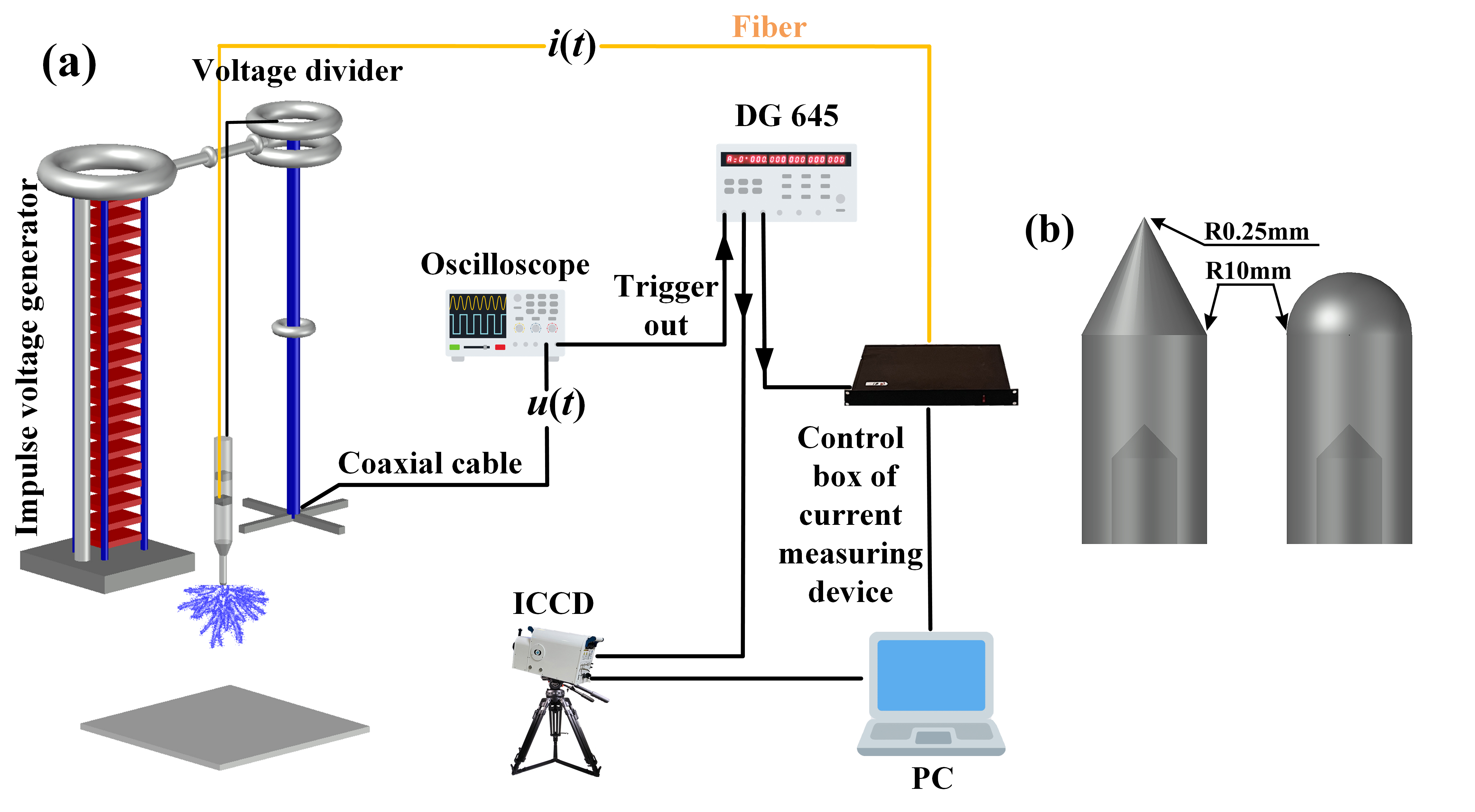
Citation: | Zhiwei LI, Ting LEI, Yu SU, Xiuyuan YAO, Bingxue YANG, Delong LIU, Fangcheng LV, Yujian DING. Dynamic propagation velocity of a positive streamer in a 3 m air gap under lightning impulse voltage[J]. Plasma Science and Technology, 2024, 26(4): 045501. DOI: 10.1088/2058-6272/ad0d51 |
Streamers represent an important stage in the initiation of gap discharge. In this work, we used an eight-frame intensified charge-coupled device camera to capture the streamer development process when a lightning impulse voltage of 95%–100% U50% was applied in a 3 m rod–plate gap and the streamer velocity was analyzed. Analysis of the observations shows that streamer velocity can be defined by three stages: rapid velocity decline (stage 1), rapid velocity rise (stage 2) and slow velocity decline (stage 3). The effects of electrode shape, applied voltage and gap breakdown or withstanding on streamer velocity were analyzed. The electrode with a larger radius of curvature will result in a higher initial velocity, and a higher voltage amplitude will cause the streamer to propagate faster at stage 3. Gap withstanding or breakdown has no obvious effect on streamer velocity. In addition, the experimental results are compared with previous results and the statistical characteristics of the primary streamer discharge are discussed.
