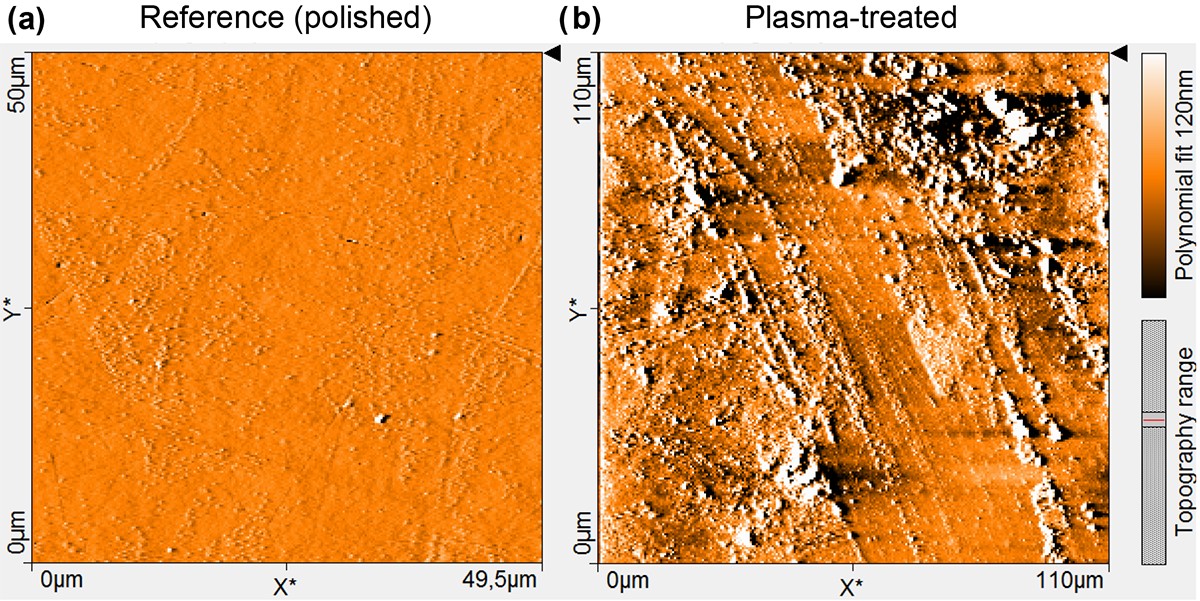
Citation: | Yorick FENNER, Martin BELLMANN, Andreas TÜMMEL, Christoph GERHARD. Feasibility study on the suitability of dielectric barrier discharge plasma treatment of desert sand for concrete production purposes[J]. Plasma Science and Technology, 2025, 27(1): 015504. DOI: 10.1088/2058-6272/ad94cd |
Due to the continuously increasing building and construction industry, sand has become one of the most questioned raw materials worldwide. However, the available amount of sand suitable for concrete production is orders of magnitude lower that the demand and consumption. Even though desert sand is sufficiently available, it is not usable for realizing stable concrete due to its surface shape. Against this background, the suitability of energy-efficient ‘cold’ dielectric barrier discharge plasma operated at atmospheric pressure for improving the properties of concrete produced from desert sand was investigated in this contribution. It is shown that such plasma treatment allows for a certain roughening and re-shaping of sand grains. As a result, the mass flow of treated sand is decreased due to an improved wedging of sand grains. This leads to a certain increase in compressive strength of concrete samples. Even though this increase is marginal, the suitability of the applied type of plasma for modification of the geometry and surface chemistry of sand grains was proven, showing its basic potential for the treatment and preconditioning of sand used for concrete, mortar or plastering.
After water, sand is the most sought-after raw material in the world. The importance of sand as a key resource for the production of glass, asphalt, ceramics, concrete etc. was already highlighted over 50 years ago [1]. However, this apparently omnipresent raw material is not available in unlimited quantities. Moreover, sand mining often has dramatic effects on environment and local ecosystems such as seabeds or rivers and has potentially existential consequences for people and nature [1‒3].
