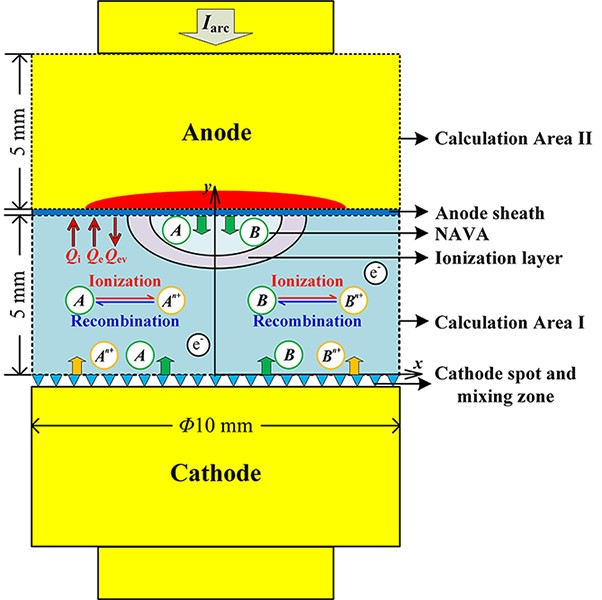
Citation: | Ze YANG, Dongsheng CAI, Qi HUANG, Lijun WANG. Effect of contact materials on the transient characteristics of vacuum arc plasma and anode erosion[J]. Plasma Science and Technology, 2024, 26(11): 115505. DOI: 10.1088/2058-6272/ad70df |
In this study, the mechanisms of the anode phenomena and anode erosion with various contact materials were investigated. Arc parameters were calculated, and the anode temperature was predicted with a transient self-consistent model. The simulation results predicted a constricted arc column and obvious anode phenomena in Cu–Cr alloy contacts than in W–Cu alloy contacts. This observation could be the reason for the concentrated anode erosion in Cu–Cr alloys. For the contacts made by pure tungsten (W) and W–Cu alloy, the anode temperature increased rapidly because of the low specific heat of W. However, the maximum energy flux from the arc column to the anode surface was lower than in other cases. The simulation results were compared with experimental results.
A vacuum interrupter is a high-voltage electrical device [1–2]. Many experimental studies on contact materials have focused on improving the capacity of vacuum interrupters [3–7]. Cu–Cr alloy is the most widely used material in commercial contacts because of its outstanding breaking capacity [3]. CuCr25 and CuCr30 are the best materials for vacuum interrupters [3, 8]. Furthermore, W–Cu alloy is commonly used because of the anti-welding ability of W. However, this factor depends on the manufacturing technique [3, 9]. Among these studies, the erosion of contacts caused by the vacuum arc has attracted considerable research attention.
In high-current vacuum interrupters, the energy flux from the arc column to the anode can heat the anode surface to a high temperature [10–12]. When the anode temperature is sufficiently high, the anode can be melted and even evaporated, forming the anode vapor emission into the arc column [13–16].
The anode phenomena have been studied with various contact materials. Kong et al [17] investigated the threshold current with which the active anode mode occurred with contacts made by Cu–Cr alloy and pure Cu. With the increase in Cr content in the contacts, the threshold current decreased. Khakpour et al [18–20] studied the anode phenomena for optical diagnostic techniques using CuCr25 contacts and studied the species density and plasma temperature. Lin et al [3] analyzed the arc characteristics and contact erosion with contacts made by Cu–Cr and W–Cu alloys. By comparison, the W–Cu alloy had worse toughness than that of the Cu–Cr alloy. The cathode spots on the contact made by W–Cu alloy moved slower, which is not beneficial to the arc diffusion process.
The anode phenomena were determined by the interaction between the anode vapor and arc column [21–23]. To understand the effect of electrode materials on the anode phenomena, relevant numerical research is necessary. Wang et al [24] established a multi-component magneto-hydro-dynamic (MHD) model to analyze the arc characteristics with contacts made by Cu–Cr and W–Cu alloys without considering anode phenomena. Huang et al [25] calculated the anode temperature distributions with various contact materials. However, the model was not coupled with the vacuum arc. Shmelev et al [26] and our group [27, 28] developed a self-consistent model to analyze the transient arc characteristics and anode temperature with contacts by the Cu–Cr alloy. However, limited numerical discussion and theoretical analyses have been conducted on the effect of electrode materials on the anode phenomena.