Discharge is a key and basic issue in the fields of high-voltage engineering and plasma research. The generation and development of streamers is an important stage in the gap discharge process [1‒5]. In-depth research into the microscopic mechanism of streamer discharge is helpful for improving the theory of gas discharge and reducing the thickness of the insulation during the design of power transmission and transformation equipment [6, 7]. Velocity is an important parameter in the development of streamers, so scholars have analyzed it by different methods.
In 1972, Les Renardières’ group reported some interesting findings concerning the developmental properties of streamers [8]. They estimated the velocity of a streamer by analyzing the results from a streak camera and found that the streamer starts at a high velocity which then decreases because the local field decreases further down the gap. However, due to the limitations of the experimental conditions, only the trend of streamer velocity development was obtained and the estimated results are not accurate.
Grange et al [9] measured the streamer velocity in a 1 cm rod–plate gap using a photomultiplier tube. When the applied voltage was 8 kV, the velocity decreased from the initial 0.5 m μs–1 to 0.2 m μs–1 with the development of the streamer. Wang et al [10] used a Blumlein pulse generator and a streak camera to study the development of positive and negative streamer discharges. When a positive voltage of 43‒90 kV was applied, the streamer velocity was 0.8‒1.2 m μs–1; when a negative voltage of 96 kV was applied, the streamer velocity was about 0.6 m μs–1. The accuracy of the above research results has been improved, but there is a lack of research under conditions of long gaps and multiple influencing factors.
In recent years, more and more researchers have adopted charge-coupled devices (CCDs) and intensified charge-coupled devices (ICCDs) to carry out related studies and obtain more accurate parameters. Wang et al [11] observed the development of streamer discharge in a wire-cylinder electrode using an ICCD camera. It was found that the maximum propagation velocity of the streamer discharge was 1.8‒3.3 m μs–1 at 72‒91 kV and the field strength on the wire surface significantly affected the propagation velocity. Briels et al [12] used a CCD camera to observe the streamer in a point–plate air gap of length 4 cm and found that no streamers were generated for an applied voltage of less than 5 kV. The streamer velocity increased from 0.1 m μs–1 to 4 m μs–1 for an applied voltage of 5‒96 kV. Moreover, the streamer velocity was greatly affected by voltage, voltage rise time and polarity.
Zeng and Chen [13] used 3a four-frame ICCD camera to study the dynamic velocity of a streamer in a 57 cm air gap under lightning impulse voltage. When the voltage amplitude was 250 kV, the streamer velocity decreased from 8.3 ± 2.7 m μs–1 to 0.4 ± 0.1 m μs–1 under a hemispherical electrode. For different electrode shapes, the streamer velocity was v(spherical) > v(hemispherical) > v(conical). Moreover, the streamer velocity increased with increasing rate of the voltage rise. References [14‒19] have also demonstrated important progress in the simulation of the effects of applied voltage, background electric field, voltage polarity, electrode shape and experimental environment on streamer velocity. However, due to the restriction of experimental conditions, most studies on streamer discharge under lightning impulse were carried out in short air gaps with a length of several centimeters to tens of centimeters. There have been fewer experiments on streamer development in meter-scale long air gaps. Also, the scope of observations and studies cannot cover the whole process of streamer development.