According to a study by Zhang et al, ten billion tons of river sand were mined in the last decade, of which a total of 1.2 billion tons were used for concrete production [4]. Neukirchen and Ries even stated an annual demand for building sand and gravel of around 40 billion tons [5]. In general, the demand for natural river sand exceeds its availability according to Elavenil and Bhoopathy [6]. In addition, the natural supply of sand via erosion is obviously insufficient. As reported by Pettijohn et al, about 44–174 million km3 of Earth’s sediments consist of sand [1]. Per year, approximately 0.05 km3 of quartz sand are additionally generated by natural processes. Comparing these values to the required quantities mentioned above reveals a clear discrepancy. Assuming an average bulk density of 1500 kg/m3, the natural annual generation of ‘new’ sand of 0.05 km3 would result in a total amount of about 75 million tons of quartz sand per year. In contrast, the amount of mined and processed sand exceeds this natural supply by orders of magnitudes.
Obviously, alternative sources are required in the future. Such an alternative to river sand – the best suited sand for the production of concrete due to its properties such as an advantageous particle size distribution and density as well as high cleanliness [7] – for construction purposes was recently presented by Gnanasundar et al in reference [8]. The authors suggested a mixture of granite waste and sea sand. This type of sand is considered to be suitable for simple, non-supporting structures. Compared to river sand, sea sand is moreover available in significantly larger quantities [8]. Moreover, so-called ‘manufactured sand’, which consists of crushed stones, is already being used in India, but merely in negligible proportions. Considering the fact that some states have already banned the use of river sand in construction projects [6], further approaches are urgently required.
Against the background introduced in the previous section, the use of desert sand gains in interest since it is available in extremely large quantities. Moreover, its mining is less questionable from an ecologic point of view and in some cases, it is even necessary for the preservation of ecosystems. However, the general sphere-like shape of desert sand particles, which is caused by wind-induced erosion via rolling friction, makes it almost unusable for the production of stable concrete structures. In order to overcome this restriction, several investigations were carried out in the past [9].
One existing approach of using desert sand as a concrete aggregate is crushing and agglomeration using high-pressure roller presses. Studies have shown that this process leads to a change in grain shape, increasing the wedging of sand grains. In addition, the surfaces of the freshly fractured edges do not yet feature any chemical passivation that occurs in the course of time at ambient conditions. Thus, such edges have a higher reactivity than naturally aged sand, promoting the formation of crystalline compounds with setting cement clinker. This reaction is inhibited for naturally aged sand where grown oxides, iron oxide or phosphate layers lower or prevent the formation of the required calcium silicate phases [10].
The workability and resilience of fibre-reinforced concrete samples prepared with desert sand were investigated by Che et al. It was found that due to the lack of coarse-grained components, a high proportion of desert sand had a negative impact on the elastic modulus of the examined samples [11]. This work shows the practical limits of desert sand admixture for construction purposes. However, a study by Zhang et al has proven sufficient performance of mortar and concrete to which desert sand was added as a fine aggregate. With a cement/sand mixing ratio of less than 1:2, the mortar would not have been qualified for use as a masonry mortar. In contrast, at a ratio higher than 1:2, the performance could reach the requirements of coating mortar [12].
A series of experiments performed by Zhang et al, where the exchange ratio of desert sand to normal sand to achieve optimal concrete properties was investigated, have, however, revealed that maximum increase in compressive strength at room temperature and in flexural strength after increasing the temperature was found at an exchange rate of 40%. This effect can mainly be attributed to the increased compaction of the concrete following from the smaller grain sizes of desert sand. With a higher desert sand content, its lower resilience exceeded the effect of compaction. As a consequence, the stability decreased at desert sand contents above 40% [4].
In recent years, a few studies on the use of plasmas for tailoring sand for concrete production have been reported. Here, the plasma (i) induces a modification of the topography or shape of sand grains and (ii) promotes chemical surfaces processes. Both effects potentially contribute to an increase stability of concrete produced from this sand.
In this context, Bruyako and co-workers have shown that plasma treatment of components of concrete allows for an increase in strength of the final concrete by up to 30%. This improvement is mainly attributed to a chemical modification and accompanying formation of required bounds. Moreover, the curing time was reduced [13]. Such increased curing, mainly caused by plasma-induced chemical modification of fine-grained concrete components, was also reported by Nalbandyan et al [14].