In this study, a self-consistent model was used considering the interaction among anode vapor, arc column, and the anode. Based on the previous model [27], the anode phenomena were analyzed with contacts made by the Cu–Cr alloy, W–Cu alloy, pure Cu, and pure W. Anode erosion was discussed with various contact materials. Simulation and relevant experimental results were compared to explain the experimental phenomena.
Figure 1 displays the physical model of the simulation. The contact diameter was 10 mm, and the gap length was 5 mm. Indexes A and B represent various materials according to the contact materials. In calculation area I, the vacuum arc parameters were calculated by the multi-component MHD model considering the anode vapor. Various components including ions, atoms, and electrons were considered. Calculation area II corresponds to the anode area, in which the anode temperature is calculated considering the energy flux from the vacuum arc and the energy loss by evaporation. During the initial stage of arcing, the anode was inactive and the cathode was the only source of the plasma. In this case, ions were emitted from the cathode and the erosion of atom evaporation was assumed to be 1/10 of the ion erosion [29]. When the arc current was sufficiently high, the anode could be heated to a sufficiently high temperature, leading to considerable anode evaporation into the arc column. Therefore, on the anode side, atoms were generated due to the anode evaporation, forming a neutral atom vapor area (NAVA) in front of the anode. Anode vapor was ionized near the ionization layer. In this study, the peak arc current Iarc was set to be 2 kA for a frequency of 50 Hz. In this case, the anode surface deformation was ignored because the arc current density was not too high [30]. The simulation covers the arc development from 1 to 9 ms with a time step of 0.05 ms. The calculation scheme can be found in a previous study [27].
In this study, various contact materials, including pure Cu, CuCr25, CuCr50, W, WCu20, and WCu30, were considered. Table 1 lists the consideration of various ion species for different contact materials so that the average charge number at the cathode side was 1.85, 2, and 3 for Cu, Cr, and W, respectively [31–32]. For example, in the simulation with WCu20 contact, seven ion species (Cu1+, Cu2+, Cu3+, W1+, W2+, W3+, and W4+) were considered in calculation area I by ionization and recombination process. At the cathode side, only Cu1+, Cu2+, and W3+ were emitted with a proportion of 0.03:0.17:0.8 according to the average charge number given previously and their mass fraction in the contact. Contact materials were divided into two groups (table 1) for analysis.
Group | Contact material | Consideration of ion species in calculation area I | Ion species emitted from the cathode |
Group I | Pure Cu | Cu1+, Cu2+, and Cu3+ | Cu1+, and Cu2+ |
Group I | CuCr25 | Cu1+, Cu2+, Cu3+, Cr1+, Cr2+, and Cr3+ | Cu1+, Cu2+, and Cr2+ |
Group I | CuCr50 | Cu1+, Cu2+, Cu3+, Cr1+, Cr2+, and Cr3+ | Cu1+, Cu2+, and Cr2+ |
Group II | Pure W | W1+, W2+, W3+, and W4+ | W3+ |
Group II | WCu20 | Cu1+, Cu2+, Cu3+, W1+, W2+, W3+, and W4+ | Cu1+, Cu2+, and W3+ |
Group II | WCu30 | Cu1+, Cu2+, Cu3+, W1+, W2+, W3+, and W4+ | Cu1+, Cu2+, and W3+ |
The vacuum arc parameters are calculated by the transient multi-component MHD model based on our previous work [27]. The mass conservation equation of atoms is expressed as follows:
∂nA0∂t+∇⋅(nA0→ua)=−˙nA0. | (1) |
For ions at the highest ionization level considered in table 1, the mass conservation equation is expressed as follows:
∂nAj∂t+∇⋅(nAj→ui)=˙nA(j−1). | (2) |
For the other ions, the mass conservation equations are expressed as follows:
∂nAj∂t+∇⋅(nAj→ui)=˙nA(j−1)−˙nAj. | (3) |
The net ionization rate in equations (1)–(3) is given by:
˙nAj=αAjnAjne−βAjnA(j+1)n2e. | (4) |
The momentum conservation equations of ions and atoms are expressed as follows:
mini∂→ui∂t+∇⋅(mini→ui→ui)=−∇(pi+pe)+→J×→B+miRia(→ui−→ua)+S1, | (5) |
mana∂→ua∂t+∇⋅(mina→ua→ua)=−∇pa−miRia(→ui−→ua)−S1. | (6) |
The energy conservation equations of ions, atoms, and electrons are expressed as follows:
32nik∂Ti∂t+∇⋅((32nikTi+12mini→ui2)→ui)+∇⋅(−λi∇Ti)=−∇⋅(pi→ui)+3memineνeik(Te−Ti)+zieni→ui⋅→E−3Riak(Ti−Ta)+miRia(→ui−→ua)2+S2, | (7) |
