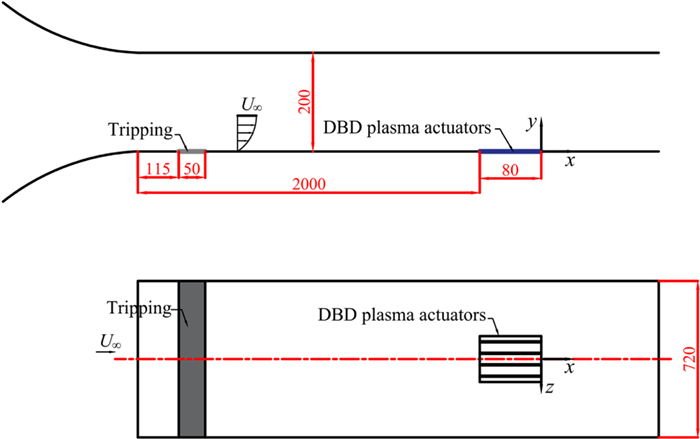
Citation: | Yueqiang LI, Bin WU, Chao GAO, Haibo ZHENG, Yushuai WANG, Rihua YAN. Turbulent boundary layer control with DBD plasma actuators[J]. Plasma Science and Technology, 2023, 25(4): 045508. DOI: 10.1088/2058-6272/aca503 |
The flat-plate turbulent boundary layer at Reτ =1140 is manipulated using a spanwise array of bidirectional dielectric barrier discharge (DBD) plasma actuators. Based on the features of no moving mechanical parts in the DBD plasma control technology and hot-wire anemometer velocity measurements, a novel convenient method of local drag reduction (DR) measurement is proposed by measuring the single-point velocity within the linear region of the viscous sublayer. We analyze the premise of using the method, and the maximum effective measurement range of −73.1% < DR < 42.2% is obtained according to the experimental environment in this work. The local drag decreases downstream of the center of two adjacent upper electrodes and increases downstream of the upper electrodes. The magnitude of the local DR increases with increasing voltage and decreases as it moves away from the actuators. For the spanwise position in between, the streamwise distribution of the local DR is very dependent on the voltage. The variable-interval time-average detection results reveal that all bursting intensities are reduced compared to the baseline, and the amount of reduction is comparable to the absolute values of the local DR. Compared with previous results, we infer that the control mechanism is that many meandering streaks are combined together into single stabilized streaks.
The pursuit of skin friction drag control in turbulent boundary layers is of great importance not only for fundamental research, but also for practical engineering applications [1]. Based on whether external energy is required to drive the control, drag reduction methods can be grouped into passive and active techniques [2]. The dielectric barrier discharge (DBD) plasma flow control method [3–6], as an active flow control technology, has recently attracted a great deal of interest because of its advantages, e.g. no moving mechanical parts, a simple structure and a rapid response [7–13].