In this work, an eight-frame ICCD camera was used to observe the dynamic development characteristics of a streamer in a 3 m rod–plate gap under lightning impulse. The influences of electrode shape, applied voltage and gap withstanding or breakdown on the streamer velocity are analyzed and compared with previous results. The relationships between the inception voltage and the peak current of the primary streamer discharge and the peak value of the impulse voltage are discussed.
The experiment site is in Beijing (55 m above sea level), and a schematic diagram of the experimental layout is shown in figure 1. A positive lightning impulse voltage with a wavefront time of 1.3 μs is generated by a 20-stage 6000 kV/900 kJ Marx generator. The rod–plate gap is 3 m in length. The hollow rod electrode is 1.5 m long with a measuring device placed inside, and the outer metal casing is insulated from the end electrode tip by an insulating layer to prevent the displacement current generated by the shielded casing from flowing through the measuring device via the electrode tip [20]. The plate electrode is a 2 m × 2 m piece of galvanized iron sheeting. Two types of electrode tips were applied in the experiments, as shown in figure 1(b). One is a conical electrode tip with a bottom cross-section radius of 10 mm and a tip radius of 0.25 mm and the other is a hemispherical electrode tip with a radius of 10 mm. Under such experimental conditions, we have U50% = 1670 kV.
The image recording device of the experimental observation system is a SIMX8 ICCD camera. The SIMX8 has eight image sensor channels and can take eight photos in a row with a maximum image resolution of 1280 × 960 pixels. The interval between two adjacent frames can be set from 0 ns to 20 ms and the exposure time can be set from 3 ns to 10 ms. The above two parameters are independently variable between two adjacent frames and the minimum setting amplitude is 1 ns, so we can observe the dynamic development of the streamer more accurately. The voltage was measured by a capacitive voltage divider, and the voltage signal was captured by an oscilloscope. The current recording device, embedded in the rod electrode, mainly comprises a 2 Ω non-inductive resistor and a voltage recorder [20]. The sample rate of the current measuring device was 100 MHz. When a lightning impulse current flows through the non-inductive resistor, the voltage recorder collects the voltage signals at both ends of the non-inductive resistor and transmits them to the controller in the control room through the optical fiber.
When the oscilloscope receives the voltage signal, it immediately sends a trigger signal to the synchronous trigger DG645, which receives the trigger signal and synchronously triggers the image and current acquisition device. Meanwhile, the time delay of the cable, photoelectric conversion and other equipment that transmits the trigger signals should be taken into account. After synchronous calibration, the recording time errors of the image, voltage and current signals were controlled within 20 ns. As shown in figure 2(a), the synchronous observation system starts at time 0 and a current pulse appears at the instant I1, which is caused by the movement of charge carriers in the space at the beginning of the streamer discharge. This instant is identified as the initial time of the streamer. After a preset starting time delay, the ICCD starts shooting at the instant I2. Various color bands in the picture correspond to the shooting instants and exposure time of the ICCD.
When the gap discharges, the atomic energy level transition in the streamer space produces photons. By utilizing an ICCD for shooting and setting different starting shooting instants, exposure times and shooting intervals for the experiments, and then integrating the results based on the development time, more comprehensive spatial motion characteristics of streamer development can be obtained. Figure 2(b) shows the projection of the streamer captured by an ICCD on a two-dimensional plane. The velocity v is calculated as the axial development distance Δy of the streamer between two adjacent frames divided by the time interval ti between two adjacent frames
v=Δyti. | (1) |
It is worth noting that the exposure time of the ICCD in this experiment is mostly set at tens of nanoseconds, whereas the entire streamer development process takes about 3 μs. So, it is necessary to adjust the ICCD’s settings in order to allow the calculated value to cover all stages of streamer development. The advantages of such a setting are that the trend of computing results will be more obvious and have a wider coverage of the timeline. However, the disadvantage is that the computational results are more scattered. At the same time, the wider gap in this experiment compared with previous ones will increase the dispersion of the streamer’s initial time, which also leads to a greater dispersion of the computed velocity results. The experimental results are therefore mostly described in scatter charts.