32nak∂Ta∂t+∇⋅((32nakTa+12mina→ua2)→ua)+∇⋅(pa→ua)=3Riak(Ti−Ta)+miRia(→ui−→ua)2−S2, | (8) |
32nek∂Te∂t+∇⋅(32nekTe→ue)+∇⋅(−λe∇Te)=→J2σ−3memineνeik(Te−Ti)−Wi. | (9) |
The magnetic field is calculated by the following magnetic transport equation:
∂→B∂t−∇⋅(1μ0σ∇→B)=−1σ2→J×∇σ+1μ0σ2∇→B⋅∇σ+1nee2∇(nekTe)×∇ne+∇×(→ue×→B). | (10) |
The influences of ionization and recombination process on the momentum conservation equations and energy conservation equations in equations (5)–(8) are expressed as follows for pure metal contacts:
S1=miαA0nA0ne→ua−miβA0nA1n2e→ui, | (11) |
S2=32k(αA0nA0neTa−βA0nA1n2eTi). | (12) |
For alloy contacts, these two items are expressed as follows:
S1=mi(αA0nA0+αB0nB0)ne→ua−mi(βA0nA1+βB0nB1)n2e→ui, | (13) |
S2=32k[(αA0nA0+αB0nB0)neTa−(βA0nA1+βB0nB1)n2eTi]. | (14) |
Similar to the previous study [27], the subscripts A and B can be Cu, Cr, or W, representing different materials. Subscripts i, a, and e represents ions, atoms, and electrons, respectively. Subscript j can be 1, 2, and 3 representing single-charged, double-charged, and triple-charged ions, respectively. In these equations, the ionization and recombination process and the friction force among ions, atoms, and electrons were considered. A detailed explanation of the equations can be found in the previous studies [22, 27]. The explanations of the parameters are shown in table 2.
Symbol | Meaning | Symbol | Meaning |
n | Number density | k | Boltzmann constant |
t | Time | T | Temperature |
→u | Velocity | λ | Thermal conductivity |
α | Ionization rate coefficient | νei | Collision frequency between electrons and ions |
β | Recombination rate coefficient | zi | Average charge number |
m | Mass | e | Unit charge |
p | Pressure | →E | Electric field |
→J | Current density | Wi | Ionization energy |
→B | Magnetic field | σ | Electric conductivity |
Ria | Friction coefficient between ions and atoms | μ0 | Vacuum permeability |
When using the finite element analysis to calculate the magnetic vector potential, the calculation area should be at least five times that of the arc column in order to apply a set of reasonable boundary conditions. However, in this study, the magnetic induction intensity is calculated directly instead. In this case, the magnetic field can be calculated by the magnetic transport equation deduced by Maxwell equations and generalized Ohm’s law (i.e., equation (10)), and the boundary conditions can be given by the Ampere’s loop theorem [33, 34]. As for the other plasma parameters, the lateral boundaries are considered as a free boundary corresponding to the pressure-far-field boundary condition as given in the previous work [32, 34]. Therefore, the calculation area is as wide as the electrode diameter, which is enough for research on the electrode ablation. The detailed boundary conditions for the calculation area I can be found in the previous studies [22, 27].
The anode temperature is calculated by the following anode energy equation [30]:
∂(ρanH)∂t−∇⋅(λan∇Tan)=0, | (15) |
where ρan is the anode material density, H is the enthalpy, λan is the thermal conductivity, and Tan is the anode temperature. The detailed boundary conditions and material parameters for the calculation area II can be found in the previous studies [25, 27].
Figure 2 presents a comparison of the density distributions of ions and atoms with contacts made of CuCr50 and WCu20 at different instants. When the anode temperature is sufficient, the anode vapor can enter the arc column forming the anode vapor area with high ion density and high atom density at the anode side. At the cathode side, the atom density increases from the center to the edge as a result of the decrease of the electron temperature along the radial direction, which is consistent with the previous work [22]. Because the relative atomic mass of W is considerably higher than that of Cr, the arc column is more constricted with the contacts made by Cu–Cr alloy than with those made by the W–Cu alloy. Thus, the ion density distribution is more uniform in the W–Cu alloy case (figure 2). The atom density is considerably lower in the case of WCu20, leading to a lower maximum ion density.