Jukes et al [9] alternately activated the electrodes of two opposing sets of asymmetric plasma actuators to mimic spanwise oscillations to control the turbulent boundary layer at the Reynolds number Reτ =δuτ/ν=380 (boundary layer thickness δ, friction velocity uτ, kinematic viscosity ν), and the local drag downstream of the actuators was reduced by up to 45%. Corke and Thomas [2] applied pulsed-DC actuators, generating a near-wall steady spanwise flow to control the turbulent boundary layer (the estimation range of the Reτ is 1700‒6200) and measured the maximum drag reduction (DR) of 70%. Furthermore, a substantial positive net energy saving was achieved. Their work that followed performed low-speed experiments (Reτ =1400) to document the changes in the turbulence characteristics of the boundary layer [10]. Using the quadrant splitting method, the results presented a decrease in duration and an increase in the time between 'ejection' (Q2) and 'sweep' (Q4) events. As a result of conditional flow field reconstruction, a suppression of λ2 vortical structures was found. This was consistent with the premise that the control would actively intervene with an autonomous cycle involving lift-up and break-up of coherent streamwise vorticity that is associated with the low-speed wall streak structure. Cheng et al [11] found a DR of up to 26% downstream of the actuators using plasma-generated large-scale streamwise vortices, and these vortices pushed numerous meandering streaks to form a stabilized streak, leading to suppression of transient growth and near-wall turbulent production. Mahfoze and Laizet [12] simulated near-wall spanwise-oriented jets to control the turbulent boundary layer, in which the jets liked the flow generated by unidirectional pulsed-DC DBD actuators [2], and obtained a DR of 33%. Turbulent structure analysis indicated that the control inhibited quasi-streamwise vortices, resulting in the disappearance of sweep events. Altintas et al [13] obtained a DR of 13% using spanwise oscillated body forces generated by DBD plasma actuators. The two-point velocity correlation did not exhibit any minima, indicating an absence of streak formation in the vicinity of the wall. The last two studies were performed using direct numerical simulation for a fully developed turbulent channel flow mainly at Reτ =180, and a simplified phenomenological model was used to simulate plasma-actuator-induced body force instead of solving the species transport equations for the plasma dynamics. Despite all these achievements, there has been little consensus on DR using the control of DBD plasma actuators.
Generally, the DR is measured over an area or single point, denoted here as local DR. DR over an area is measured quickly and accurately and is also closely related to practical engineering applications. However, local DR measurement can offer more information on flow fields with control, to improve the control strategy and uncover the control mechanism combined with other turbulent characteristics. For local drag measurement, Hutchins and Choi [14] pointed out that the practicality and accuracy of many existing methods suffer when the boundary layer flow under consideration is noncanonical, as in flow with control, and they proposed that the local drag can be evaluated via a single velocity measurement made at a known wall-normal distance within the linear region of the viscous sublayer. This technique relies on accurate probe positioning. Although two methods for achieving this positioning were outlined, they were not easy to implement in a higher velocity flow. By considering the feature of DBD plasma control technology, i.e. no moving mechanical parts, we propose a new convenient method to obtain local DR without accurate probe positioning.
In this work, we investigate flat-plate turbulent boundary layer control using a spanwise array of DBD plasma actuators. The experimental details are given in section 2. The results, including the new method, are presented and discussed in section 3. The work and the control mechanism are concluded in section 4.
Experiments are conducted in a low-speed blowdown wind tunnel with a closed test section in the National Key Laboratory of Aerodynamic Design and Research at Northwestern Polytechnical University. The freestream velocity in the test section with a 720×200 mm2 cross section ranges from 5 to 20 m s−1 with a longitudinal turbulence intensity of less than 0.4%. Both sidewalls are made of Perspex for observation during the experiment, and the upper wall, made of a steel plate, has a rectangular 675×220 mm2 measuring window used to connect the hot-wire probe in the test section and an external computer-controlled traversing system. The lower wall, made of a smooth Perspex plate, serves as a flat-plate model for the experiment, and its leading edge is close to the exit of the wind tunnel contraction section (see figure 1). A 50 mm wide sandpaper sheet is placed 115 mm downstream of the leading edge to trip the boundary layer. In this paper, the experimental measurement area is approximately 2000 mm downstream of the leading edge, where the free velocity U∞ is 7.5 m s−1. The major parameters of the turbulent boundary layer are given in table 1, including the boundary layer thickness δ, displacement thickness δ*, momentum thickness θ, friction velocity uτ, viscous length scale δν=ν/uτ, shape factor H=δ*/θ and Reynolds numbers Reτ =δuτ/ν and Reδ* =δ*U∞/ν.
