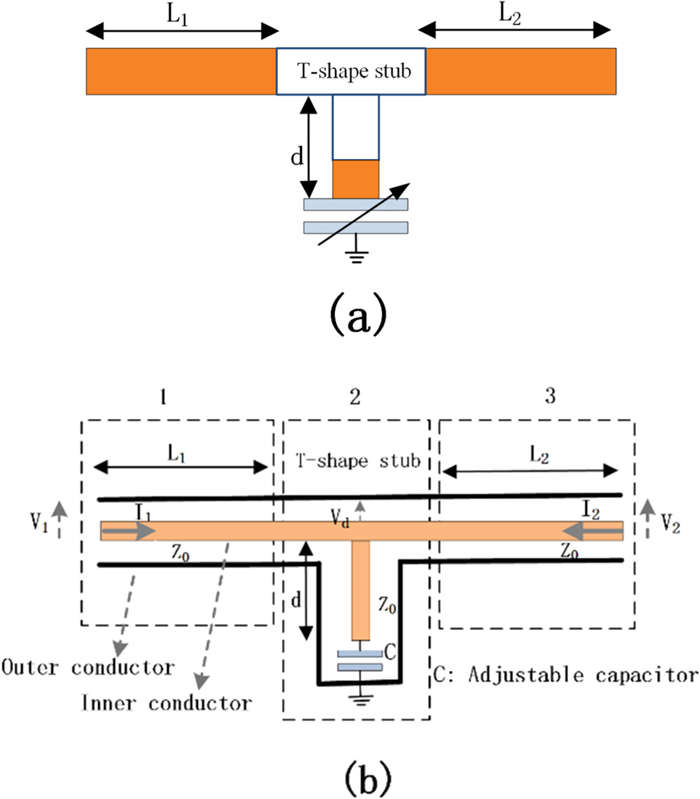
Citation: | Xinghua ZHANG, Zhenhua ZHANG, Shaoxia JIA, Ting JIN, Jinghua YANG, Long LI, Fangfang LIU, Yong CAI, Jian CAI. Influence of anode temperature on ignition performance of the IRIT4-2D iodine-fueled radio frequency ion thruster[J]. Plasma Science and Technology, 2022, 24(1): 015506. DOI: 10.1088/2058-6272/ac34e6 |
This paper reports the ignition performance of the iodine-fueled radio frequency (RF) ion thruster (IRIT) at different anode temperatures (
The Ion Cyclotron Radio Frequency (ICRF) heating antenna adopts the design of multi-radiation straps, which results in a strong power coupling between the straps [1–7]. To restrain such power coupling, variable decouplers have been developed in the world tokamak machines [8–13], and a decoupler based on the T-shape shorted stub was used on EAST [14–17]. However, during the experiment, it was discovered that the short-circuit type with piston had shortcomings such as long size, difficult to adjust electrical length, poor contact of the short-circuit finger which leads to easy burning out etc. Therefore, it is planned to adopt a terminal-loaded tunable capacitor solution to shorten the length of the stub and facilitate adjustment, and the design of none short-circuit contact finger can avoid the problem of poor contact and burnout.
The design of a decoupler with terminal-loaded tunable capacitors should meet the requirements of mutual coupling suppression on EAST antennas, which works under the pressurized atmosphere of the transmission line. By changing the capacitance value, the imaginary part of non-diagonal term of Y parameter of the decoupler is supposed to achieve
Three significant aspects are elaborated: T-shape stub with tunable capacitor design, simulation analysis and physical test. Section 2 introduces the theoretical derivation of the admittance matrix of the decoupling device, the relationship among the capacitor voltage and the capacitance value, and so on. Section 3 builds a simulation model based on the design parameters and discusses the simulation results. Section 4 shows the test results of the developed system without plasma. Finally, there is a conclusion of the whole design and tests.
Besides the tunable admittance parameters of decoupler, the withstand voltage of the capacitor is the most significant consideration for decoupler to work under high power. Therefore, based on the microwave engineering theory, the calculation model of capacitor loaded decoupler is constructed, and the capacitor working voltage and other performance parameters are deduced theoretically, which will be the foundation of the parameter's selection of decoupler.