Figure 3 shows the typical development of a streamer at different spatial ranges of observation and different time scales when 95% U50% is applied to the conical electrode. The streamer size is small during the initial stage of propagation. In order to improve the shooting accuracy at this stage, the focal length of the ICCD was adjusted to set the spatial range of observation to 0.4 m. In the later stage the streamer was about to penetrate the gap, and the experiment was repeated after the spatial range of observation was set to 3 m.
The relationship between streamer velocity and time is shown in figure 4. The figure is the result of integration of multiple sets of data under the same experimental conditions and different shooting modes. In our research, the streamer velocity is defined as having three stages. In stage 1 (initiation‒0.88 μs), the streamer velocity develops at a high initial value and then decreases sharply. The axial propagation velocity reaches the lowest value when t = 0.88 μs. The inset in the upper right of figure 4 shows the result in this stage zoomed in along the timeline. As the streamer develops very quickly during the first stage and is difficult to capture, it is not possible to obtain a stable initial velocity. In stage 2 (0.88‒ 1.30 μs) of streamer development, the streamer velocity increases sharply. At t = 1.30 μs, the velocity peaks at about 1.6 m μs–1. In stage 3 (1.30‒3 μs), the streamer velocity decreases slowly until it penetrates the gap. It takes the streamer about 3 μs to develop onto the plate electrode.
Throughout the streamer development process, the velocity shows a trend of ‘declining rapidly, rising rapidly and then declining slowly’. Specifically, streamer development is fastest at the beginning and its velocity reaches its lowest value at the boundary of stage 1 and stage 2 (t = 0.88 μs). The streamer has the longest propagation time during stage 3, about 1.7 μs.
Next, the above results are analyzed. Figure 5 shows the different stages of development of a streamer. As the streamer discharge region increases during stage 1, the electric field distribution gradually becomes uniform and the electric field in the streamer development area decreases, resulting in a rapid decrease in the streamer velocity. In stage 2, the rising voltage generates a high electric field around the anode and the secondary streamer discharge starts at a high initial velocity and continues to decrease until it converges with the primary streamer [21]. During this stage, initiation of the secondary streamer enhances the electric field in the primary streamer head. Meanwhile, the increased electric field accelerates the propagation of the primary streamer, resulting in an increase in the measured value of the streamer velocity. In stage 3, the secondary streamer completely covers the primary streamer. Thereafter, there is no difference between the primary streamer and secondary streamer. The electric field distribution gradually becomes uniform and the streamer velocity gradually decreases.
As shown in figure 6, an interesting phenomenon was found when using different electrodes in the experiments. Different electrodes will lead to different streamer morphologies. In the experiment, a lightning impulse voltage of 100% U50% was applied. The exposure time was 20 ns at an observation space range of 0.3 m and 500 ns at an observation space range of 3 m.
It can be seen from the figure that the entire streamer discharge area under the two electrodes comprises a sector or a pyramid shape. In the early stage of development, the streamer under the hemispherical electrode with a bigger curvature radius has obvious branches, and its light trajectory has a needle shape. The streamer under the conical electrode with a smaller curvature radius has no obvious branches, and its light trajectory is in a dispersed state. At a late stage of development, the streamer morphology under both electrodes is dispersed and shows no significant difference within a 3 m observation space range. We will focus on those parts where there are differences in the initial stages of the streamer under the two electrodes.
Figure 7 shows the refined measurement results for the initial stage of a streamer under both electrodes. The figure integrates the refined measurement results of the initial stage velocity of the streamer under the same experimental conditions and different shooting modes. From the figure, it can be found that the streamer velocity under the hemispherical electrode starts rapidly and decreases rapidly; the streamer velocity under the conical electrode starts slowly and decreases slowly. At t = 0.44 μs, the streamer velocity is the same under both hemispherical and conical electrodes.
Figure 8 shows the variation of streamer length and velocity with time for gap withstanding and breakdown under the same conditions at t = 0.4‒1.8 μs. The figure shows the results of a single shot, where the linear plot is the length of streamer development and the scatter plot is the streamer velocity. It can be observed that the values and trends for streamer development length and velocity do not differ much in the two cases.