U∞ (m s−1) | δ (mm) | δ* (mm) | θ (mm) | uτ (m s−1) | δν (mm) | H | Reτ | Reδ* |
7.5 | 55 | 8.46 | 6.15 | 0.31 | 0.048 | 1.37 | 1140 | 4262 |
The spanwise array of DBD plasma actuators is arranged on a 170×96 mm2 Perspex panel, shown in figure 2(a), which is mounted on the lower wall of the test section. The misalignment of the sides between the panel and lower wall is less than 0.1 mm within the viscous sublayer, which has little influence on the flow. The actuators have an effective streamwise length of 80 mm, and the front is 10 mm downstream of the front edge of the panel. The array consists of four 2 mm wide copper sheets as upper electrodes and an 80 mm wide copper sheet as a lower electrode; in addition, a layer of 0.2 mm thick Kapton as dielectric material is slotted in between (figure 3). The upper electrodes are arranged along the streamwise direction with a 20 mm wide electrode spacing from the left side of one upper electrode to that of the adjacent upper electrode.
The lower electrode connects to the ground, and the upper electrodes connect to an AC power source to provide a burst of high voltage. Figure 4 shows a voltage waveform schematic of burst-mode actuation. Here, Ton indicates the duration when the voltage peak-to-peak value Vp-p is not 0 during one cycle of time T. The duty cycle D is defined as Ton/T. Here, F is the frequency of the AC power source. In this paper, we fix the burst frequency, f=1/T=200 Hz, D=0.5, F=6.9 kHz and Vp-p=7 kV, unless otherwise indicated. Figure 2(b) shows that plasma is uniformly produced on both sides of the upper electrodes when the plasma is on at the still air.
We regard the center of the downstream edge of the actuators as the coordinate origin, as shown in figure 1. Here, x, y and z denote the streamwise, wall-normal and spanwise directions, respectively.
The streamwise velocity is measured using a Dantec streamline constant temperature hot-wire anemometer and a 55P15 standard boundary layer probe that is 1.25 mm long and 5 μm in diameter. The overheat ratio is set to 1.8 during hot-wire operation. Before the wind tunnel experiment, the 55P15 probe is calibrated for velocities ranging from 0.5 to 15 m s−1 using the automatic calibration unit. The probe is mounted on a computer-controlled traversing system to traverse the boundary layer with a spatial resolution of 0.02 mm in the wall-normal direction.
Figure 5 shows the measurement points of the hot wire. Considering that the DBD plasma actuators are symmetric about the centerline, i.e. z=0 mm, we assume that the controls on the left and right are statistically identical and the hot-wire measurements are only limited to behind one half of the middle actuator pair. There are three and five measurement points in the spanwise direction and streamwise direction, respectively. When measuring the velocity in the near-wall region, the sampling frequency and time are set to 2 kHz and approximately 30 s, respectively. In other cases, when measuring the boundary layer velocity for the calculation of statistical characteristics and variable-interval time-average (VITA) analysis, these are set to 20 kHz and 5 s, respectively.
To obtain the temperature change generated by actuators when the plasma is on, the cold wire resistance of the 55p15 probe is measured. The sampling frequency and time are 2 Hz and 10 s, respectively.
In this paper, the flow without control, i.e. with plasma off, is taken as the baseline flow. The superscripts '+' and '*' indicate nondimensionalization by the baseline and the 'actual' wall units, respectively. The subscripts 'no' and 'c' indicate the condition without control and with control. Here, u and u' denote streamwise time-averaged and fluctuating velocities, respectively, and urms denotes the root mean square (rms) of the fluctuating velocity.
To ensure that the uncontrolled boundary layer is turbulent, we measure the velocity profile upstream and downstream of the actuators. Figure 6 shows the velocity profiles 25 mm upstream (x=−105 mm) and 15 mm downstream (x =15 mm) of the actuators. The velocity profile fits the classical log-law well (Clauser [15]) at 30 < y+ < 200, which not only illustrates that the boundary layer where the actuators are placed is a fully developed turbulent boundary layer but also implies that artificial roughness, such as the aforementioned misalignment, and the upper electrodes essentially do not affect the flow field.