Figure 3 displays the axial current density distribution in front of the anode at 4 ms, where no anode phenomena can be observed from the arc appearance. Compared with the case of group I, the current density is more uniform in the case of group II due to the high relative atomic mass of W, which is consistent with figure 2. Concerning group II, with the increase in the content of Cu in the contacts, the current density becomes constricted. However, for group I, the mass difference between Cu and Cr is too small to play an essential role. In this case, the Hall effect is the primary reason for current constriction. With a higher content of Cr in the contacts, the average charge number becomes higher, leading to a weaker Hall effect. However, the difference among the contacts in each group is not obvious.
Figure 4 displays the transient simulation results of ion density and atom density in front of the anode center. In group I, both ion density and atom density in front of the anode center increase with the decrease in Cr content from 4 to 5 ms because more Cr content leads to a lower saturated vapor pressure in the case where the anode temperature is lower than the melting point of Cr [25]. After 5 ms, the difference in the density becomes negligibly small. In the case of pure W contacts, the anode phenomena do not occur because of their high melting point. Therefore, the ion density is proportional to the arc current, whereas the atom density is inversely proportional to the arc current because the ionization process is more intense at a higher arc current. Compared with Cu–Cr alloy contacts, the anode vapor density is lower in W–Cu alloy contacts. Accordingly, ion density in group II is lower than in group I.
Figure 5 displays the transient simulation results of axial ion velocity in front of the anode center. The ion velocity is on the order of 103 m/s, which is consistent with the experimental results in the case of high-current vacuum arc [35]. Before the anode vapor appears, ions are generated at the cathode side and accelerated by the pressure gradient from the cathode to the anode. The ion velocity at the anode side decreases with the increase in the average mass. When sufficient anode vapor enters the arc column, the ions are decelerated by the friction force. In W–Cu alloy contacts, the axial ion velocity can even be negative because the friction force is proportional to the ion mass (see equation (5)). After about 7 ms, the atom density at the anode side begins to decrease (see figure 4(b)). Then the friction between the atoms and the ions becomes lower, leading to the increase of the ion velocity.
Figure 6 displays the transient simulation results of the plasma temperature in front of the anode center. The electron temperature depends on the Joule heat, namely the current density and conductivity. In group II, the collision frequency between the ions and electrons was higher because of the higher average charge number, leading to a lower conductivity [22]. Therefore, although the current density is lower in group II than in group I, the electron temperature is higher. Furthermore, the thermal conductivity of electrons in group II is lower because of its high average charge number, which is not beneficial to heat conduction, leading to a high electron temperature. The ion temperature is dominated by the energy exchange with electrons, which is inversely proportional to the ion mass. Therefore, the difference among the materials before 4 ms is small. The presence of the anode vapor considerably decreases both the ion and electron temperature. A sharp increase is observed just before the decrease as a result of the friction between ions and atoms. Then the ion temperature decreases rapidly due to the energy exchange between the ions and atoms. As for the electron temperature, a decrease can also be observed due to the ionization energy loss. However, even if the anode vapor can reduce the electrical conductivity, the current density around the anode vapor area is still high due to the constriction of the arc current. Therefore, the influence of the anode vapor on the electron temperature is not that obvious as a result of the Joule heat.
Figures 7 and 8 display the energy flux from the vacuum arc to the anode estimated by the arc parameters. At 4 ms, under the comprehensive effect of arc parameters, the energy flux distributions in group II are more uniform but lower than in group I. As discussed in a previous study [27], the energy flux decreases at the anode center, and its maximum moves towards the anode edge under the influence of anode vapor. The fluctuation of the profiles in figure 8 during the decrease after approximately 4.5 ms is caused by the unstable expansion of the NAVA.
Figure 9 displays the anode temperature that was predicted with the energy flux. Table 3 presents the maximum anode temperature and corresponding instants. The maximum anode temperature always occurs after the current peak because of the thermal inertia. In W contacts, the anode center temperature can increase up to 2871 K. The anode temperature depends on the energy flux. Therefore, the anode temperature reached the maximum earlier in the other cases than in W contacts since the anode vapor could reduce the energy flux. However, in the case of W contacts and WCu20 contacts, the anode temperature increases more quickly than in the other cases because of the low specific heat capacity and low heat conductivity of W in spite of their low energy flux [25].
Group | Contact material | Maximum anode temperature (K) | The corresponding instant (ms) |
Group I | Pure Cu | 1984.4 | 6.55 |
Group I | CuCr25 | 2006.8 | 6.50 |
Group I | CuCr50 | 2038.0 | 6.55 |
Group II | Pure W | 2871.8 | 7.60 |
Group II | WCu20 | 2037.0 | 6.70 |
Group II | WCu30 | 1949.2 | 6.75 |
From table 3, the maximum anode temperature is around 2000 K when the anode vapor occurs. In our study, a simulation with WCu10 electrodes was also conducted and the anode temperature was found to be up to 2244 K. However, this result is not given since the arc calculation is not converged after about 8 ms. Nevertheless, this indicates that a higher anode temperature is possible with our model and the maximum anode temperature is not caused by the model or the calculation method.