Based on the original design [16], only the change of the introduced part of capacitive loading needs to be considered. Two-port network design with T-shape structure is applied on the decoupler. One of the ports is loaded with a terminal short-circuit tunable vacuum capacitor, as shown in figure 1(a). The T-shape stub loaded with tunable capacitor circuit used in decoupler can be equivalent to a two-port network cascaded by three parts, as shown in figure 1(b). The cascaded three parts are transmission line
A1=[cosβlj×sinβlY0j×sinβl×Y0cosβl], | (1) |
where,
The ABCD matrix of part 2, i.e. T-shape stub, is:
Yd=1Zd=-j×Y0cot(βd-θ), | (2) |
θ=tan-1(1ωCZ0). | (3) |
Among them,
According to microwave transmission theory, the ABCD matrix of decoupler can be expressed as:
YT=[YT11YT12YT21YT22], | (4) |
where
YT11=YT22=j×Y0×Yd×sinβl×cosβl-Y02×(sinβl)2+Y02×(cosβl)2(-Yd)×(sinβl)2+j×2×Y0×sinβl×cosβlYT12=YT21=-Y02(-Yd)×(sinβl)2+j×2×Y0×sinβl×cosβl. | (5) |
Therefore, the diagonal admittance of decoupler is determined by the equivalent phase of the terminal-loaded capacitor, which is the foundation for the decoupler to perform the mutual coupling suppression.
When the capacitor is loaded at the short-circuit end of the T-shape stub, the withstand voltage and the tunable capacitance value need to be considered for high-power operation and antenna decoupling. The voltage at both ends of decoupler is:
Vd=V1×cosβl-j×sinβlY0×(V1×YT11+V2×YT12). | (6) |
T-shape stub with terminal loaded capacitor can be expressed as figure 2,
Vc=Vde-jβd1+ΓL1+Γd, | (7) |
where,
Based on equations (4) and (7), the known parameters and conditions can be brought in to design the withstand voltage and capacitance value of the tunable capacitor. According to the design requirements and test conditions of ICRF antenna, the parameters already known are as follows:
(1) Operating frequency
(2) Design requirements according to experimental statistics [16]:
(3) Length selection of T-shape stub:
(4) Port voltage at the hard-fed connection between T-shape stub and ICRF antenna:
(5) According to tunable capacitor selection manual [19], the operating voltage amplitude of the capacitor:
Put condition (3) into equation (4) to derive:
YT12=Y20Yd=j×Y0tan(βd-θ). | (8) |
According to equation (7), it can be deduced that:
Vc=Vde-jβd1-jcot(βd-θ)1+jωCZ0. | (9) |
To satisfy design requirement (2), the range of
-0.025≤tan(βd-θ)≤0.025. | (10) |
Taking three significant digits after the decimal point,
According to known condition (5), the range of capacitor C is:
-0.025≤βd-θ≤0.025. | (21) |
According to equation (9), the voltage of the tunable capacitor can be calculated under different values of
However, when the capacitance value
According to these parameters, the capacitor CKTB1000/35/25 produced by Kunshan Guoli Electronic Technology Co., which can achieve the tunable capacitance of
In order to make
Considering the achievability of the structure of d-length, theoretical calculation parameters adopted finally are:
Compared with T-shape stub, the difference of decoupler is
In EAST 2021 experiments, the decoupler with this new design is adopted for two straps ICRF antenna at port N. The scattering parameter
During the design of capacitor-loaded decoupler, those factors, such as the adjustable range of parallel admittance, the compactness and feasibility of the structure, and the voltage and adjustable range of the capacitor, have been taken into considerations. The theoretical analysis carefully elaborates the capacitor withstand voltage, which is the most significant aspect for high power operation of decoupler, and the detailed analytical equations and criteria for design are given. The test results show that the imaginary part of
The financial support from National Natural Science Foundation of China (No. 11805265) and Key Laboratory of Micro-Satellites, Chinese Academy of Sciences (No. KFKT201903) is gratefully acknowledged.