For the turbulent boundary layer, the flow clinging to the wall is determined by the viscous fraction; accordingly, the velocity is linearly distributed with distance from the wall. The linear velocity region is called the viscous sublayer, where u+=y+. For nearly parallel flow and smooth walls, the sublayer has a linear region up to y+=5 [16]. During the velocity measurement of the hot wire in the sublayer, the wall effect is that, as the heated element of the hot wire approaches the wall, there is an additional conductive heat transfer to the wall, deteriorating the linear velocity distribution very near the wall and consequently shortening the linear region. By combining velocity measurements using hot-wire anemometry with accurate positioning of the sensor element with respect to the wall, Hutchins and Choi [14] proposed that the local drag can be evaluated via a single velocity measurement made at a known wall-normal distance within the linear region of the viscous sublayer. This technique relied on accurate probe positioning, and two methods for achieving this were outlined. However, when the free velocity increases, these two methods are difficult to perform to obtain sufficiently accurate positioning because the linear region size decreases almost linearly with increasing flow velocity by increasing the fraction velocity.
With respect to the flow control field, the conventional measurement method of the local DR directly measures the amount of local drag reduction ∆τ =
DR=τno−τcτno×100% | (1) |
where τ denotes shear stress.
Combined with the no moving mechanical parts feature of DBD plasma control technology, we propose a convenient new method to obtain local DR that does not need accurate probe positioning. The detailed method is as follows: we position the hot-wire element at a predetermined wall-normal height y0 within the linear region of the viscous sublayer. Then, the velocities without and with control (denoted as uno and uc) are measured. Therefore, the shear stresses without control τno and with control τc are:
τno=μnounoy0 | (2) |
τc=μcucy0 | (3) |
where μ indicates the viscosity. The viscosity difference μno − μc is dependent on the temperature change. In this paper, the change generated by plasma is within 2 ℃ (see figure 9 below); therefore, the viscosity difference is less than 1% relative to viscosity μno. Therefore, we assume μno=μc. For the same reason, the density ρ and kinematic viscosity ν are kept the same in the following.
Hence, the local drag reduction DR is:
DR=τno−τcτno×100%=uno−ucuno×100%. | (4) |
Note that the existence of linearity in the viscous sublayer is not assured per se (although researchers commonly assume so) [14], especially in the controlled boundary layer. Consequently, the existence of linearity in the sublayer of the uncontrolled and controlled boundary layers should be ascertained experimentally. We choose the controlled boundary layer at position x/δ=0.27, z=10 mm as a representative among the controlled boundary layers because its deviation from the baseline is almost the largest in both the local drag and boundary layer profiles (see figures 10 and 13 below). Figure 7 shows the wall-normal distributions of streamwise velocity u in the near-wall region with a resolution of approximately 0.01 mm. The data of both uncontrolled and controlled boundary layers fit the law of the wall, i.e. u* =y*, for y* in the range 3.8‒5, which is similar to the results of Cheng et al [11].
The premise of the new method is that the position y0 is always in the linear region before and after control. By analyzing this premise, we obtain an effective measurement range of local drag reduction DR. Assuming that local drag reduces with control, we place the hot-wire element at nearly y0+=5 before control. After controly0* =y0uτ/ν should decrease due to the reduction in friction velocity uτ but y0* > 3.8. Hence, the friction velocities
3.8<y0uτc/νc<y0uτno/νno<5. | (5) |
Then, according to the definition
τnoτc=(uτnouτc)2=(53.8)2. | (6) |
With the definition of local DR, the ceiling of the effective measurement is DR=42.2%. Similarly, the floor is DR=−73.1%.
The seven repeated measurements of velocity u at y+=4.1 are used to give a relative error of 0.83%; therefore, the relative error of the proposed method is approximately 1.2% (calculated using the test method of the square sum root) according to equation (4). To ensure that the new method is reliable, we compare the local DR measured using the method with the conventional near-wall linear region velocity gradient fit method [14]. Using the two methods, the local DRs at z=10 mm are −48% and −47.7%, respectively. The latter is calculated by fitting the velocity gradient at y* =3.8–5 from figure 7. The comparison indicates that the new method is reliable.