Figure 10 displays the radial anode surface temperature profiles. The anode surface temperature distributions in group II are more uniform than in group I because the energy flux is more uniform in group II. Under the influence of anode vapor, the maximum of the energy flux moves to the anode edge, leading to a more uniform anode temperature distribution. This phenomenon indicates that the melting area of the anode can be considerably larger in the case of W–Cu alloy contacts.
Figure 9 reveals that the anode temperature can be higher than the melting point of Cu but lower than those of Cr and W. Therefore, the area with the temperature higher than the melting point of Cu was melted. Figure 11 displays the melting radius of the anode and reveals that the melting area is larger in W–Cu alloy contacts than in group I, which is consistent with section 3.2 (i.e., figure 10). This phenomenon indicates a severe erosion with W–Cu alloy contacts.
Anode vapor expansion depends on the pressure balance between the anode vapor and the cathode plasma [23]. For example, figure 12 reveals that the ion pressure in the case of WCu20 contacts is considerably lower than in CuCr50 contacts, which is beneficial to anode vapor expansion. When the anode phenomena occur, the ion pressure distribution exhibits two peak values. The distribution at the anode side is caused by the ionized anode vapor, whereas the other distribution represents the cathode plasma pressure. In WCu20 contacts, the peak ion pressure near the anode side is farther away from the anode compared with CuCr50 contacts, indicating a wider anode vapor expansion.
The vacuum arc plasma can be considered as a kind of ideal gas, namely
pi=nikTi. | (16) |
According to the experimental and theoretical research on the high-current vacuum arc, the ion density is in the order of 1020–1022 m−3 and the ion temperature is about 3–7 eV [32–37]. Therefore, the maximum ion pressure can be in the order of 103–104 Pa, which is consistent with figure 12.
Figure 13 displays the variation of ion and atom densities at 6 ms along the y-axis near the anode side. Although both ion and atom densities in front of the anode were lower in group II, the decline of them was slower in such a case. This phenomenon indicates that the anode vapor enters deep into the arc column in group II, which is consistent with the analysis. However, because the maximum atom density with contacts made of the W–Cu alloy was too low (see figures 4 and 13), the anode phenomena in W–Cu alloy contacts were less obvious than in Cu–Cr alloy contacts.
Here, CuCr50 and WCu20 contacts are considered examples to make a comparison. As displayed in figure 14, the NAVA is larger in WCu20 contacts than in the other cases. Therefore, the arc parameters in front of the anode are more likely to be affected by anode vapor, and the maximum energy flux moves from the anode center to the anode edge quickly (figure 15) when the anode phenomena occur. This phenomenon can be another reason for the uniform anode temperature distributions in W–Cu alloy contacts (figure 10).
According to the preceding analysis, pure W contacts have the best ablation resistance. However, this material is not suitable to be applied in the high-current interrupters due to its low electrical conductivity and fragility (especially at high temperature). From figure 11, the ablation radius with the W–Cu alloy is larger than radii in the other cases, indicating more melting of the Cu in the contacts. With the mass loss of Cu in the form of droplets, the contact characteristics made by W–Cu alloy may be similar to that made by pure W.
From figure 9, the anode temperature is higher than the melting point of Cu for a long time with pure Cu contacts. This indicates a severe mass loss of the contact material due to the strong mobility of melted Cu. Among the materials studied in this work, Cu–Cr alloy is the best choice for the contacts in high-current interrupters. However, with the increase of the Cr content in the contacts, the maximum anode temperature is higher. Therefore, CuCr25 contacts are better than CuCr50 contacts. This is also consistent with the experimental results [6].
In section 4.1, the anode phenomena are predicted to be more obvious in Cu–Cr alloys than in W–Cu alloys. Therefore, most of experimental studies on the anode phenomena in the past used Cu–Cr alloy contacts [13–17]. However, the movement of the melting pool of the anode surface and the formation of the anode plume are not discussed. Considering the complex mechanism of the anode plume expansion, the anode ablation characteristics can be different at the arc current high enough for a more active anode mode.