Even though the technological approach of applying plasmas for the treatment of sand prior to concrete production is not yet sufficiently covered in research, it allows for the realization of advantageous effects. However, to our best knowledge, no work on plasma treatment of desert sand was reported in literature up to today. Against this background, the suitability of plasma treatment of desert sand for concrete production purposes was investigated in the present work.
Due to good availability, two types of decoration sand that are usually used for terraria were investigated in this work. This includes white desert sand (‘Terrano desert sand nature’ from Dohse Aquaristik) and red desert sand (‘Terrano Outback’ from Dohse Aquaristik). Moreover, playground sand (‘Playground sand’ from RedSun GmbH & Co. KG) was tested for auxiliary measurements. In contrast to the other types of sand, the origin of the investigated red sand is well known. According to the supplier’s information, it is dug in Vredenburg, South Africa and mainly consists of silicon dioxide (about 95%). It was thus preferentially used in the following experiments.
Own previous work on quartz glass, featuring the same chemical composition as pure sand, i.e., silicon dioxide, has shown that plasma treatment may cause severe chemical modification and change in surface structure [15]. For instance, notable roughening can be induced, as revealed by atomic force micrscopy (AFM) measurements, shown in figure 1.
Moreover, surface analysis via Fourier-transform infrared (FTIR) spectroscopy has proven plasma-induced attachment of hydroxyl (OH) groups as indicated by an increased absorption in the wavenumber region between about 3000 and 3500 cm−1, representing OH-stretching modes. One has to consider that such chemical and topographic changes strongly depend on the type of plasma and the applied plasma parameters such as process gas, plasma power, or discharge distance. The results on glasses were obtained using a so-called dielectric barrier discharge (DBD) plasma. Since in this type of plasma the current is almost completely inhibited, it stands out due to a high energetic degree of efficiency which is required for the treatment of materials in large quantities. It moreover features marginal heating in the range of some degrees to tens of degrees [16] and is thus commonly referred to as a ‘cold’ plasma. Finally, it is normally operated at atmospheric pressure and can thus be applied without any vacuum periphery such as chambers or pumps. Due to these advantageous characteristics, this type of plasma was used in the present work.
Preliminary studies were carried out on single sand grains in order to examine the impact of such plasma treatment of topography. For this purpose, the sand grains were fixed on a sample holder using a commercial glue. The actual plasma treatment was then performed employing a homemade source, which is presented in detail elsewhere [17]. As process gases, air was applied at a flow rate of 15 L/min. since for the intended potential application, an ecological and economical treatment of high quantities of sand, this gas is the most reasonable choice. The applied plasma power was 750 W and the plasma treatment duration was 10 min.
For large-scale treatment of sand, another homemade plasma setup for the treatment of loose material was applied. As shown in figure 2, this setup consists of a rotating drum which acts as ground electrode and moreover allows for the transport and swirling of loose material such as particles or grains. The actual high-voltage electrode is placed within the drum. In operation, where the applied plasma power was 250 W, a double-sided dielectric barrier discharge is ignited and the material is brought in the plasma ignition zone by the drum’s rotation. Since the drum is inclined by about 2.5 degrees, the grains move along the cylinder axis and the line-shaped plasma, respectively. Finally, the plasma source was equipped with an antistatic brush (‘Antistatic Brush AB’ from Elettromeccanica Bonato SAS) for removing charged sand particles that stick to the inner cylinder wall of the rotating drum. The overall plasma treatment duration of the sand was 10 min. As for the above-described preliminary studies at fixed sand grains, ambient air was used as process gas.
In order to identity and quantify the impact of plasma treatment on the characteristics of the investigated sand, different parameters of interest were determined before and after plasma treatment as described hereafter.
The visual examination of the impact of plasma treatment on the shape and topography of sand grains was carried out with the aid of light microscopy. For this purpose, a digital 2D-/3D-microscope (‘VHX-6000’ from Keyence, Corp.) with a magnification range from 500x to 5000x was employed.
One indicator for the roundness and angularity, respectively, of powder or grains such as sand is the mass flow since this value is directly impacted by the mechanical interaction of the grain surfaces. In order to measure this value, a defined amount of sand was sent through a funnel made of glass with a height of 70 mm, an entrance diameter of 40 mm, and an exit diameter of 3.5 mm. The mass flow is then given by the ratio of the mass of sand and the required flow time, which was determined using a digital clock. For increasing the accuracy of measurement, the flow time was measured for different sample sizes, i.e., different masses of sand. As exemplarily shown in figure 3, a linear regression was then applied to the detected data and the flow rate was obtained from the slope of the regression line.