At t = 1.196 μs, the difference in development length is the largest at about 5.2 cm; at t = 1.118 μs, the velocity difference is the largest at about 0.705 m μs–1. Therefore, it can be inferred that there is no significant effect on streamer velocity for gap discharge withstanding or breakdown.
Figure 9 shows the variation of streamer velocity when different voltages are applied. The figure contains the integrated results of multiple sets of data under the same experimental conditions and different shooting modes. The difference between the velocity of the streamer when 95%‒100% U50% was applied is not significant in stages 1 and 2. In stage 3, the higher the applied voltage, the faster the streamer develops. At t = 2.25 μs, the velocity under 100% U50% is about 0.25 m μs–1 higher than that under 95% U50%.
In this section, our experimental results are compared with the typical results of previous work. Morrow and Lowke [22] obtained a positive streamer development law in a 50 mm point–plane gap at an applied voltage of 20 kV by means of simulation. Based on their simulation results, the streamer velocity was divided into three stages: rapid streamer propagation (6‒40 ns), slow streamer propagation (40‒130 ns) and streamer termination (130‒210 ns). In our experiment, the streamer velocity is defined as comprising three stages based on measured and calculated results: rapid velocity decline (stage 1, initiation‒0.88 μs), rapid velocity rise (stage 2, 0.88–1.30 μs) and slow velocity decline (stage 3, 1.30‒3.00 μs). Compared with the simulation results of Morrow and Lowke, our experiment uses a high-precision ICCD to observe the process of streamer velocity recovery when a positive lightning impulse voltage is applied.
Zeng and Chen [13] studied streamer discharge development in a 0.57 m rod–plate gap at an experimental voltage amplitude of 250 kV. For hemispherical and conical electrodes, the streamer velocity decreased rapidly from 3.2 m μs–1 to 0.80 m μs–1 in 50 ns and from 1.7 m μs–1 to 0.5 m μs–1 in 60 ns, respectively. In our experiment, the process of development of a 3 m rod–plate gap streamer was studied. When a voltage of 1670 kV was applied to the hemispherical and conical electrodes, the streamer velocity decreased rapidly from 4.8 m μs–1 to 0.80 m μs–1 in 0.25 μs and from 3.5 m μs–1 to 0.5 m μs–1 in 0.4 μs, respectively. The results of this study and previous studies show that, compared with a conical electrode, a hemispherical electrode has a faster initial velocity and a greater falling rate.
Briels et al [12] at TU/e University studied streamer development at a 0.04 m point–plane gap. The applied voltage was increased from 5 kV to 96 kV, and the streamer velocity increased from 0.1 m μs–1 to 4 m μs–1. In Creyghton et al’s experiment [23], the streamer velocity increased from 2 m μs–1 to 3.5 m μs–1 when a pulse voltage of 20‒25 kV was applied. The present experimental measurements found that the higher the applied voltage at stage 3 the faster the streamer velocity when applying 95%‒100% U50%. Hence, a higher voltage amplitude leads to a greater velocity. References [24‒26] also obtained the same results through experiments and simulations.
The voltage rise rate is another important factor affecting streamer velocity. Komuro et al [27] simulated that when the applied voltage of a 13 mm rod–plate gap was 24 kV and the voltage rise rates were 0.11 kV ns–1 and 0.52 kV ns–1, the average streamer velocities were 0.49 m μs–1 and 0.69 m μs–1, respectively. Winands et al [28] found that when the voltage rise rate increased in the range of 1.5‒2 kV ns–1, the streamer velocity increased from 0.5 m μs–1 to 2.5 m μs–1. In our experiment, the voltage rise rates were 1.22 kV ns–1 and 1.28 kV ns–1, and the average streamer development velocities were 0.9 m μs–1 and 1 m μs–1, respectively. Yagi et al [29] and Yoshinaga et al [30] also did a similar study and concluded that the propagation velocity of the streamer heads increased with a higher rise rate of the applied voltage.
It should be noted that although the initial streamer velocity in this experiment is large, this value is underestimated due to the limitations of the experimental equipment and methodology. In future research, we aim to extend the experiment to extreme environments such as high altitude and low temperature. At the same time, we will explore the universal model of streamer propagation based on the existing data and known influencing factors to obtain a more accurate picture of dynamic streamer development.
