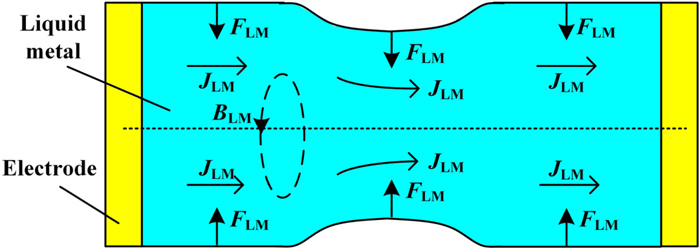
Citation: | Jinjin LI, Xiongying DUAN, Zhihui HUANG, Weiying XIE, Minfu LIAO, Chang MA, Jia TAO. Study on the formation of arc plasma on the resistive wall liquid metal current limiter[J]. Plasma Science and Technology, 2023, 25(8): 085507. DOI: 10.1088/2058-6272/acc235 |
Due to its significant attributes, the liquid metal current limiter (LMCL) is considered a new strategy for limiting short-circuit current in the power grid. A resistive wall liquid metal current limiter (RWLMCL) is designed to advance the starting current-limiting time. Experiments are performed to investigate the dynamic behaviors of liquid metal, and the influence of different currents on the liquid metal self-shrinkage effect is compared and analyzed. Furthermore, the liquid metal self-shrinkage effect is mathematically modeled, and the reason for the formation of arc plasma is obtained by simulation. The laws of arc plasma formation and the current transfer in the cavity are revealed, and the motion mechanisms are explained by physical principles. The simulations are in accordance with the test data. It is demonstrated that the sudden change of the current density at both ends of the wall causes the liquid metal to shrink and depress under the electromagnetic force, and the current starts to transfer from the liquid metal path to the wall resistance path. The RWLMCL can effectively advance the starting current-limiting time.
With the rapid expansion of modern power grids and the continuous operation of large-capacity groups, the system structure has been complex, the short-circuit fault forms have become diverse, and the short-circuit current has increased. Simultaneously, the requirements for various electrical equipment are more stringent, which has become a difficult problem that restricts the development of the power grid [1-4].
The fault current limiter (FCL) can lower mechanical and thermal stress while limiting short-circuit current and enhancing system stability [5]. At present, several FCLs have been put forward in academia, such as the positive temperature coefficient (PTC), the superconductor, the power electronic device, and liquid metal [6-11]. The liquid metal current limiter (LMCL) has the significant attributes of having a simple structure, no control device, a fast response, and self-recovery characteristics [12]. It has become an alternative new current-limiting technology.
The liquid metal self-shrinkage effect is the process in which the current flowing through the liquid metal interacts with the magnetic field generated by itself, causing the liquid metal path to shrink, as shown in figure 1. According to Ampere's law, when the liquid metal flows through a current with an axial current density JLM, a closed magnetic field BLM will be generated in each liquid column inside the liquid metal. The interaction of current and magnetic field produces the Lorentz force FLM, which produces a radial pressure gradient. The liquid metal column will shrink rapidly once short circuited.
In order to improve the performance of the existing insulating wall LMCL (IWLMCL), for example, to reduce ablation and advance the starting current-limiting time, some methods have been proposed. Combining experiments and numerical simulations, researchers in [13] were concerned with the investigation of the behaviors of the LMCL, and a decompressed structure LMCL was designed to reduce the high pressure of the burning arc process. According to [14], a new LMCL using an active triggering approach to the burn arc was developed to improve fault response function and rated current-carrying capability. Rong et al [15] conducted tests to explore the liquid metal self-shrinking behaviors and explored the root of electrode ablation. However, the above-mentioned methods do not fundamentally solve the problem of serious ablation and slow current limiting. At present, the IWLMCL is only applicable to the current-limiting field of medium and low voltage. In order to develop the LMCL into the field of high-voltage current limiting, our previous research put forward a new FCL topology consisting of a resistive wall LMCL (RWLMCL), fast switch and reactor, and proved that the new FCL can effectively suppress arc ablation and improve current-limiting efficiency [6, 12]. However, we do not systematically explain the change process of the liquid metal self-shrinkage effect and the reason for the formation of arc plasma in the RWLMCL.
Many scholars have made excellent achievements on the liquid metal self-shrinkage effect and the dynamic change of arc plasma. In order to research the impact of the arc on the LMCL electrodes ablation, Liu et al [16] simulated the arc. Based on the three-dimensional finite element method (FEM), a magnetohydrodynamic physical model of the liquid metal self-shrinkage effect of IWLMCL was carried out, as detailed in [17]. However, the research object is the IWLMCL, not the RWLMCL.
Simultaneously, the liquid metal self-shrinking stability under the action of current has been studied. When an axial current passed through a cylindrical liquid metal, the shrinkage instability was studied, as explored in [18]. Kang et al [19] studied the stability of the liquid metal free surface under a gradient magnetic field through experiment and simulation. However, the dynamic change of resistive wall sharing current is not considered in the liquid metal self-shrinking process.
To sum up, in order to fundamentally improve the current-limiting speed of the LMCL, a RWLMCL is designed based on the liquid metal self-shrinkage effect. In addition, it is necessary to study the principle of liquid metal self-shrinkage and arc plasma in the RWLMCL. In this work, to explore the mechanism of the liquid metal self-shrinkage, arc plasma formation process, and the transfer process of a short-circuit current, a finite element mathematical model is established. Utilizing the fluid simulation software Fluent, the liquid metal gas and liquid phases diagrams are obtained. In particular, the current density, magnetic induction intensity, and Lorentz force of the liquid metal at different times are specifically analyzed. Finally, the transfer process of the short-circuit current from the liquid metal path to the wall resistance path is studied.
