R., Liao, M., Duan, X. et al. Research on the Arc Characteristics of a New Self-Driving Fault Current Limiter. IEEE Transactions on Plasma Science, 2024, 52(1): 126-133. DOI:10.1109/TPS.2023.3343494 |
Gas | Pressure (×1.01 MPa) | Tave at Pmax (K) | Arcing time (ms) |
H2 | 1 | 9672.5 | 1.22 |
2 | 8939.4 | 0.92 | |
4 | 8367.8 | 0.7 | |
N2 | 1 | 7015.9 | 7.8 |
2 | 6803.2 | 5.97 | |
4 | 6442.5 | 4.94 | |
H7N3 | 1 | 8072.5 | 3.79 |
2 | 7646 | 2.67 | |
4 | 7247.4 | 1.87 |