In this work, the statistical characteristics of the primary streamer discharge were analyzed for lightning impulse voltages of 90% U50%, 95% U50% and 100% U50% (U50% = 1670 kV; the experiment applying 90% U50% was a supplementary experiment). Figures 10‒12 show the integrated results for multiple sets of data under the same experimental conditions.
Figure 10 shows the relationship between ui, the inception voltage of the primary streamer discharge, and ˆu, the peak value of the impulse voltage. In this figure, the data points represent the results of each experiment and the line segments represent the linear fitting values for ui. The statistical results were aggregated into three groups. Regardless of the voltage range, ui shows a dispersion
ˉui≈ui+δui=364±44kV. | (2) |
It can be seen from the statistical results that the discharge inception voltage ui of the primary streamer and the deviation of inception voltage δui remain approximately constant; the average inception voltage ˉui is almost independent of the peak value of the impulse voltage ˆu. With increase in the statistical samples, ˉui shows minor statistical changes.
Figure 11 shows the relationship between the peak current ip of the primary streamer and the peak value of impulse voltage ˆu. Although there is still dispersion, it is obvious that ip increases with increase in ˆu
ip=k1ˆu+k2. | (3) |
Equation (3) is the fitting result of a linear function. Due to the influence of data dispersion, it is difficult to obtain definite values for k1 and k2. Statistical studies have found that the value range of k1 is [0.004881, 0.006942] and that of k2 is [−5.392, −2.017]. The fitted curve in figure 12 uses the optimal values of both, with k1=0.005912, k2=−3.705.
Figure 12 shows the relationship between the peak current value ip and the discharge inception voltage ui of the primary streamer. It can be seen that there is no obvious correspondence between ip and ui.
In this paper, an experimental study of positive streamer discharge in a 3 m rod–plate gap under lightning impulse voltage is described. Based on an ICCD synchronous observation system, the dynamical development of a streamer in the range of 0.3‒3.0 m is obtained. The following conclusions are obtained from analyzing the experimental results:
(1) When 95%–100% U50% is applied to the two types of electrodes, the streamer velocity shows three stages: rapid velocity decline (stage 1), rapid velocity rise (stage 2) and slow velocity decline (stage 3).
(2) The influence of the electrode on streamer development is studied. When a hemispherical electrode is used, the streamer form gradually evolves from a needle shape at the initial stage to a state of dispersion. When a conical electrode is used, the streamer shows a state of dispersion throughout the development process. The initial streamer velocity of the hemispherical electrode is fast and the falling rate is high, while the initial streamer velocity of the conical electrode is slow and the falling rate is low.
(3) Gap withstanding or breakdown has no obvious effect on streamer development. In addition, when a 100% U50% positive lightning impulse voltage is applied, the streamer velocity is faster than that when 95% U50% is applied in stage 3, but the difference is not obvious in stages 1 and 2.
(4) The statistical characteristics of the primary streamer discharge are discussed. There is no obvious correspondence between the inception voltage and the peak current of the primary streamer discharge or the peak impulse voltage. The peak current of the primary streamer discharge is positively correlated with the peak impulse voltage.