According to the experimental results of Lin et al [3], the vacuum arc with contacts made by W–Cu alloy distributed evenly and the erosion area on the anode surface was less concentrated than in Cu–Cr alloy. Simulation results are consistent with these experimental results. Lin et al [3] reported that W was left in W–Cu alloy contacts after several discharges because of the evaporation of Cu, leading to cracks and bad toughness. Figure 16 displays the density distributions of the anode vapor components at 6 ms. In WCu20 contacts, the W atom density in front of the anode is considerably lower than the Cu atom density. This phenomenon indicates that the W in the anode hardly melts, and the W atom in front of the anode is from the cathode plasma, which is consistent with the experimental results by the scanning electron microscope of Lin et al [3]. A similar phenomenon was reported by Nicolle et al [4].
Huang et al [25] estimated the anode temperature with various contact materials without considering anode vapor. According to their results, the anode temperature in the case of W contacts increased quickly and was higher than in the case of Cu–Cr alloy contacts, which is consistent with our results. Because the arc current density in their study was higher than in this study, the maximum anode temperature predicted by them was higher (e.g., 2700–2900 K for Cu–Cr alloy contacts).
In this study, the effect of the contact materials on the anode phenomena was studied using the MHD model. Here are some conclusions.
(a) The arc column was predicted to be more uniform in group II than in group I, leading to a more uniform anode surface temperature distribution and a larger anode erosion area.
(b) Anode vapor expansion was deeper in the W–Cu alloy contacts than in Cu–Cr alloy contacts. However, the anode phenomena in the W–Cu alloy contacts were less obvious because of their lower maximum atom density.
(c) In W–Cu alloy contacts, the anode vapor was dominated by Cu. This is the reason for the cracks on the anode surface and the bad toughness observed in experiments.
(d) Of the materials studied in this work, CuCr25 is the best choice for the contacts in high-current interrupters.
The data that support the findings of this study are available from the corresponding author upon reasonable request.
This research was supported by the Sichuan Science and Technology Program (No. 2024NSFSC0867) and National Natural Science Foundation of China (No. 52377157).
[1] |
Kantas S 2013 IEEE Trans. Plasma Sci. 41 1709 doi: 10.1109/TPS.2013.2265414
|
[2] |
Liu Z Y et al 2007 IEEE Trans. Plasma Sci. 35 856 doi: 10.1109/TPS.2007.896929
|
[3] |
Lin R J et al 2018 IEEE Trans. Plasma Sci. 46 3047 doi: 10.1109/TPS.2018.2854715
|
[4] |
Nicolle C et al Behavior of CuCr and WCu contacts during making tests at high voltage and high currents In: Proceedings of the 24th ISDEIV 2010 Braunschweig: IEEE 2010: 261
|
[5] |
Lin Y D et al 2023 IEEE Trans. Plasma Sci. 51 1502 doi: 10.1109/TPS.2023.3277199
|
[6] |
Wang L J et al 2022 IEEE Trans. Plasma Sci. 50 2652 doi: 10.1109/TPS.2022.3174723
|
[7] |
Slade P 1974 IEEE Trans. Parts Hybrids Packag. 10 43 doi: 10.1109/TPHP.1974.1134834
|
[8] |
Xiu S X et al 2011 Trans. Nonferrous Met. Soc. China 21 s389 doi: 10.1016/S1003-6326(11)61612-9
|
[9] |
Ghaderi Hamidi A, Arabi H and Rastegari S 2011 Int. J. Refract. Met. Hard Mater. 29 538 doi: 10.1016/j.ijrmhm.2011.03.009
|
[10] |