Figure 2 is a structural schematic diagram of the RWLMCL designed in this work. A rectangular epoxy resin shell with external measurements of 200 mm × 200 mm × 100 mm makes up the RWLMCL's exterior. The top is made of lucent glass, which on one hand keeps the liquid metal from splashing and on the other hand makes it easy to utilize a high-speed camera to record the dynamic behaviors of the liquid metal. Two electrodes are located at both ends of the cavity. There are two identical grooves for placing the liquid metal. The detachable wall is located in the center of the cavity. The cylindrical channel on the wall has dimensions of 10 mm in diameter and 20 mm in length. To facilitate the observation of the liquid metal dynamic process, the top of the channel is cut, and then a borosilicate glass is bonded, thus forming a confining space. The liquid metal is filled in the cavity and can flow freely through the channel. The remaining cavity is filled with air, which is the same as the external atmospheric pressure [12].
During normal operation of the system, current passes through the left electrode, the liquid metal path, and the right electrode. The resistance of the circuit is nearly zero. When short-circuiting, the liquid metal's initial shrink causes the current to be moved from the liquid metal path to the wall resistance path. The liquid metal and resistive wall share the current, and the impedance of the RWLMCL progressively increases. When the liquid metal burns arc, the resistance of the RWLMCL further rises. After the fault is eliminated, the liquid metal flows back to the channel.
GaInSn alloy is selected as the liquid metal in this work. It is mixed with 68.5% Ga, 21.5% In, and 10% Sn. GaInSn is a non-toxic, low melting point liquid alloy with high thermal and electrical conductivity [13]. At room temperature, the density, dynamic viscosity coefficient, electrical conductivity, and surface tension of the GaInSn are 6400 kg m-3, 2.4 × 10-3 N·s/m2, 3.4 × 106 S m-1, and 0.533 N m-1, respectively [17].
After many simulations and experiments [20], it is determined that the conductivity of the RWLMCL wall material is between 3.4 × 105 S m-1 and 3.4 × 106 S m-1 in practical applications [6, 12]. Kovar 4J29 with a volume of 40 mm × 20 mm × 40 mm is selected as the RWLMCL wall material for experiments. The conductivity and magnetic permeability of Kovar 4J29 are 2.08 × 106 S m-1 and 2 × 10-3 T·m/A respectively. Its excellent performance makes Kovar 4J29 a good candidate for use as an electrical system component. Kovar 4J29 can be used in liquid metal discharge devices since it does not react with liquid metals like mercury [21]. Specially, Kovar 4J29 has distinct expansion characteristics. Similar to the borosilicate glass, it has same expansion coefficient and contraction rate. They can be properly bonded to prevent glass from breaking [22].
The experimental setup shown in figure 3 is built using the RWLMCL. The LC single-frequency oscillation circuit is used as the experimental power supply. The current IRWLMCL and voltage URWLMCL of the RWLMCL are collected respectively. The high-speed camera is positioned perpendicular to the transparent glass to shoot the dynamic behaviors of liquid metal [6, 12]. The controller controls the opening and closing of the circuit switch CB, and triggers the camera. The liquid metal level is 5 mm from the bottom of the channel. The prospective current is determined by the discharge of LC oscillating power supply with no load.
In this work, the circuit shown in figure 3 is used to measure the resistance of the resistive wall. The LC oscillating power supply discharges the resistive wall. When the current is small, the wall will not generate an arc, so a current with a peak value of less than 1 kA can be selected. The current IWall and voltage UWall are obtained through many experiments. The resistance value of the resistive wall can be calculated by using the formula Rwall = UWall/IWall, and then compared with RWall = ρWall LWall/SWall calculated values (ρWall, LWall and SWall are the resistivity, resistance length, and resistance section area, respectively). Finally, the resistance value of the resistive wall is obtained. The total resistance value of the RWLMCL is also the same, which can be obtained by the LC oscillating power supply and calculation.
Before the tests, the circuit switch CB is opened, and the DC charging system charges the capacitor bank C. Once the capacitor bank C reaches the experimental value, the controller controls the CB to close. Assuming that at the time 0 ms, the CB is fully closed, the LC oscillation power supply discharges the RWLMCL. Then, the controller triggers the camera.
Figure 4 shows the four processes of the dynamic behaviors of liquid metal. The time T0-T1 is the normal operation process; the time T1-T2 is the liquid metal self-shrinking process; the time T2-T3 is the burn arcs process, and the time T3-T0 is the liquid metal self-recovery process.
In order to more clearly describe the liquid metal self-shrinking dynamic behaviors and the characteristics of current transfer from the liquid metal path to the wall resistance path, three key parameters are defined for the normal operation process and the liquid metal self-shrinking process.
As shown in figures 4(a) and (b), the time from T0 to T1 is defined as the pre-liquid metal shrinking time TN. TN is a parameter used to describe the difficulty of the liquid metal self-shrinkage. The smaller the TN, the easier the liquid metal shrinks. TN can be expressed as:
TN=T1−T0. | (1) |
As illustrated in figures 4(b) and (c), the time from T1 to T2 is defined as the liquid metal self-shrinking time TS. TS is a parameter used to define how quickly the liquid metal shrinks. It is assumed that different currents cause the liquid metal to shrink at the same distance. The smaller the TS, the faster the liquid metal shrinks. TS can be represented as:
TS=T2−T1. | (2) |
To describe the current transfer speed from the liquid metal path to the wall resistance path, the resistance change rate Rδ is defined. Rδ represents a parameter of the current transfer speed. The larger the Rδ, the faster the current transfer speed. Rδ can be written as:
Rδ=(RS−R0)/TS | (3) |
where R0 is the inherent resistance of the RWLMCL, and RS is the resistance at the moment before the liquid metal burning arcs.
We have done a preliminary study [12, 20], replacing the wall material in figure 2 with acrylic to simulate the existing IWLMCL [13-18, 23-25]. Using the experimental circuit of figure 3, experiments are performed on the IWLMCL. Moreover, other experimental conditions are consistent with those of the RWLMCL. For the RWLMCL and IWLMCL, each current test is repeated ten times respectively.