[1] |
Meek J M 1940 Phys. Rev. 57 722 doi: 10.1103/PhysRev.57.722
|
[2] |
Lin B et al 2020 J. Computat. Phys. 401 109026 doi: 10.1016/j.jcp.2019.109026
|
[3] |
Ding Y J et al 2019 Electr. Power Syst. Res. 172 32 doi: 10.1016/j.jpgr.2019.02.024
|
[4] |
Nijdam S, Teunissen J and Ebert U 2020 Plasma Sources Sci. Technol. 29 103001 doi: 10.1088/1361-6595/abaa05
|
[5] |
Mao Y et al 2021 High Voltage Eng. 47 1436 (in Chinese)
|
[6] |
Ebert U et al 2010 J. Geophys. Res. Space Phys. 115 A00E43
|
[7] |
Zou D D et al 2023 Plasma Sci. Technol. 25 072001 doi: 10.1088/2058-6272/acb876
|
[8] |
Les Renardières Group 1972 Research on long air gap discharges at Les Renardières Electra 29 53–157
|
[9] |
Grange F et al 1995 J. Phys. D: Appl. Phys. 28 1619 doi: 10.1088/0022-3727/28/8/011
|
[10] |
Wang D Y et al 2007 IEEE Trans. Plasma Sci. 35 1098 doi: 10.1109/TPS.2007.902132
|
[11] |
Wang D Y et al 2007 IEEE Trans. Plasma Sci. 35 1098 doi: 10.1109/TPS.2007.902132
|
[12] |
Briels T M P et al 2008 J. Phys. D: Appl. Phys. 41 234004 doi: 10.1088/0022-3727/41/23/234004
|
[13] |
Zeng R and Chen S 2013 J. Phys. D: Appl. Phys. 46 485201 doi: 10.1088/0022-3727/46/48/485201
|
[14] |
Serdyuk Y V et al 2001 J. Phys. D: Appl. Phys. 34 614 doi: 10.1088/0022-3727/34/4/323
|
[15] |
Zhuang C J et al 2013 IEEE Trans. Magnet. 49 1929 doi: 10.1109/TMAG.2013.2240669
|
[16] |
Geng J H et al 2022 Plasma Sci. Technol. 24 095402 doi: 10.1088/2058-6272/ac6cd2
|
[17] |
Starikovskiy A Y, Bazelyan E M and Aleksandrov N L 2022 Plasma Sources Sci. Technol. 31 114009 doi: 10.1088/1361-6595/aca04c
|
[18] |
Huang B D et al 2022 Plasma Sources Sci. Technol. 31 114002 doi: 10.1088/1361-6595/ac9c2c
|
[19] |
Ren C H et al 2023 Plasma Sources Sci. Technol. 32 085013 doi: 10.1088/1361-6595/aceeac
|
[20] |
Yue Y S and He J J 2013 Rev. Sci. Instrum. 84 085107 doi: 10.1063/1.4817208
|
[21] |
Shirvani A et al Spatial-temporal investigation of breakdown of long air gaps by lightning voltages up to 2.4 MV In: 2013 IEEE Electrical Insulation Conference (EIC) Ottawa: IEEE 2013
|
[22] |
Morrow R and Lowke J J 1997 J. Phys. D: Appl. Phys. 30 614 doi: 10.1088/0022-3727/30/4/017
|
[23] |
Creyghton Y L M, Veldhuizen E M V and Rutgers W R 1994 IEE Proc. Sci. Measur. Technol. 141 141 doi: 10.1049/ip-smt:19941017
|
[24] |
Huiskamp T et al 2017 Plasma Sources Sci. Technol. 26 075009 doi: 10.1088/1361-6595/aa7587
|
[25] |
Li X et al 2021 Plasma Sources Sci. Technol. 30 095002 doi: 10.1088/1361-6595/ac1b36
|
[26] |
Fu Y W et al 2023 Plasma Sci. Technol. 25 085401 doi: 10.1088/2058-6272/acc16c
|
[27] |
Komuro A, Ono R and Oda T 2013 Plasma Sources Sci. Technol. 22 045002 doi: 10.1088/0963-0252/22/4/045002
|
[28] |
Winands et al 2008 J. Phys. D: Appl. Phys. 41 234001 doi: 10.1088/0022-3727/41/23/234001
|
[29] |
Yagi I et al 2011 IEEE Trans. Plasma Sci. 39 2232 doi: 10.1109/TPS.2011.2154386
|
[30] |
Yoshinaga K et al 2009 Acta Phys. Pol. A 115 1050 doi: 10.12693/APhysPolA.115.1050
|
[1] | Chijie ZHUANG (庄池杰), Zezhong WANG (王泽众), Rong ZENG (曾嵘), Lei LIU (刘磊), Te LI (李特), Min LI (李敏), Yingzhe CUI (崔英哲), Jinliang HE (何金良). Discharge characteristics of different lightning air terminals under composite voltages[J]. Plasma Science and Technology, 2019, 21(5): 51001-051001. DOI: 10.1088/2058-6272/aafdfa |