As described in DIN EN 1008, the chemical properties of mixing water used for concrete production are strictly specified. Since a number of quite different chemical processes may occur in the course of plasma treatment using air as process gas, such plasma treatment of the sand might also impact the composition and characteristics of the mixing water, thus finally affecting the compressive strength of the produced concrete. Against this background, 25 g of treated and untreated sand samples were rinsed with 30 g of distilled water. The water was then qualitatively tested for the chemical substances peroxide (O2−2), nitrite (NO−2), and nitrate (NO−3) using reflectometer test strips (‘Reflectoquant’ from Merck KGaA). Moreover, the pH-value of the water was determined with the aid of a pH-meter (tabletop device: ‘FiveEasy’, pH electrode: ‘InLab Expert Pro-ISM’, both from Mettler Toledo).
Finally, the compressive strength of concrete samples produced from treated and untreated sand was measured. The production and storing of the required samples were carried out following DIN EN 12390-2, which is applied for testing hardened concrete. However, due to given experimental conditions and a limited volume of available sand, slight deviations from the standard procedure were required. According to the above-mentioned standard, 1400 g of sand, 350 g of cement and 350 g of water are used to produce a sample block with an edge length of 100 mm. In order to produce cubes with smaller edge lengths (25 mm), the sand and cement proportions were adapted to the smaller sample volume maintaining the appropriate mixing ratio. In addition, the water to cement ratio was reduced to 75%. This value is based on recommendations for the limit value regarding the maximum permissible ratio between the mass of mixing water and the mass of the binder (cement) for concrete in exposure classes XC1 and XC2 according to DIN 1045. The cement used to produce concrete samples was a Portland composite cement (‘ECO COMFORT CEM II/B-M (V-LL) 42.5 N (az)’ from Dyckerhoff GmbH); the used mixing water was tap water. After mixing, the concrete was formed and stored in cubic silicone moulds. In this way, several samples were made from treated sand (n = 16) and untreated sand (n = 21), respectively, for subsequent compressive strength tests. These tests were carried out with a commercial compressive strength tester (type ‘5567’ from Instron GmbH) following DIN EN 12390.
As shown by the comparison of a single sand grain before and after plasma treatment in figure 4, such treatment leads to the emergence of a certain perforation at the sand surface via the generation of single craters. This observation can be explained by the fact that in pulsed plasma discharges, high-energetic plasma streamers with considerable energy density are usually formed. These streamers preferentially ignite towards elevated surface structures such as roughness peaks where the electric field strength is increased [18]. The observed porosity could thus likely be induced by the footprints of such streamers.
Beyond such surface roughening, a certain modification of the sand grain shapes occurred in some cases as shown in figure 5. Such re-shaping by plasma induced erosion was ascertained in case of 8 out of 24 runs, i.e, a third or 33%, respectively, of all of the perfromed experiments. The plasma efficiency for re-shaping could thus be defined to amount to this fraction of about 33%.
Partial erosion of sand can be explained by the impact of reactive plasma species such as atomic or excited nitrogen or hydrogen from the moisture content that are formed in air plasmas. As reported in reference [19], such species may induce a decomposition of the main constituent of sand, silicon dioxide (SiO2), to volatile nitric oxide (NO) or water (H2O). Comparative investigations using pure argon as process gas support the assumption of the importance of such plasma-chemical mechanisms. With inert argon, where physical instead of chemical plasma effects are predominant, no erosion or roughening was achieved. Based on this first insight, subsequent treatment of larger volumes of sand for the production of concrete samples for compressive strength tests was carried out.
The plasma-induced effects introduced in section 4.1 were observed for both white and red desert sand. For large scale plasma treatment, the latter type was used due to the detailed information on this sand such as grain size distribution, chemical composition etc. provided by the supplier. First, the mass flow of the sand was determined according to the procedure described in section 3.3.2. As shown in figure 6, a slight, but statistically significant decrease in mass flow was obtained by the plasma treatment.