According to [12-18, 23-25], the IWLMCL begins to limit current at the time when the liquid metal generates gaps with the channel's bottom, that is, the time T2 shown in figure 4(c). It is assumed that the starting current-limiting time of the IWLMCL is TIA. The starting current-limiting time of the IWLMCL is the sum of the pre-liquid metal shrinking time TN and the liquid metal self-shrinking time TS, that is, TIA = TN + TS. However, starting from the liquid metal shrinking (time T1), the liquid metal path current is gradually transferred to the wall resistance, and the RWLMCL begins to limit the current.
Under the different short-circuit currents, the test curves of the pre-liquid metal shrinking time TN and the liquid metal self-shrinking time TS of the RWLMCL, and the starting current-limiting time TIA of the IWLMCL are shown in figure 5.
As can be seen from figure 5, as the current increases, the TN, TS and TIA show a downward tendency, and the standard deviations of the above three parameters also gradually decrease.
In summary, the greater the current, the easier the liquid metal shrinks, and the faster the self-shrinking speed. Moreover, the RWLMCL starts to limit the current earlier than the IWLMCL.
Figure 6 is a comparison diagram of the resistance change rate Rδ of the RWLMCL and IWLMCL in the liquid metal self-shrinking process under different short-circuit currents.
Figure 6 shows that the resistance change rate Rδ of the IWLMCL is zero. During the time from T0 to T2, the resistance of the IWLMCL will hardly change. However, the resistance change rate Rδ of the RWLMCL shows an upward tendency as the current increases. Moreover, the standard deviation incrementally increases. When the current is greater than 2.329 kA, the resistance change rate Rδ of the RWLMCL increases faster. The velocity of current transfer from the liquid metal path to the wall resistance path increases. It is considered that the above phenomenon is related to the current peak and rise rate. The higher the current, the smaller the liquid metal self-shrinking time TS. This results in an increase in the rise rate of Rδ.
The experimental RWLMCL waveforms are obtained as illustrated in figure 7 when the prospective peak current is 1.28 kA. Among them, IRWLMCL is the current flowing through the RWLMCL, and URWLMCL is the voltage across the RWLMCL. RRWLMCL is the resistance of the RWLMCL, which is obtained by calculating RRWLMCL = URWLMCL/IRWLMCL.
In this experiment, the camera records the dynamic behaviors of liquid metal at a speed for recording of 10 000 frames/s. Figure 8 shows the dynamic behaviors of liquid metal when the controller triggers the camera.
According to the experimental results, this section specifically analyzes the dynamic behavior mechanism of liquid metal. Combined with figure 4, the dynamic behaviors of liquid metal are divided into four stages: the normal operation stage, the liquid metal self-shrinking stage, the burn arcs stage, and the liquid metal self-recovery stage.
Figures 8(a) and (b) show that the time from 0 to 10.20 ms is the normal operation stage, and the free liquid metal level does not change. Moreover, the resistance at both ends of the RWLMCL is basically unchanged, R0 = 0.22 mΩ. The voltage URWLMCL is proportional to the current IRWLMCL. At this stage, the RWLMCL has a lower limit on the short-circuit current.
Figures 8(b)-(e) show that the time from 10.20 to 16.60 ms is the liquid metal self-shrinking stage. At 10.20 ms, the liquid metal starts to shrink and depress at the four corners. Subsequently, the depressions gradually deepen and expand in the channel and grooves. Moreover, the liquid metal depresses on the left side faster than on the right side. Simultaneously, the liquid metal of the channel decreases and flows to the grooves. At this stage, the resistance of the RWLMCL increases in two periods due to the different depression speeds on both sides of the wall. The first period's resistance rises from 0.22 to 0.81 mΩ. After 2.8 ms, the resistance of the second period increases to 1.12 mΩ. The resistance change rate Rδ = 0.141 Ω/s. According to figure 7, the current is gradually transferred from the liquid metal path to the wall resistance path when the liquid metal begins to depress. Further, the voltage of the RWLMCL shows the trend of first increasing and then slightly decreasing.
Figures 8(e)-(g) show that the time from 16.60 to 32.00 ms is the burn arcs stage, and the depressions in the grooves continue to expand toward the electrodes. At 32.00 ms, the depressions reach the maximum. During this period, the arcs are burned many times. At 16.60 ms, the arcing starts at the place where the left groove is far away from the channel. However, the arcing intensity is low and the arc time is short. At 25.20 ms, the arc is burned at the place where the left groove is close to the channel. The arcing intensity increases slightly. The RWLMCL resistance tends to increase due to the depression expansion and multiple burn arcs of the liquid metal. Further, the voltage URWLMCL has a tendency to increase first and then decrease.
Figures 8(g)-(i) show that the time from 32.00 to 480 ms is the liquid metal self-recovery stage. Because it is less affected by the current, the liquid metal flows freely in the channel and grooves under the action of its own inertia. At 480 ms, the liquid metal surface returns to calm, and the next current limit can be carried out. Although the arcs are no longer burned, many huge depressions are still formed due to the liquid metal sloshing with a free surface. This causes the resistance to increase and then decrease. At this stage, the voltage decreases at an accelerated rate to zero at 44.10 ms.
In summary, the wall changes from insulation to resistance, and the liquid metal self-shrinkage effect is proved to be still effective. The dynamic behaviors of liquid metal can be divided into four stages, and these four stages are closely related to the resistance and voltage of the RWLMCL.
According to the experimental results, we still have the following two points to make a profound study. The first one is why the liquid metal starts to shrink and depress at the four corners where the two ends of the channel are connected with the inner wall, while the second one is how the current transfers from the liquid metal path to the wall resistance path.