Craig Miller H 2017 IEEE Trans. Plasma Sci. 45 2366 doi: 10.1109/TPS.2017.2708695
|
[11] |
Liang F et al 2016 J. Phys. D: Appl. Phys. 49 125201 doi: 10.1088/0022-3727/49/12/125201
|
[12] |
Boxman R L and Goldsmith S 1983 J. Appl. Phys. 54 592 doi: 10.1063/1.332063
|
[13] |
Khakpour A et al 2018 J. Appl. Phys. 124 243301 doi: 10.1063/1.5057753
|
[14] |
Wang H D et al 2022 Phys. Plasmas 29 083501 doi: 10.1063/5.0095824
|
[15] |
Ye K et al 2021 Plasma Sci. Technol. 23 075506 doi: 10.1088/2058-6272/ac02a9
|
[16] |
Khakpour A et al 2017 IEEE Trans. Plasma Sci. 45 2126 doi: 10.1109/TPS.2017.2690572
|
[17] |
Kong G W et al 2011 IEEE Trans. Plasma Sci. 39 1370 doi: 10.1109/TPS.2011.2107529
|
[18] |
Khakpour A et al 2016 IEEE Trans. Plasma Sci. 44 3337 doi: 10.1109/TPS.2016.2625862
|
[19] |
Khakpour A et al 2019 J. Appl. Phys. 125 133301 doi: 10.1063/1.5086543
|
[20] |
Khakpour A et al 2017 J. Phys. D: Appl. Phys. 50 185203 doi: 10.1088/1361-6463/aa6494
|
[21] |
Zhang D et al 2019 Carbon 142 278 doi: 10.1016/j.carbon.2018.10.062
|
[22] |
Yang Z et al 2019 J. Appl. Phys. 126 193306 doi: 10.1063/1.5127964
|
[23] |
Wang L J et al 2019 Appl. Phys. Lett. 115 014101 doi: 10.1063/1.5110538
|
[24] |
Wang L J et al 2020 Phys. Plasmas 27 023514 doi: 10.1063/1.5129780
|
[25] |
Huang X L et al 2015 IEEE Trans. Plasma Sci. 43 2283 doi: 10.1109/TPS.2015.2443811
|
[26] |
Shmelev D L et al 2020 Self consistent simulation of development of anode spot in high current vacuum arc In: Proceedings of the 2020 7th International Congress on Energy Fluxes and Radiation Effects Tomsk, Russia: IEEE 2020: 393
|
[27] |
Yang Z, Wang L J and Gortschakow S 2021 J. Phys. D: Appl. Phys. 54 505201 doi: 10.1088/1361-6463/ac25b0
|
[28] |
Yang Z et al 2022 J. Phys. D: Appl. Phys. 55 415201 doi: 10.1088/1361-6463/ac84ea
|
[29] |
Shmelev D L, Uimanov I V, and Frolova V P 2018 Numerical simulation of low-current vacuum arc plasma jet in strong axial magnetic field In Proceedings of the 2018 28th International Symposium on Discharges and Electrical Insulation in Vacuum. Greifswald, Germany: IEEE 2018: 377
|
[30] |
Huang X L et al 2016 J. Phys. D: Appl. Phys. 49 075202 doi: 10.1088/0022-3727/49/7/075202
|
[31] |
Anders A and Yushkov G Y 2002 J. Appl. Phys. 91 4824 doi: 10.1063/1.1459619
|
[32] |
Wang L J et al 2006 J. Appl. Phys. 100 113304 doi: 10.1063/1.2388734
|
[33] |
Beilis I I et al 1998 J. Appl. Phys. 83 709 doi: 10.1063/1.366742
|
[34] |
Wang L J et al 2017 J. Phys. D: Appl. Phys. 50 095203 doi: 10.1088/1361-6463/aa5620
|
[35] |
Schellekens H 1983 J. Appl. Phys. 54 144 doi: 10.1063/1.331740
|
[36] |
Zhirkov I, Eriksson A O and Rosen J 2013 J. Appl. Phys. 114 213302 doi: 10.1063/1.4841135
|
[37] |
Boxman R L 1974 J. Appl. Phys. 45 4835 doi: 10.1063/1.1663143
|
[1] | Ye HUA, Ping WU, Hong WAN, Shuxin BAI, Jinyu GONG, Meng ZHU, Xianchen BAI, Guangshuai ZHANG. Effects of anode material on the evolution of anode plasma and characteristics of intense electron beam diode[J]. Plasma Science and Technology, 2023, 25(9): 095402. DOI: 10.1088/2058-6272/acc8bb |
[2] | Jun HE (何鋆), Zhiquan SONG (宋执权), Cunwen TANG (汤存文), Peng FU (傅鹏), Jie ZHANG (张杰). Study of contact resistance in the design of a pyro-breaker applied in superconducting fusion facility[J]. Plasma Science and Technology, 2019, 21(6): 65602-065602. DOI: 10.1088/2058-6272/aaf590 |
[3] | Xianhai PANG (庞先海), Zixi LIU (刘紫熹), Shixin XIU (修士新), Dingyu FENG (冯顶瑜). Arc characteristics during the instability stage on transverse magnetic field contacts[J]. Plasma Science and Technology, 2018, 20(9): 95505-095505. DOI: 10.1088/2058-6272/aac50a |