Even though this decrease amounts to merely 2.64%±0.92% (from 1.76±0.02 g/s before to 1.71±0.02 g/s after plasma treatment), a measurable plasma-induced impact on the flow characteristics of sand could be ascertained. This effect can be explained by the modification in surface shape and the accompanying change in interaction and wedging of sand grains by the plasma, comparing figures 5(a) and (b). However, one has to consider that the shaping efficiency of the drum setup used for large scale treatment is most likely much lower in comparison to the setup applied for single grain treatment.
Nevertheless, the reduced mass flow correlates with the increased compressive strength of concrete samples produced as described in section 3.3.4. As shown in figure 7, a higher value was obtained for the samples made of plasma-treated sand (15.66±1.07 N/mm²) compared to the ones based on untreated sand (13.97±0.84 N/mm²).
However, no statistical significance could be determined. The minor increase in compressive strength can thus be referred to as a plasma-induced trend. Basically, a dependency of the flow rate and the compressive strength is observed where the latter value increases with decreasing flow rate. This is also confirmed by considering a further type of sand, playground sand (see section 3.1), as shown in figure 8.
One has to consider that the mass flow does not only follow from the shape and surface topography, but also the size of the sand grains. However, the plasma-induced increase in pure mechanical interaction of sand grains seems to play the major role for the observed increase in compressive strength. This assumption is also confirmed by the analysis of water after rinsing treated and untreated sand where obvious differences were observed. Both water samples did not feature any traces of peroxide or nitrite that could be detected using indicator strips. However, a clearly detectable nitrate concentration was found in samples resulting from rinsing plasma-treated sand. In all cases, the discolouration of the test strip occurred clearly and quickly. It can thus be assumed that the nitrate concentration was at the upper end or even above the detection limit of the measuring device of 225 mg/L. Hence, the nitrate concentration in the investigated concrete samples can presumably be even higher than the limit value for the nitrate concentration in concrete of 500 mg/L as specified in DIN EN 1008.
The pH-values allow clearer insights: for water samples gained from untreated sand, neutral values of pH = 6.97±0.04 were detected, whereas the pH-value of water rinsed from treated sand was 3.50±0.67. According to DIN EN 1008, the minimum acceptable pH-value for mixing water in concrete production is 4. The plasma-induced modification of the chemical properties of the mixing water should therefore result in a reduction in the compressive strength of samples made from plasma-treated sand compared to the untreated reference samples. This interrelationship was studied in detail by McCoy and Hermann [20, 21]. In accordance with the specified limit values, concrete samples were assessed as suitable if the concrete samples produced using the mixing water in question exhibited 85% of the strength of a reference sample. However, this value could also be maintained by the samples prepared in the present work with presumably unsuitable mixing water, see figure 7. This observation thus indicates a plasma-induced increase in the mechanical interactions between the sand grains by roughening as stated above.
It was principally shown that dielectric barrier discharge plasma treatment at atmospheric pressure allows for a certain roughening of sand grains. The presented large scale treatment led to a statistically significant reduction in mass flow of sand which can be attributed to such roughening and thus improved canting and wedging of grains. Moreover, plasma-induced surface activation or charging may have taken place, leading to higher interaction between particles and thus better adhesion. It was moreover shown that there is an obvious dependency of compressive strength on mass flow. However, even though a certain trend for improved compressive strength of concrete was determined, significant improvement cannot be stated. It can thus be concluded that the applied plasma has a basic potential for the treatment of desert sand for concrete production purposes. For further development, several weaknesses have to be addressed and overcome.
First, the current approach and apparatus require comparatively long treatment duration which is far too long for the intended final application. The treatment duration could be shortened by several actions as for example increasing the plasma power or adapting the plasma discharge geometry for treating a larger volume in the same time. Second, the concrete samples featured a compressive strength of 15.66±1.07 N/mm², which corresponds to compressive strength class LC12/13 according to DIN EN 206. It is thus a light cement, which is rather suitable for mortar and plastering, and cannot be applied for supporting structures. Hence, the adhesion could further be improved by plasma-induced surface activation of sand grains in addition to roughening by appropriate process gas admixtures. For instance, additional hydrogen can increase the formation of hydroxyl groups on the sand grain surfaces, causing improved hydrophilicity. Moreover, an argon-hydrogen mixture with added nitrogen and oxygen could not only enhance chemical surface reactions, but also improve the efficiency of the plasma ignition due to the lower required ignition voltage in case of argon as carrier gas. Third, the current DBD-plasma features comparatively high homogeneity. It can be assumed that more inhomogeneous discharges consisting of single high-energetic streamers might increase the effect of surface roughening and thus wedging of sand grains. Such filamentary discharges can also be operated at DBD and thus at low energy consumption.