[2] | Qiming LIN (林启明), Su ZHAO (赵谡), Dengming XIAO (肖登明), Baijie ZHOU (周柏杰). Breakdown characteristics of CF3I/N2/CO2 mixture in power frequency and lightning impulse voltages[J]. Plasma Science and Technology, 2019, 21(1): 15401-015401. DOI: 10.1088/2058-6272/aade83 |
[3] | Yaqi YANG (杨亚奇), Weiguo LI (李卫国), Yu XIA (夏喻), Chuangye YUAN (袁创业). Characteristics of long-gap AC streamer discharges under low pressure conditions[J]. Plasma Science and Technology, 2017, 19(10): 105401. DOI: 10.1088/2058-6272/aa79fe |
[4] | Xiaoqiong WEN (温小琼), Qian LI (李倩), Jingsen LI (李井森), Chunsheng REN (任春生). Quantitative relationship between the maximum streamer length and discharge voltage of a pulsed positive streamer discharge in water[J]. Plasma Science and Technology, 2017, 19(8): 85401-085401. DOI: 10.1088/2058-6272/aa6bf0 |
[5] | Joseph-Marie PLEWA, Olivier DUCASSE, Philippe DESSANTE, Carolyn JACOBS, Olivier EICHWALD, Nicolas RENON, Mohammed YOUSFI. Benchmarks of 3D Laplace Equation Solvers in a Cubic Configuration for Streamer Simulation[J]. Plasma Science and Technology, 2016, 18(5): 538-543. DOI: 10.1088/1009-0630/18/5/16 |
[6] | CHEN She (陈赦), ZENG Rong (曾嵘), ZHUANG Chijie (庄池杰), ZHOU Xuan (周旋), DING Yujian (丁玉剑). Experimental Study on Branch and Diffuse Type of Streamers in Leader Restrike of Long Air Gap Discharge[J]. Plasma Science and Technology, 2016, 18(3): 305-310. DOI: 10.1088/1009-0630/18/3/15 |
[7] | REN Wanbin (任万滨), CHANG Cheng (常成), CHEN Yu (陈宇). Formation Process of Intermittent Molten Bridge Between Au-Plated Contacts at Super Low Breaking Velocity[J]. Plasma Science and Technology, 2016, 18(3): 236-240. DOI: 10.1088/1009-0630/18/3/04 |
[8] | DUAN Ping(段萍), ZHOU Xinwei(周新维), LIU Yuan(刘媛), CAO Anning(曹安宁), QIN Haijuan(覃海娟), CHEN Long(陈龙), YIN Yan(殷燕). Effects of Magnetic Field and Ion Velocity on SPT Plasma Sheath Characteristics[J]. Plasma Science and Technology, 2014, 16(2): 161-167. DOI: 10.1088/1009-0630/16/2/13 |
[9] | WU Jing (吴静), YAO Lieming (姚列明), ZHU Jianhua(朱建华), HAN Xiaoyu (韩晓玉), LI Wenzhu(李文柱). Profile Measurement of Ion Temperature and Toroidal Rotation Velocity with Charge Exchange Recombination Spectroscopy Diagnostics in the HL-2A Tokamak[J]. Plasma Science and Technology, 2012, 14(11): 953-957. DOI: 10.1088/1009-0630/14/11/02 |
[10] | WEN Xiaoqiong (温小琼), Wang Ming (王明), DING Zhenfeng (丁振峰), LIU Guishi (刘贵师). Decoloration of azo dye sunset yellow by a coaxial insulated-rod-to-cylinder underwater streamer discharge system[J]. Plasma Science and Technology, 2012, 14(4): 293-296. DOI: 10.1088/1009-0630/14/4/05 |
1. | Huang, B., Zhou, X., Wang, S. et al. Observation and analysis of positive leader re-illumination in a 10 m ultra-high voltage transmission line gap under switching impulse voltages. Plasma Science and Technology, 2024, 26(10): 105502. DOI:10.1088/2058-6272/ad56cb |
1. | Huang, B., Zhou, X., Wang, S. et al. Observation and analysis of positive leader re-illumination in a 10 m ultra-high voltage transmission line gap under switching impulse voltages. Plasma Science and Technology, 2024, 26(10): 105502. DOI:10.1088/2058-6272/ad56cb |