The liquid metal self-shrinking process of the IWLMCL has been simulated [13, 16-19, 24, 25]. To reveal the mechanism of the liquid metal self-shrinkage effect and the dynamic changes of current transfer, the liquid metal self-shrinkage effect is mathematically modeled by combining the turbulence model, volume of fluid (VOF) model and magnetohydrodynamic (MHD) model. This mathematical model involves the coupling of multi-physics fields such as the electric field, magnetic field, and gas-liquid two-phase flow field.
In this work, the Reynolds averaging method is used to calculate the turbulence. Further, the k-ω turbulence model is adopted. The model can penetrate the entire boundary layer when the near-wall mesh density meets the conditions, and is suitable for wall-constrained fluids. The model of two equations is used in the simulation analysis.
The volume fraction of the liquid metal phase in a unit is defined as αL. The unit filled with liquid metal is denoted by αL = 1; the unit filled with air is denoted by αL = 0; 0 < αL < 1 denotes the existence of a gas-liquid free interface.
The interface transport equation of the VOF model is:
\frac{\partial \alpha_{\mathrm{L}}}{\partial t}+\boldsymbol{v} \cdot \nabla \alpha_{\mathrm{L}}=0 | (4) |
where t is the time, and v is the fluid velocity. The simulation includes Lorentz force, gravity and surface tension. The Navier-Stokes equations are used to solve the fluid velocity of the fluid, and the continuity equation and momentum equation are:
\left\{\begin{array}{l} \nabla \boldsymbol{v}=0 \\ \rho \frac{\partial \boldsymbol{v}}{\partial t}+\rho \boldsymbol{v} \cdot \nabla \boldsymbol{v}=\mu \nabla^2 \boldsymbol{v}-\nabla \boldsymbol{P}+\boldsymbol{J} \times \boldsymbol{B}+\rho g+\boldsymbol{F}_\delta \end{array}\right. | (5) |
where ρ is the fluid domain density, μ is the viscosity coefficient, P is the pressure, J is the current density, B is the magnetic induction intensity, Fδ is the surface tension, and g is the gravitational acceleration, g = 9.8 m s-2.
Maxwell's equations are used to solve the electric field, and the magnetic vector equation is used to calculate the magnetic field of the fluid domain in the cavity, which can be expressed by equation (6).
\left\{\begin{array}{l} \nabla(\sigma \nabla \varphi)=0 \\ \boldsymbol{E}=-\nabla \varphi \\ \boldsymbol{J}=\sigma \boldsymbol{E} \\ \boldsymbol{B}=\nabla \times \boldsymbol{A} \end{array}\right. | (6) |
where φ is the electric potential, E is the electric field strength, σ is the electrical conductivity, and A is the magnetic vector potential.
The RWLMCL physical model in figure 2 is complex. Solid components such as the shell and electrodes do not physically change during the current-limiting process, so there is little effect on the simulation. To simplify the simulation, the constructed RWLMCL simulation model is shown in figure 9.
In figure 9, the size of the fluid domain is 40 mm × 40 mm × 50 mm. The fluid domain includes the top and both sides of the wall, and the interior of the channel. The size of the wall is 40 mm × 20 mm × 40 mm, and it is located below the middle of the fluid domain. The channel inside the wall has a diameter and length of 10 mm and 20 mm respectively. The bottom of the channel is 10 mm from the bottom end of the wall. Due to the magnetic field boundary, a ballon region three times the size of the actual model is constructed in this work, with a size of 120 mm × 120 mm × 150 mm.
In order to reduce the difficulty of numerical analysis, combined with the formation mechanism of the liquid metal self-shrinkage effect, the simulation model of RWLMCL is simplified and assumed to be as follows. First, the contact between the wall and the liquid metal is not considered. The wall is considered to be smooth and there is no air in the gap. Second, the influence of temperature changes on various physical parameters during the current-limiting process is not considered, and all physical parameters are constant. Third, the fluid domain always contains only gas-liquid phases, which are both incompressible and immiscible. Fourth, the change of air pressure in the cavity during the current-limiting process is not considered.
The boundary condition settings need to consider velocity, magnetic field, and electric field, etc. For the velocity boundary, it is generally considered that the model wall is a no-slip boundary and the velocity is zero. The cathode surface is set to zero potential, and the anode current inlet is set to a uniform current density Jin.
\boldsymbol{J}_{\text {in }}=I_{\text {in }} / S_{\text {in }} | (7) |
where Iin is the current flowing into the RWLMCL, and Sin is the current inlet area. In the simulation, the current flowing through the RWLMCL is a sine current, and the current expression is Iin = Imsin(2πt/T). Since the magnetic field decays with the square of the distance from the current source, the magnetic field boundary sets the magnetic vector potential A of the outer six faces of the ballon region to zero.
For the simulation model shown in figure 9, this work uses the fluid simulation software Fluent to calculate. The liquid metal surface rises 5 mm above the channel's bottom, and the entire channel is not filled. It is assumed that the initial time of the short-circuit current is 0 ms, and the lower right corner of the wall is the coordinate origin. The liquid metal and air phases in the fluid domain are initialized, and the dynamic distribution is shown in figure 10.
To analyze the change process of the liquid metal self-shrinkage effect and arc plasma formation process, transient calculations are carried out. The gas and liquid phases distribution diagrams of the RWLMCL fluid domain obtained for Planes 1 and 2 are illustrated in figure 11.
Figure 11 shows that at 7.2 ms, liquid metal surface depressions are formed at the four corners under the current. As the current increases, the liquid metal at both ends of the channel is depressed along the inner wall of the channel, and the area and depth of the depressions continue to expand. The liquid metal height of the channel gradually rises and becomes thinner. The quick growth in the Lorentz force inside the liquid metal results from the continuous reduction of the current cross-sectional area, which accelerates the liquid metal self-shrinking process. At 13.0 ms, the depressions at the channel's bottom reach the maximum. The liquid metal is almost broken, and arcs are formed. However, due to the high viscosity of the liquid metal, a small amount of liquid metal remains at the channel's bottom.