Figure 8 shows the procedure of single-point measurement of local DR. The step by step procedure is as follows. First, the velocity in the near-wall region is measured to find the linear velocity region where u* =y*, as shown in figure 7; for example, y* =3.8‒5 in this paper. Second, by estimating whether the local drag reduces or increases by positioning the hot-wire element at nearly y0+=4 before control, we measure the velocity without and with control. If plasma control makes the velocity smaller, uno > uc, it indicates that the local drag reduces. If not, the local drag increases. Third, the position is adjusted to approximately y0+=5 in the local drag-reduced boundary layer or y0+=3.8 in the local drag-increased boundary layer to ensure the maximum effective measurement range. Fourth, the velocity is measured again without and with control, and the local DR is calculated according to equation (4). Last, we determine whether the DR falls into the measurement range −73.1% < DR < 42.2%. If so, the measurement is valid.
The hot-wire probe operating at a high overheat ratio makes the ratio of the velocity sensitivity to the temperature sensitivity large [17]. However, the error of the velocity measurement introduced by the slow drift in the ambient temperature generated by plasma needs to be considered on the basis of the experimental result in that there is an approximately 2% error of velocity measurement for every 1 ℃ change in temperature in air [17]. Figure 9 shows the temperature increase measured after the actuators have been discharging for 15 min when the rate of the increase is much slower.
The maximum and minimum temperature increments are 1.8 ℃ at z=5 mm and 1.6 ℃ at z=10 mm, respectively. The reason for the difference is mainly related to the plasma and plasma-induced flow. The plasma generated at z= 7‒9 mm (figure 2(b)) heats the nearby air, and then the heated air convects toward z=0 mm because of the spanwise jet induced by the plasma, which is directed from z=10 mm to z=0 mm (see figure 17). Simultaneously, to replenish the ejected fluid, entrained air immediately from the outside near z=10 mm moves into the vicinity of the plasma region. Hence, the air at z=10 mm is not heated directly by the plasma, and the temperature increase is caused by heat transfer from the heated air.
The temperature increase decreases monotonically with distance from the wall, and the thickness of the temperature boundary layer is approximately 0.22δ, which seems to be independent of the spanwise position. This is different from the temperature distribution of Jukes et al [9]; there is a peak at y+=25, which closely coincides with the center of the co-rotating vortices. This difference may result from the different discharging times before measuring. Our time is sufficiently long (15 min) to lead to thermal accumulation in the Perspex panel where the actuators are placed; therefore, the distribution of the temperature increase relies on heated air and the panel together. The following velocity data have been corrected for temperature increase.
With the benefit of the efficiency of the new method for measuring local DR in section 3.2, we can measure a mass of data for comparison and analysis. Figure 10 shows the spatial distribution of the local DR varying with voltage. In general, the local drag increases at z=10 mm just directly downstream of the upper electrode and quickly recovers to baseline when moving away from the actuators due to the gradually weakening control effect.
In contrast to z=10 mm, the local drag decreases at z=0 mm and very slowly recovers to baseline, such as Vp-p=9 kV. This is similar to the findings of Cheng et al [11]. However, the local DR at Vp-p=7 kV and 8 kV does not present a decreasing trend with distance from the actuators. We think this may be caused by the less obvious decrease in local DR because the measuring region is not long enough, as well as measurement error. In addition, the discharge states are not identical during measurement due to the slow deterioration of the actuators as the discharging time increases. With regard to Vp-p=6 kV, the local drag barely changes close to the actuators and decreases very slowly far away from the actuators. Based on the accepted results, the maximum velocity of spanwise plasma-induced flow increases with increasing voltage in the low electrical power range [18, 19]. The main reason for this is that the maximum velocity is small at Vp-p=6 kV; hence, the control effect imposed on the baseline flow by the plasma sluggishly reaches z=0 mm as it moves away from the actuators. Moreover, probably due to the aforementioned results, the local DR monotonously increases with increasing voltage at z=0 mm. In contrast, the local DR decreases at z=10 mm.