[1] |
Dressler R A, Chiu Y H and Levandier D J 2000 Propellant alternatives for ion and hall effect thrusters Proc. of the 38th Aerospace Sciences Meeting and Exhibit (Reno, NV: AIAA)
|
[2] |
Tverdokhlebov O S and Semenkin A V 2001 Iodine propellant for electric propulsion-to be or not to be Proc. of the 37th Joint Propulsion Conf. and Exhibit (Salt Lake City, UT, USA: AIAA)
|
[3] |
Szabo J et al 2012 J. Propul. Power 28 848 doi: 10.2514/1.B34291
|
[4] |
Szabo J et al 2015 IEEE Trans. Plasma Sci. 43 141 doi: 10.1109/TPS.2014.2367417
|
[5] |
Szabo J et al 2017 Characterization of a one hundred watt long lifetime hall effect thruster for small spacecraft AIAA Propulsion and Energy Forum, 53rd AIAA/SAE/ASEE Joint Propulsion Conf. (Atlanta, GA)
|
[6] |
Kamhawi H et al 2016 Overview of iodine propellant hall thruster development activities at NASA Glenn Research Center American Institute of Aeronautics and Astronautics, 52nd AIAA/SAE/ASEE Joint Propulsion Conf.
|
[7] |
Smith T D et al 2016 Overview of NASA iodine hall thruster propulsion system development In: https://ntrs.nasa.gov/search.jsp?R=20160006296
|
[8] |
Liu H et al 2019 J. Propul. Technol. 40 12 (in Chinese)
|
[9] |
Tsay M, Frongillo J and Hohman K 2015 Iodine-fueled Mini RF ion thruster for CubeSat applications Proc. of the 34th Int. Electric Propulsion Conf. and 6th Nano-satellite Symp (Hyogo-Kobe, Japan: IEPC)
|
[10] |
Tsay M et al 2017 Integrated testing of iodine BIT-3 RF ion propulsion system for 6U CubeSat applications The 35th Int. Electric Propulsion Conf. (USA: Georgia Institute of Technology)
|
[11] |
Holste K et al 2018 Eur. Phys. J. D 72 9 doi: 10.1140/epjd/e2017-80498-5
|
[12] |
Martínez J M, Rafalskyi D and Aanesland A 2019 Development and testing of the NPT30-I2 iodine ion thruster 36th Int. Electric Propulsion Conf. (Vienna, Austria: University of Vienna)
|
[13] |
Yang J H et al 2020 Plasma Sci. Technol. 9 094006 doi: 10.1088/2058-6272/ab891d
|
[14] |
Manente M et al 2019 REGULUS: iodine fed plasma propulsion system for small satellites 36th Int. Electric Propulsion Conf. (Vienna, Austria: University of Vienna) IEPC-2019-417
|
[15] |
Manente M et al 2019 REGULUS: know-how acquired on iodine propellant 36th Int. Electric Propulsion Conf. (Vienna, Austria: University of Vienna) pp 1–10 IEPC- 2019-419
|
[16] |
Polzin K A 2018 Iodine satellite propellant feed clog-clearing demonstration testing In: NASA/TM—2018–220128.1-28
|
[17] |
Samples S A, Dankanich J W and Polzin K A 2015 Iodine hall thruster feed system design, development and testing 51st AIAA/SAE/ASEE Joint Propulsion Conf. (Orlando, FL: AIAA)
|
[18] |
Paganucci F et al 2019 I2HET: development of an iodine-fed hall effect thruster 36th Int. Electric Propulsion Conf. (Vienna, Austria: University of Vienna)
|
[19] |
Li L et al 2020 Development of IRIT3.5-2D iodine-fueled ion electric propulsion system 16th China Electric Propulsion Symp. (Beijing, China) (in Chinese)