The liquid metal self-shrinking behaviors simulated in figure 11 are in good agreement with the images in figure 8. The correctness of the mathematical model established is proved. However, all liquid metal levels in the channel rise in the simulation, while the liquid level in the channel rises locally and unevenly in the experiment. This is possible because the pressure change in the cavity during the process of limiting current is not considered in the simulation. The pressure in the cavity increases, which will affect the liquid metal in the channel in the experiment.
In the simulation, the arc starts burning at the bottom of the channel. But in the experiment, it starts burning at the left groove away from the channel, and then at the channel. This may be because the simplified model does not consider the gaps between the liquid metal and the wall surface, and the contact between the cavity wall and the liquid metal in the simulation.
Furthermore, the arc burning time of the RWLMCL is shorter in the simulation than in the experiment. This is possible because the sinusoidal current is set in the simulation, while the single-frequency oscillation current in the experiment is not standard enough.
In the experiment shown in figure 8, the phenomenon of a different depression time on both sides of the wall appears, but it does not appear in the simulation. This can be related to the smoothness of the wall and channel. In the simulation, only the case with a smooth wall is considered. When the wall surface is rough, there are gaps between the liquid metal and wall surface. According to [25], the air in the gap will accelerate the liquid metal to shrink and depress, leading to the different times to start shrinking.
In this section, we explore why the liquid metal first begins to depress at the four corners, and why the liquid metal shrinks along the inner wall of the channel. The current density, magnetic induction intensity, and Lorentz force of the liquid metal at different times will be analyzed.
At different times, the current density J distribution diagrams of the RWLMCL for Planes 1 and 2 are illustrated in figure 12.
Figure 12 shows that the current density J distribution in the fluid domain is axisymmetric, and the current density in the air domain is close to zero. The liquid metal current density in the channel is the largest, and it gradually decreases in the direction of the electrodes in the grooves. With the deepening of the depressions, the current density at the interface of the channel inner wall and air gradually increases. At 13.0 ms, the liquid metal current density in the grooves is greater than that in the channel. In addition, the liquid metal is in the critical state of break, the liquid metal cross-sectional area at the channel's bottom is the smallest, and the maximum current density is 4.03 × 108 A/m2.
The liquid metal current density JL in the cavity is:
J_{\mathrm{L}}=\boldsymbol{e}_{\mathrm{L}} \frac{\mathrm{d} i_{\mathrm{L}}}{\mathrm{d} S_{\mathrm{L}}} | (8) |
where eL is the direction of the current density JL, iL is the current flowing through the liquid metal, and SL is the current cross-sectional area.
According to equation (8), the current density is inversely proportional to the current cross-sectional area and proportional to the current. The current cross-sectional area of the liquid metal at both ends of the channel decreases sharply. As a result, the liquid metal current density at the four corners is the largest at 0 ms. The liquid metal accelerates to depress along the inner wall of the channel as the current increases, resulting in a further reduction of the current cross-sectional area in the channel. Under the combined effect of the increasing current and the decreasing current cross-sectional area, the liquid metal current density at the interface of the channel inner wall and air gradually increases. Simultaneously, the increased current density accelerates the liquid metal depression.
At different times, the magnetic induction intensity B distribution diagrams of the RWLMCL for Planes 1 and 2 are shown in figure 13.
It can be seen from figure 13 that the magnetic induction intensity B is also axisymmetric. The liquid metal magnetic induction intensity of the channel's inner wall is the largest. For the cylinder-like liquid metal in the channel, the magnetic induction intensity decreases radially from the outside to the center, and the inner center is zero. As the depression deepens and the liquid metal level rises, the position where the magnetic induction intensity is zero gradually moves up, and the magnetic induction intensity at the interface of the channel inner wall and air gradually increases. The liquid metal of the channel becomes thinner and the liquid level rises, causing the liquid metal to flow into the grooves. The height of the liquid metal in the grooves gradually increases. Therefore, the magnetic induction intensity in the grooves is greater than that in the channel. At 12.2 ms, the magnetic induction intensity at the channel's bottom inner wall reaches the maximum, which is 2.39 × 105 T.
Taking figure 11(c) as an example, for simplifying the analysis, the liquid metal path in the channel is regarded as a cylinder with a radius of a, and the current is uniformly distributed. The liquid metal magnetic induction intensity model on the axis is shown in figure 14.
For Plane C and Plane F, according to the Ampere circuital theorem, inside the liquid metal cylinder, the following formulas can be obtained:
\left\{\begin{array}{l} \xi_{\mathrm{C}}=I_{\mathrm{C}} /\left(\pi a^2\right) \\ \xi_{\mathrm{F}}=I_r /\left(\pi r^2\right) \\ \xi_{\mathrm{C}}=\xi_{\mathrm{F}} \\ \oint_r \boldsymbol{B}(r) \mathrm{d} \boldsymbol{l}_r=\mu_{\mathrm{C}} I_r \end{array} .\right. | (9) |
From equation (9), the magnetic induction intensity distributions inside the liquid metal in the channel are deduced as:
\boldsymbol{B}(r)=\frac{\mu_{\mathrm{C}} I_{\mathrm{C}}}{2 \pi a^2} r(r<a) . | (10) |
For Plane D, according to the Ampere circuital theorem, the magnetic induction intensity outside the liquid metal in the channel is deduced as:
\boldsymbol{B}(r)=\frac{\mu_{\mathrm{C}} I_{\mathrm{C}}}{2 \pi r}(r>a) | (11) |
where ξC and ξF are the current surface densities of Plane C and Plane F respectively. μC is the vacuum permeability, r is the distance between the calculation point and the central axis of the liquid metal cylinder, IC is the current flowing through the liquid metal of the channel, and Ir is the current flowing through any curved surface inside the liquid metal.