The streamwise distribution of the local DR at z=5 mm has a strong dependence on voltage. The local drag first decreases and then increases with increasing voltage near the actuators, and the valley is near Vp-p=7 kV. For the first two low voltages Vp-p=6 kV and 7 kV, the DR curves are similar to those at z=0 mm. When the voltage increases to 8 kV and 9 kV, the DR curves are similar to those at z=10 mm but have an upward migration, in which the local DR gradually increases from negative to positive and the null points are consistently near x/δ=0.64. This consistency is interesting because the difference in the local DR close to the actuators is very large; specifically, the local DR at Vp-p=9 kV is almost twice that at Vp-p=8 kV (x/δ=0.27). The reason for this phenomenon is unclear thus far, and more detailed research is needed, which is beyond the scope of this paper.
Figure 11 shows the mean velocity profile normalized by the baseline and their own actual fraction velocity. The actual fraction velocity
uτc=uτno√(1−DR) | (7) |
where
Figure 11(a) indicates that in local drag-reduced boundary layers, such as those at z =0 mm and 5 mm, the plasma control causes a slight velocity deficit in the buffer and logarithmic regions. The local drag increase, such as z=10 mm, is the opposite, and the deviation from the baseline profile is strong. These correspond to the results (figure 10(b)) in which the absolute values of the local DR at z=10 mm are greater than those at z=0 mm and 5 mm. Furthermore, the controlled profiles seem to approach first and then run away from baseline step by step from z=0 to 10 mm. We note the wake region (y+ > 200) with control remains static, which implies that the electromagnetic interference when the plasma is on has little influence on the velocity u. The same is true for urms in figures 14 and 15.
When the velocity profiles are normalized by their own actual fraction velocities in figure 11(b), the profiles retain a well-defined logarithmic region. In local drag-reduced boundary layers, the profiles have a tiny increase in the slope of the log-law that translates into a decrease in the von Kármán coefficient (figures 12(a) and (b)). However, for local drag-increased boundary layers, the slope remains the same, but the logarithmic region shifts down, indicating a decrease in the additive constant (figure 12(c)), which is consistent with the results of Cheng et al [11].
The streamwise distributions of the controlled boundary layer profiles are shown in figure 13. In figures 13(b) and (e), the profile at x/δ=0.27 is missing because the actuators are broken down during hot-wire measurement. In local drag-reduced boundary layers, the profiles hardly vary with the streamwise distance. For the local drag-increased boundary layers, however, the deviation of the profile from baseline gradually weakens. These results are in good agreement with the trends of the local DR along the distance from the actuators (figure 10(b)).
Figure 14 depicts the rms of the fluctuating velocity profile at x/δ=0.45. The urms in the wake region with control remains static, similar to the mean velocity profiles, which implies that the plasma control described here belongs to inner-scale control. In the local drag-reduced boundary layers, the peak near y+=15 is almost constant. At z=0 mm, the urms increases in the buffer and logarithmic regions (20 < y+ < 200), whereas at z=5 mm, the urms only increases in the logarithmic region (40 < y+ < 200), and the second peak appears near y+=90. For the drag-increased boundary layer, the peak dramatically reduces.
The streamwise distributions of the urms are presented in figure 15. At z=0 mm and 5 mm (figures 15(a) and (b)), the deviation from the baseline reduces slightly. At z=5 mm, the second peak gradually disappears. In agreement with the local DR results, the urms did not return to baseline in the measuring region. Conversely, the urms returned to normal step by step from plateau to peak at z=10 mm.