Hence, it can be summarized that even though the suitability of ‘cold’ atmospheric pressure plasma treatment of desert sand was principally shown, extensive work has to be carried out in the future for making this approach suitable for an application in an appreciable level. Since alternative processes for ensuring the availability of appropriate sand for concrete constructions are imperatively needed, the presented approach could contribute to addressing this demand partially after further development.
Data underlying the results presented in this paper are not publicly available at this time but may be obtained from the authors upon reasonable request.
This research was funded by the Bundesministerium für Bildung und Forschung (Nos. 13FH6I06IA and 13FH6I08IA).
[1] |
Pettijohn F J, Potter P E and Siever R 1973 Sand and Sandstone (Berlin: Springer) 1 ISBN 3540055282
|
[2] |
Torres A et al 2017 Science 357 970 doi: 10.1126/science.aao0503
|
[3] |
Gunaratne LHP 2010 Economy and Environment Program for Southeast Asia ISBN 9789810877095
|
[4] |
Zhang M H et al 2019 Appl. Sci. 9 4151 doi: 10.3390/app9194151
|
[5] |
Neukirchen F and Ries G 2016 Industrieminerale, Steine und Erden In: Neukirchen F and Ries G Die Welt der Rohstoffe (Berlin: Springer) p. 317 ISBN 9783642377389 (in German
|
[6] |
Elavenil S and Bhoopathy V 2013 Int. J. Civil Eng. Res. Dev. 3 1 doi: https://papers.ssrn.com/sol3/papers.cfm?abstract_id=3513295
|
[7] |
Abdias M W M et al 2023 Open J. Civil Eng. 13 353 doi: 10.4236/ojce.2023.132027
|
[8] |
Gnanasundar V M, Suvetha S and Preethy S 2019 AIP Conf. Proc. 2128 020011 doi: 10.1063/1.5117923
|
[9] |
Cai H et al 2020 Adv. Civil Eng. 2020 8875922 doi: 10.1155/2020/8875922
|
[10] |
Jörg B 2017 Use of treated desert sand as an aggregate for concrete WO2017178362A1
|
[11] |
Che J L et al 2019 Appl. Sci. 9 1857 doi: 10.3390/app9091857
|
[12] |
Zhang G X et al 2006 Build. Environ. 41 1478 doi: 10.1016/j.buildenv.2005.05.033
|
[13] |
Bruyako M G et al 2014 Adv. Mater. Res. 1040 730 doi: 10.4028/www.scientific.net/AMR.1040.730
|
[14] |
Nalbandyan G, Soloviev V and Ushkov V 2019 Mater. Today Proc. 19 1841 doi: 10.1016/j.matpr.2019.07.024
|
[15] |
Gerhard C et al 2012 Plasma Chem. Plasma Proces. 33 895 doi: 10.1007/s11090-013-9471-7
|
[16] |
Gredner A et al 2013 J. Mater. Sci. Eng. B 3 346 doi: 10.17265/2161-6221/2013.06.002
|
[17] |
Bellmann M et al 2024 Plasma Process. Polym. 21 2300224 doi: 10.1002/ppap.202300224
|
[18] |
Gerhard C et al 2013 J. Eur. Opt. Soc. Rapid Publ. 8 13081 doi: 10.2971/jeos.2013.13081
|
[19] |
Gerhard C, Viöl W and Kretschmer M 2012 Opt. Photonik 7 35 doi: 10.1002/opph.201290098
|
[20] |
McCoy WJ 1989 ASTM Special Publication 196B 765 doi: 10.1520/STP49900S
|
[21] |
Hermann K 1996 Cementbulletin 64 3 (in German doi: https://www.e-periodica.ch/digbib/view?pid=cem-001%3A1996%3A64%3A%3A11#1121.0b21
|