Inside the liquid metal path of the channel, it can be known from equation (10) that the magnetic induction intensity is positively correlated with the current IC and the distance r. The liquid metal current density is the largest at the bottom of the inner wall of the channel, resulting in a large current here. Furthermore, the distance from the axis of the liquid metal cylinder is the greatest here. Affected by the current and distance, the maximum magnetic induction intensity appears at the bottom of the inner wall of the channel. Moreover, inside the liquid metal, the closer to the central axis of the liquid metal cylinder, the smaller the magnetic induction intensity B. At the axial center position (r = 0 m), the magnetic induction intensity is zero. As time increases, the liquid metal level in the channel rises, leading to the central position where the magnetic induction intensity is zero also rising.
Outside the liquid metal path, the magnetic induction intensity is inversely proportional to the distance r according to equation (11). The farther away from the central axis of the liquid metal cylinder, the smaller the magnetic induction intensity.
At different times, the Lorentz force F distribution diagrams of the RWLMCL simulation model for Planes 1 and 2 are shown in figure 15.
Figure 15 shows that similar to the magnetic induction intensity B, the Lorentz force F in the fluid domain of the RWLMCL also presents an axisymmetric distribution. The liquid metal Lorentz force on the inner wall of the channel is the largest. The Lorentz force of the liquid metal path decreases from the outside to the inside, and the middle part is zero. As the liquid level rises, the position where the Lorentz force is zero gradually moves upward. With the deepening of the depression, the Lorentz force at the interface of the channel inner wall and air gradually increases. The height of the liquid metal level in the grooves increases, resulting in a greater Lorentz force in the grooves than in the channel. At 12.2 ms, the Lorentz force at the channel's bottom reaches the maximum of 9.35 × 1013 N.
The interplay between current and magnetic induction intensity produces the Lorentz force F. The Lorentz force produces a radial pressure gradient, which makes the liquid surface depress. Furthermore, the Lorentz force is the main factor leading to the liquid metal self-shrinkage effect.
In summary, because of the special structure of the RWLMCL, the liquid metal current density at both ends of the channel will change abruptly. The liquid metal Lorentz force at the four corners changes the most, so the pressure gradient formed is the largest in the whole region. Moreover, the viscosity coefficient of the liquid metal is large, and it cannot be closely attached to the cavity. Therefore, under the combined effect of Lorentz force and airflow, the gap at the inner wall connection at both ends of the channel will appear first. In addition, the shrinkage of liquid metal reduces the cross-sectional area of the depressions, making the current density and magnetic induction intensity distribution of the liquid metal in the depressions more uneven. As the current increases, the liquid metal Lorentz force in the depressions further increases, so that the depressions of the surface continue to deepen and expand. Until the depressions reach the channel's bottom, the liquid metal path is broken and the arcs are formed. Concurrently, the level of liquid metal in the channel rises due to squeeze, which causes the level of the liquid metal in the grooves to increase, forming huge depressions.
To further explore the formation mechanism of the gas-liquid surface in the liquid metal self-shrinking process, this work simulates the velocity field distribution of the RWLMCL simulation model at 0 ms, as shown in figure 16.
At the initial moment, the liquid metal current density is the largest on both sides of the inner wall of the channel, where the magnetic induction intensity and Lorentz force are the largest, resulting in the shrinkage here first. Figure 16(a) shows the velocity field starting from the edges of the inner walls on both sides of the channel and flowing to the grooves. This velocity field causes the liquid metal in the channel to flow toward the grooves, and the liquid metal level in the groove rises. This is also the reason for the formation of huge depressions in the grooves of the experiment shown in figure 8, which expand toward the electrodes.
Meanwhile, as shown in figure 1(b), two annular velocity fields are formed. The velocity in liquid metal is higher than that of air. The gas-liquid two-phase flow will separate due to the slip velocity under the action of the magnetic field.
In addition, we can see the reason for the formation of bubbles along the bottom of the channel wall. The bubbles start from the liquid metal at the edges of the inner walls on both sides of the channel to the bottom. Then, the liquid metal in the center of the channel is extruded and bulged towards the Z-axis direction. Because the liquid metal shrinks faster, the compressed air in turn continues to compress the liquid metal on the edge of the inner wall of the channel, forming vortexes.
The key to the early current limiting of the RWLMCL is that when the liquid metal in the channel shrinks and depresses, the current begins to transfer from the liquid metal to the wall resistance. In this work, the current-carrying capacity value is defined as:
\gamma=J_{\mathrm{a}} / J_{\mathrm{m}} \times 100 \% | (12) |
where γ is the current-carrying capacity value, Jm is the peak current density, and Ja is the current density value.
In the liquid metal self-shrinking process, the short-circuit current transfer of the RWLMCL from the liquid metal path to the wall resistance path is shown in figure 17. For simplification, assuming that dY is infinitely small, the current density at Y = 15-25 mm of Line 1 can be regarded as the projection of the liquid metal current density on the inner wall of the channel to the Y axis.
This work uses the simulation of figure 11, intercepts the current density on Line 1, and calculates current-carrying capacity values at different times, as shown in figure 18.
At 0 ms, the current-carrying capacity value of the liquid metal is the largest. At 7.2 ms, the liquid metal gradually shrinks and depresses in the channel, and the current starts to transfer, resulting in an increase in the current-carrying capacity value of Y = 0-6, 34-40 mm on Line 1. At this time, the wall resistance is connected to the loop, so that the current-limiting resistance of the RWLMCL increases, and the RWLMCL starts to limit current. With the further increase of the current and the liquid metal depressions in the channel, the current-carrying capacity value and current-carrying distance of the liquid metal in the channel gradually decrease. The current-carrying capacity value of the resistive wall at the left and right ends gradually increases, and the maximum current-carrying capacity value gradually moves toward the channel. The liquid metal is in the critical state of break at 13.0 ms. Simultaneously, the short-circuit current mainly passes through the wall resistance path. At Y = 36.43 mm, the current-carrying capacity value is the largest. At Y = 20.24 mm (the channel's bottom), the current-carrying capacity value is only 44.85%.