The bursting events play an important role in the near-wall turbulence-production process and may be affected by plasma control. The events are detected from the fluctuating velocity signal u' using the VITA technique [20]. The detection criterion depends on the averaging time T, which must be of the order of the time scale of bursting events and a threshold level k on the VITA variance signal. Following Cheng et al [11], we set T+=10 and k=1.
Figure 16 shows the ensemble-averaged fluctuating velocity ⟨u'⟩t based on VITA detection normalized by local actual urms at x/δ=0.27. For z=0 mm and 5 mm, compared to the baseline, the bursting intensity contracts by approximately 7% and 5%, respectively, which is almost equal to the DR, while the frequency of bursting events contracts by 18% and amplifies by 20%, respectively.
For the local drag-increased boundary layer (z = 10 mm), the intensity substantially reduces by approximately 35%; however, the frequency nearly doubles. Combined with the result that the urms peak decreases significantly, it may be inferred that the control leads to more premature bursting events that cause local drag increases.
The turbulent boundary layer at Reτ =1140 is manipulated using a spanwise array of DBD plasma actuators. Based on the feature of no moving mechanical parts in DBD plasma control technology, a single-point measurement method of local DR without requiring accurate probe positioning is proposed. The method positions the hot wire within the linear region of the sublayer and measures the velocity before and after control. Then, the local DR is obtained according to equation (4). By analyzing the premise of using the method, we obtain the maximum effective measurement range −73.1% < DR < 42.2% based on the experimental environment in this paper.
The thermal effect generated by plasma is slightly different in the spanwise direction, and the maximum and minimum temperature increments are 1.8 ℃ at z=5 mm and 1.6 ℃ at z=10 mm, respectively. The temperature increase decreases monotonically with distance from the wall, and the thickness of the temperature boundary layer is consistently approximately 0.22δ.
The effect of voltage on the spatial distribution of the local DR indicates that the local drag decreases at z=0 mm and increases at z=10 mm. The magnitude of the local DR increases with increasing voltage and decreases as it moves away from the actuators. For z=5 mm, the streamwise distribution of the local DR is very dependent on the voltage.
The mean velocity profiles show a slight velocity deficit in the near-wall region in local drag-reduced boundary layers, while it is just the opposite for the drag-increased boundary layers. The mean velocity profiles normalized by actual fraction velocity retain a well-defined logarithmic region, but the slope and the additive constant change. In the local drag-reduced case, the urms increases in the buffer and logarithmic regions; in particular, the second peak appears near y+=90 at z=5 mm. As the local drag increases, the peak dramatically reduces to form a plateau. In all cases, the wake region with control remains static.
The VITA detection results reveal that all bursting intensities decrease compared to the baseline, and the magnitude of reduction is comparable to the absolute values of the local DR. In the local drag-reduced case, the frequency of bursting events does not vary much. However, in the local drag-increased case, the frequency nearly doubles.
Although detailed turbulent coherent structures, such as spanwise and streamwise vortices and streaks, have not been examined in this paper, we will give a brief explanation of the plasma control on the turbulent boundary layer by combining the results outlined above with other studies. The DBD plasma produces a spanwise jet directed from the upper electrode to the lower electrode. Based on the symmetrical layout of DBD plasma actuators and fluid continuity, the plasma-induced flow is depicted schematically in figure 17. This is similar to the flow presented in figure 1(a) of Yao et al [21], but the plasma-induced flow is not continuous due to the duty cycle τ=0.5. Moreover, the spanwise trend of the local DR is also similar to the curve in figure 4(l) of Yao et al without considering the magnitude, which is relative to the boundary layer and control parameters, such as the Reτ and electrode spacing. Our results, including the local DR distribution and boundary layer statistical characteristics, are also similar to the experimental results of plasma control in Cheng et al [11], whose excitation is steady, as in Yao et al. However, the VITA results are different from those of Cheng et al, who found that the variation in bursting event intensity is consistent with the variation in local drag. We think this may be caused by the difference in the Reτ and the excitation state (steady and unsteady); note that unsteady excitation can introduce moving vortices [22]. In conclusion, we infer that the control mechanism in this paper resembles the conclusions of Yao et al and Cheng et al, which is to say that many meandering streaks are combined together into single stabilized streaks by plasma control.