[4] | Hantian ZHANG (张含天), Tianwei LI (厉天威), Bing LUO (罗兵), Yi WU (吴翊), Fei YANG (杨飞), Hao SUN (孙昊), Li TANG (唐力). Influence of the gassing materials on the dielectric properties of air[J]. Plasma Science and Technology, 2017, 19(5): 55504-055504. DOI: 10.1088/2058-6272/aa57f5 |
[5] | CUI Xinglei (崔行磊), ZHOU Xue (周学), ZHAI Guofu (翟国富), PENG Xiyuan (彭喜元). Evaporation Erosion During the Relay Contact Breaking Process Based on a Simplified Arc Model[J]. Plasma Science and Technology, 2016, 18(5): 512-519. DOI: 10.1088/1009-0630/18/5/12 |
[6] | Emre SEKER, Mehmet Ali KILICARSLAN, Serdar POLAT, Emre OZKIR, Suat PAT. Non-Thermal Atmospheric Plasma: Can it Be Taken as a Common Solution for the Surface Treatment of Dental Materials?[J]. Plasma Science and Technology, 2016, 18(4): 417-423. DOI: 10.1088/1009-0630/18/4/15 |
[7] | NIU Guojian(牛国鉴), LI Xiaochun(李小椿), DING Rui(丁锐), XU Qian(徐倩), LUO Guangnan(罗广南). Molecular Dynamics Simulations of Deposition and Damage on Tungsten Plasma-Facing Materials by Tungsten Dust[J]. Plasma Science and Technology, 2014, 16(8): 805-808. DOI: 10.1088/1009-0630/16/8/13 |
[8] | M’hammed ABBAOUI, Andr′e LEFORT, Erwann CARVOU, Damien SALLAIS, James Brian Alexander MITCHELL, Noureddine BEN JEMAA. Formation of a 40 A DC Current Arc During the Opening of Silver Contacts[J]. Plasma Science and Technology, 2014, 16(5): 471-478. DOI: 10.1088/1009-0630/16/5/06 |
[9] | WANG Lijun(王立军), HUANG Xiaolong(黄小龙), JIA Shenli(贾申利), ZHOU Xin(周鑫), SHI Zongqian(史宗谦). Modeling and Simulation of Deflected Anode Erosion in Vacuum Arcs[J]. Plasma Science and Technology, 2014, 16(3): 226-231. DOI: 10.1088/1009-0630/16/3/10 |
[10] | ZHANG Ling(张玲), WANG Lijun (王立军), JIA Shenli(贾申利), YANG Dingge(杨鼎革), SHI Zongqian(史宗谦). Numerical simulation of high-current vacuum arc with consideration of anode vapor[J]. Plasma Science and Technology, 2012, 14(4): 285-292. DOI: 10.1088/1009-0630/14/4/04 |
Group | Contact material | Consideration of ion species in calculation area I | Ion species emitted from the cathode |
Group I | Pure Cu | Cu1+, Cu2+, and Cu3+ | Cu1+, and Cu2+ |
Group I | CuCr25 | Cu1+, Cu2+, Cu3+, Cr1+, Cr2+, and Cr3+ | Cu1+, Cu2+, and Cr2+ |
Group I | CuCr50 | Cu1+, Cu2+, Cu3+, Cr1+, Cr2+, and Cr3+ | Cu1+, Cu2+, and Cr2+ |
Group II | Pure W | W1+, W2+, W3+, and W4+ | W3+ |
Group II | WCu20 | Cu1+, Cu2+, Cu3+, W1+, W2+, W3+, and W4+ | Cu1+, Cu2+, and W3+ |
Group II | WCu30 | Cu1+, Cu2+, Cu3+, W1+, W2+, W3+, and W4+ | Cu1+, Cu2+, and W3+ |
Symbol | Meaning | Symbol | Meaning |
n | Number density | k | Boltzmann constant |
t | Time | T | Temperature |
→u | Velocity | λ | Thermal conductivity |
α | Ionization rate coefficient | νei | Collision frequency between electrons and ions |
β | Recombination rate coefficient | zi | Average charge number |
m | Mass | e | Unit charge |
p | Pressure | →E | Electric field |
→J | Current density | Wi | Ionization energy |
→B | Magnetic field | σ | Electric conductivity |
Ria | Friction coefficient between ions and atoms | μ0 | Vacuum permeability |
Group | Contact material | Maximum anode temperature (K) | The corresponding instant (ms) |
Group I | Pure Cu | 1984.4 | 6.55 |
Group I | CuCr25 | 2006.8 | 6.50 |
Group I | CuCr50 | 2038.0 | 6.55 |
Group II | Pure W | 2871.8 | 7.60 |
Group II | WCu20 | 2037.0 | 6.70 |
Group II | WCu30 | 1949.2 | 6.75 |