Starting from the liquid metal depressions of the RWLMCL, the short-circuit current is transferred from the liquid metal path to the wall resistive path. Compared with the existing IWLMCL [13-18, 23-25], the current-limiting time of the RWLMCL starts earlier.
In the process of short-circuit current transfer, the maximum current density of the resistive wall moves from the distal end of the wall to the direction of the channel with the expansion of the liquid metal depression. This may be the main reason for the different arc positions in the experiment shown in figure 8.
In summary, the liquid metal starts to shrink and depress under the current, and the wall resistance is connected to the loop. The current starts to transfer from the liquid metal path to the resistive wall path, which begins to limit the short-circuit current. With the expansion of the liquid metal depressions in the channel, the current-carrying capacity value of the resistive wall gradually increases, and the maximum current-carrying capacity value gradually moves towards the direction of the channel at the distal end of the wall. The RWLMCL can advance the starting current-limiting time.
Under the action of different currents, the simulating and experimental results of the pre-liquid metal shrinking time TN and the liquid metal self-shrinking time TS of the RWLMCL are shown in figure 19. The TN and TS of the RWLMCL decrease as the current increases. The greater the current, the easier and faster the liquid metal shrinks. The simulations are consistent with the experimental results. This demonstrates that the simulation method adopted can be used to explore the characteristics of liquid metal.
When the current values are 1.285 kA and 1.797 kA, the TN and TS obtained from the experiments are larger than the simulated ones. This phenomenon may be related to the roughness within the channel [25]. The air in the gap can advance and accelerate the liquid metal self-shrinking process. In the simulation, it is assumed that the wall is smooth and there is no gap between the liquid metal and wall. When the current is small, the air in the gap has a greater influence in the liquid metal self-shrinking process.
In the present work, we have designed a new RWLMCL. The RWLMCL can effectively advance the starting current-limiting time of the existing LMCL. Furthermore, the dynamic behaviors, arc plasma formation process, and current transfer law of the liquid metal self-shrinkage are investigated by experiments and simulations.
In the liquid metal self-shrinking process, the greater the current, the easier and faster the liquid metal shrinks. In addition, the greater the current, the faster the current transfer from the liquid metal path to the resistive wall path.
The liquid metal dynamic behaviors under the short-circuit current can be divided into four stages, which are as tightly bound to the resistance and voltage of the RWLMCL. It is proved that the liquid metal self-shrinkage effect is still effective for the RWLMCL.
We perform simulations by the FEM to study the generation mechanism of the liquid metal self-shrinkage effect and the dynamic change of the current transfer. Because of the special structure of the RWLMCL, the liquid metal current density at both ends of the channel will suddenly change. The four corners where the two ends of the channel are connected with the inner wall have the largest variation in the Lorentz force, which causes the four corners to depress first. With the increase of current, the cross-sectional area of the liquid metal depressions decreases, and the Lorentz force further increases, so that the depressions continue to deepen and expand. Until the depressions reach the channel's bottom, the liquid metal path is broken and arc plasma is formed.
Starting from the liquid metal depressions, the short-circuit current is transferred from the liquid metal path to the wall resistance path, and the RWLMCL begins to limit current. With the expansion of the liquid metal depressions in the channel, the current shared by the wall resistance path increases, and the maximum current-carrying capacity value gradually moves from the distal end of the wall to the direction of the channel. Due to the resistive wall structure of the RWLMCL, the starting current-limiting time is advanced.
The simulations are consistent with the experimental results, which proves the rationality of the theoretical model. The computer simulation method adopted in this work can be used to study the arc plasma formation process.
This work was supported by National Natural Science Foundation of China (No. 52177131) and the Interdisciplinary Program of Wuhan National High Magnetic Field Center (No. WHMFC202130), Huazhong University of Science and Technology.
[1] |
Jiang Y Z et al 2021 Plasma Sci. Technol.
23 025505 doi: 10.1088/2058-6272/abd5a1
|
[2] |
Ju X B et al 2016 Plasma Sci. Technol.
18 531 doi: 10.1088/1009-0630/18/5/15
|
[3] |
Chen Z Q et al 2021 High Volt.
6 328 doi: 10.1049/hve2.12026
|
[4] |
Zhang H et al 2021 IEEE Access
9 17222 doi: 10.1109/ACCESS.2021.3053347
|
[5] |
Tang S et al 2020 CSEE J. Power Energy Syst.
6 298 doi: 10.17775/CSEEJPES.2019.02800
|
[6] |
Li J J et al 2021 2020 29th Int. Symp. on Discharge and Electrical Insulation in Vacuum (ISDEIV) (Padova: Consorzio RFX)
|
[7] |
Mohsenzade S, Zarghani M and Kaboli S 2021 IEEE J. Emerg. Sel. Top. Power Electron.
9 6300 doi: 10.1109/JESTPE.2021.3061093
|
[8] |
Kraemer H et al 2022 IEEE Trans. Power Deliv.
37 612 doi: 10.1109/TPWRD.2021.3066845
|
[9] |
Van den Bossche A, Stoyanov R S and Valchev V C 2018 Int. J. Electron.
105 1615 doi: 10.1080/00207217.2018.1477194
|
[10] |
Li H X et al 2021 IEEE Trans. Appl. Supercond.
31 5601305 doi: 10.1109/TASC.2021.3064515
|
[11] |
Yuan J X et al 2020 IEEE Trans. Power Deliv.
35 1707 doi: 10.1109/TPWRD.2019.2950470
|
[12] |
Li J J et al 2022 Plasma Sci. Technol.