[1] | Abba Alhaji BALA, Ping ZHU, Haolong LI, Yonghua DING, Jiaxing LIU, Sui WAN, Ying HE, Da LI, Nengchao WANG, Bo RAO, Zhijiang WANG. Quasi-static magnetic compression of field-reversed configuration plasma: amended scalings and limits from two-dimensional MHD equilibrium[J]. Plasma Science and Technology, 2023, 25(2): 025106. DOI: 10.1088/2058-6272/ac92cc |
[2] | Songru XIE (谢松汝), Yong HE (何勇), Dingkun YUAN (袁定琨), Zhihua WANG (王智化), Sunel KUMAR, Yanqun ZHU (朱燕群), Kefa CEN (岑可法). The effects of gas flow pattern on the generation of ozone in surface dielectric barrier discharge[J]. Plasma Science and Technology, 2019, 21(5): 55505-055505. DOI: 10.1088/2058-6272/aafc50 |
[3] | LI Guozhan(李国占), CHEN Fu(陈浮), LI Linxi(李林熙), SONG Yanping(宋彦萍). Large Eddy Simulation of the E?ects of Plasma Actuation Strength on Film Cooling Efficiency[J]. Plasma Science and Technology, 2016, 18(11): 1101-1109. DOI: 10.1088/1009-0630/18/11/08 |
[4] | QI Xiaohua (齐晓华), YANG Liang (杨亮), YAN Huijie (闫慧杰), JIN Ying (金英), HUA Yue (滑跃), REN Chunsheng (任春生). Experimental Study on Surface Dielectric Barrier Discharge Plasma Actuator with Different Encapsulated Electrode Widths for Airflow Control at Atmospheric Pressure[J]. Plasma Science and Technology, 2016, 18(10): 1005-1011. DOI: 10.1088/1009-0630/18/10/07 |
[5] | JIAO Juntao (焦俊韬), XIAO Dengming (肖登明), ZHAO Xiaoling (赵小令), DENG Yunkun (邓云坤). Analysis of the Molecules Structure and Vertical Electron Affinity of Organic Gas Impact on Electric Strength[J]. Plasma Science and Technology, 2016, 18(5): 554-559. DOI: 10.1088/1009-0630/18/5/19 |
[6] | WAN Gang (弯港), JIN Yong (金涌), LI Haiyuan (李海元), LI Baoming (栗保明). Study on Free Surface and Channel Flow Induced by Low-Temperature Plasma via Lattice Boltzmann Method[J]. Plasma Science and Technology, 2016, 18(3): 331-336. DOI: 10.1088/1009-0630/18/3/19 |
[7] | JIN Ying (金英), REN Chunsheng (任春生), YANG Liang (杨亮), ZHANG Jialiang (张家良), et al.. Atmospheric Pressure Plasma Jet in Ar and O 2 /Ar Mixtures: Properties and High Performance for Surface Cleaning[J]. Plasma Science and Technology, 2013, 15(12): 1203-1208. DOI: 10.1088/1009-0630/15/12/08 |
[8] | LI Zhanguo (李战国), LI Ying (李颖), CAO Peng (曹鹏), ZHAO Hongjie (赵红杰). Surface Decontamination of Chemical Agent Surrogates Using an Atmospheric Pressure Air Flow Plasma Jet[J]. Plasma Science and Technology, 2013, 15(7): 696-701. DOI: 10.1088/1009-0630/15/7/17 |
[9] | LIU bo (刘波), YANG JiJun (杨吉军), JIAO Guohua (焦国华), XU KeWei (徐可为). Improvement of Interfacial Adhesion Strength and Thermal Stability of Cu/p-SiC:H/SiOC:H Film Stack by Plasma Treatment on the Surface of Cu Film[J]. Plasma Science and Technology, 2012, 14(7): 619-623. DOI: 10.1088/1009-0630/14/7/12 |
[10] | LIANG Haoming (梁浩明), XIAO Chijie (肖池阶), ZHOU Guiping(周桂萍), PU Zuyin(濮祖荫), WANG Honggang (王红刚), WANG Xiaogang (王晓钢). Alfvénic Fluctuations in an Interplanetary Coronal Mass Ejection Observed Near 1 AU[J]. Plasma Science and Technology, 2012, 14(2): 102-106. DOI: 10.1088/1009-0630/14/2/04 |