|
[1] | Jinghua YANG (杨景华), Shaoxia JIA (贾少霞), Zhenhua ZHANG (张振华), Xinghua ZHANG (张兴华), Ting JIN (金婷), Long LI (李龙), Yong CAI (蔡勇), Jian CAI (蔡建). Performance of a 4 cm iodine-fueled radio frequency ion thruster[J]. Plasma Science and Technology, 2020, 22(9): 94006-094006. DOI: 10.1088/2058-6272/ab891d |
[2] | Xiuquan CAO (曹修全), Deping YU (余德平), Yong XIANG (向勇), Chao LI (李超), Hui JIANG (江汇), Jin YAO (姚进). Study on the ignition process of a segmented plasma torch[J]. Plasma Science and Technology, 2017, 19(7): 75404-075404. DOI: 10.1088/2058-6272/aa62f9 |
[3] | A F POPOVICH, V G RALCHENKO, V K BALLA, A K MALLIK, A A KHOMICH, A P BOLSHAKOV, D N SOVYK, E E ASHKINAZI, V Yu YUROV. Growth of 4″ diameter polycrystalline diamond wafers with high thermal conductivity by 915 MHz microwave plasma chemical vapor deposition[J]. Plasma Science and Technology, 2017, 19(3): 35503-035503. DOI: 10.1088/2058-6272/19/3/035503 |
[4] | DONG Yunsong (董云松), YANG Jiamin (杨家敏), SONG Tianming (宋天明), ZHU Tuo (朱托), HUANG Chengwu (黄成武). Radiation Hydrodynamic Simulations in the Planar Scheme for the Fundamental Studies of Shock Ignition[J]. Plasma Science and Technology, 2016, 18(4): 376-381. DOI: 10.1088/1009-0630/18/4/08 |
[5] | Hadar MANIS-LEVY, Tsachi LIVNEH, Ido ZUKERMAN, Moshe H. MINTZ, Avi RAVEH. Effect of Radio-Frequency and Low-Frequency Bias Voltage on the Formation of Amorphous Carbon Films Deposited by Plasma Enhanced Chemical Vapor Deposition[J]. Plasma Science and Technology, 2014, 16(10): 954-959. DOI: 10.1088/1009-0630/16/10/09 |
[6] | WU Maoshui(吴茂水), XU Yu(徐雨), DAI Linjun(戴林君), WANG Tiantian(王恬恬), LI Xue(李雪), WANG Dexin(王德信), GUO Ying(郭颖), DING Ke(丁可), HUANG Xiaojiang(黄晓江), SHI Jianjun(石建军), ZHANG Jing(张菁). The Gas Nucleation Process Study of Anatase TiO 2 in Atmospheric Non-Thermal Plasma Enhanced Chemical Vapor Deposition[J]. Plasma Science and Technology, 2014, 16(1): 32-36. DOI: 10.1088/1009-0630/16/1/07 |
[7] | MIAO Chunguang (苗春光), WANG Xiangqin (王相勤). Mass Deposition, Etching and Sputtering Effects of Low-Energy N + Ion Irradiation on Solid Fly Ash[J]. Plasma Science and Technology, 2013, 15(12): 1232-1236. DOI: 10.1088/1009-0630/15/12/13 |
[8] | YAN Ying (燕颖), CAI Kaiyong (蔡开勇), YANG Weihu (杨维虎), LIU Peng (刘鹏). Surface Modification of NiTi Alloy via Cathodic Plasma Electrolytic Deposition and its Effect on Ni Ion Release and Osteoblast Behaviors[J]. Plasma Science and Technology, 2013, 15(7): 648-653. DOI: 10.1088/1009-0630/15/7/09 |
[9] | M. MAHDAVI, A. GHOLAMI. Ignition Conditions for Simulated Fuel Pellets in Degenerate Plasma[J]. Plasma Science and Technology, 2013, 15(4): 323-328. DOI: 10.1088/1009-0630/15/4/04 |
[10] | CHEN Ju (陈聚), YAN Rong (鄢容), CHEN Junling (陈俊凌). Influence of Erosion and Deposition on Metallic First Mirror in HT-7 Tokamak[J]. Plasma Science and Technology, 2012, 14(8): 708-711. DOI: 10.1088/1009-0630/14/8/05 |