24 085503 doi: 10.1088/2058-6272/ac64f0
|
[13] |
Liu Y Y et al 2014 IEEE Trans. Compon. Pack. Manuf. Technol.
4 209 doi: 10.1109/TCPMT.2013.2292581
|
[14] |
Niu C P et al 2021 IEEE Trans. Power Deliv.
36 3619 doi: 10.1109/TPWRD.2020.3045559
|
[15] |
Rong M Z et al 2010 IEEE Trans. Plasma Sci.
38 2056 doi: 10.1109/TPS.2010.2050704
|
[16] |
Liu Y Y et al 2013 Plasma Sci. Technol.
15 1006 doi: 10.1088/1009-0630/15/10/09
|
[17] |
Wu H R et al 2009 IEEE Trans. Compon. Packaging Technol.
32 572 doi: 10.1109/TCAPT.2009.2024157
|
[18] |
Zienicke E et al 2008 J. Therm. Sci.
17 261 doi: 10.1007/s11630-008-0261-0
|
[19] |
Kang W S, Xu Z Y and Pan C J 2006 Fusion Eng. Des.
81 1019 doi: 10.1016/j.fusengdes.2005.07.029
|
[20] |
Li J J et al 2022 IEEE Trans. Plasma Sci.
50 2745 doi: 10.1109/TPS.2022.3192564
|
[21] |
Xiao Y Q and Li J H 2021 IEEE Trans. Compon. Pack. Manuf. Technol.
11 153 doi: 10.1109/TCPMT.2020.3041258
|
[22] |
Fang J H et al 2019 Vacuum
167 459 doi: 10.1016/j.vacuum.2019.07.001
|
[23] |
Xiao Y et al 2021 IEEE J. Emerg. Sel. Top. Power Electron.
9 5521 doi: 10.1109/JESTPE.2021.3056085
|
[24] |
Wang B B et al 2022 IEEE Trans. Ind. Electron.
69 5050 doi: 10.1109/TIE.2021.3078401
|
[25] |
He H L2 et al 2015 3rd Int. Conf. on Electric Power Equipment-Switching Technology (ICEPE-ST) (Busan, Korea)
|
[1] | Guoqiang Gao, Aozheng Wang, Yaguang Ma, Bingyan You, Wei Peng, Zefeng Yang, Guangning Wu. Analysis of shrinkage characteristics of GaInSn liquid metal in pre-arc process[J]. Plasma Science and Technology. DOI: 10.1088/2058-6272/adb36b |
[2] | Jinjin LI, Xiongying DUAN, Weiying XIE, Zhihui HUANG, Minfu LIAO, Dequan WANG, Xiaotao HAN. A novel fault current limiter topology design based on liquid metal current limiter[J]. Plasma Science and Technology, 2022, 24(8): 085503. DOI: 10.1088/2058-6272/ac64f0 |
[3] | A K MANDAL, R K DISHWAR, O P SINHA. Behavior of an indigenously fabricated transferred arc plasma furnace for smelting studies[J]. Plasma Science and Technology, 2018, 20(3): 35506-035506. DOI: 10.1088/2058-6272/aa9cde |
[4] | Hao ZHANG (张浩), Fengsen ZHU (朱凤森), Xiaodong LI (李晓东), Changming DU (杜长明). Dynamic behavior of a rotating gliding arc plasma in nitrogen: effects of gas flow rate and operating current[J]. Plasma Science and Technology, 2017, 19(4): 45401-045401. DOI: 10.1088/2058-6272/aa57f3 |
[5] | JU Xingbao (琚兴宝), SUN Haishun (孙海顺), YANG Zhuo (杨倬), ZHANG Junmin (张俊民). Investigation on the Arc Ignition Characteristics and Energy Absorption of Liquid Metal Current Limiter Based on Self-Pinch Effect[J]. Plasma Science and Technology, 2016, 18(5): 531-537. DOI: 10.1088/1009-0630/18/5/15 |
[6] | M’hammed ABBAOUI, Andr′e LEFORT, Erwann CARVOU, Damien SALLAIS, James Brian Alexander MITCHELL, Noureddine BEN JEMAA. Formation of a 40 A DC Current Arc During the Opening of Silver Contacts[J]. Plasma Science and Technology, 2014, 16(5): 471-478. DOI: 10.1088/1009-0630/16/5/06 |
[7] | LIU Yiying (刘懿莹), WU Yi (吴翊), RONG Mingzhe (荣命哲), HE Hailong (何海龙). Simulation of the Effect of a Metal Vapor Arc on Electrode Erosion in Liquid Metal Current Limiting Device[J]. Plasma Science and Technology, 2013, 15(10): 1006-1011. DOI: 10.1088/1009-0630/15/10/09 |
[8] | YANG Fei (杨飞), RONG Mingzhe (荣命哲), WU Yi (吴翊), SUN Hao (孙昊), MA Ruiguang (马瑞光), NIU Chunping (纽春萍). Numerical Simulation of the Eddy Current Effects in the Arc Splitting Process[J]. Plasma Science and Technology, 2012, 14(11): 974-979. DOI: 10.1088/1009-0630/14/11/05 |
[9] | HU Hui (胡辉), CHEN Weipeng(陈卫鹏), Zhang Jin-li (张锦丽), LU Xi (陆僖), HE Junjia(何俊佳). Influence of plasma temperature on the concentration of NO produced by pulsed arc discharge[J]. Plasma Science and Technology, 2012, 14(3): 257-262. DOI: 10.1088/1009-0630/14/3/13 |
[10] | YANG Fei(杨飞), MA Ruiguang ( 马瑞光), WU Yi( 吴翊), SUN Hao( 孙昊), NIU Chunping( 纽春萍), RONG Mingzhe(荣命哲). Numerical study on arc plasma behavior during arc commutation process in direct current circuit breaker[J]. Plasma Science and Technology, 2012, 14(2): 167-171. DOI: 10.1088/1009-0630/14/2/16 |