The authors would like to acknowledge the financial support received from the National Science Fund for Distinguished Young Scholars (No. 12102359). The authors are grateful to Professor Dong Li for providing the wind tunnel and corresponding experimental equipment.
[1] |
Spalart P R and McLean J D 2011 Philos. Trans. Roy. Soc. A: Math., Phys. Eng. Sci. 369 1556 doi: 10.1098/rsta.2010.0369
|
[2] |
Corke T C and Thomas F O 2018 AIAA J 56 3835 doi: 10.2514/1.J056949
|
[3] |
Roth J R, Sherman D M and Wilkinson S P 1998 Boundary layer flow control with a one atmosphere uniform glow discharge surface plasma Proc. of the 36th AIAA Aerospace Sciences Meeting and Exhibit (Reno, NV: AIAA) (https://doi.org/10.2514/6.1998-328)
|
[4] |
Roth J R, Sherman D M and Wilkinson S P 2000 AIAA J 38 1166 doi: 10.2514/2.1110
|
[5] |
Sato S et al 2019 Sci. Rep. 9 5813 doi: 10.1038/s41598-019-42284-w
|
[6] |
Benard N, Mizuno A and Moreau E 2009 J. Phys. D: Appl. Phys. 42 235204 doi: 10.1088/0022-3727/42/23/235204
|
[7] |
Zheng B R, Xue M and Ge C 2020 Chin. Phys. B 29 064703 doi: 10.1088/1674-1056/ab8372
|
[8] |
Zheng B R et al 2022 Plasma Sci. Technol. 24 114003 doi: 10.1088/2058-6272/ac72e2
|
[9] |
Jukes T N et al 2004 Turbulent boundary-layer control for drag
reduction using surface plasma Proc. of the 2nd AIAA Flow
Control Conf. (Portland, OH: AIAA) (https://doi.org/10.2514/6.2004-2216)
|
[10] |
Duong A H, Corke T C and Thomas F O 2021 J. Fluid Mech. 915 A113 doi: 10.1017/jfm.2021.167
|
[11] |
Cheng X Q et al 2021 J. Fluid Mech. 918 A24 doi: 10.1017/jfm.2021.311
|
[12] |
Mahfoze O and Laizet S 2017 Int. J. Heat Fluid Flow 66 83 doi: 10.1016/j.ijheatfluidflow.2017.05.013
|
[13] |
Altıntaş A, Davidson L and Peng S H 2020 Phys. Fluids 32 075101 doi: 10.1063/5.0007103
|
[14] |
Hutchins N and Choi K S 2002 Prog. Aeros. Sci. 38 421 doi: 10.1016/S0376-0421(02)00027-1
|
[15] |
Clauser F H 1956 Adv. Appl. Mech. 4 1
|
[16] |
Tennekes H and Lumley J L 1972 A First Course in Turbulence(Cambridge, MA: The MIT Press) ( https://doi.org/10.7551/mitpress/3014.001.0001)
|
[17] |
Bruun H H 1995 Hot Wire Anemometry: Principles and Signal Analysis (Oxford: Oxford University Press)
|
[18] |
Forte M et al 2007 Exp. Fluids 43 917 doi: 10.1007/s00348-007-0362-7
|
[19] |
Jolibois J and Moreau E 2009 IEEE Trans. Dielectr. Electr. Insul. 16 758 doi: 10.1109/TDEI.2009.5128516
|
[20] |
Blackwelder R F and Kaplan R E 1976 J. Fluid Mech. 76 89 doi: 10.1017/S0022112076003145
|
[21] |
Jie Y et al 2017 Phys. Rev. Fluids 2 062601 doi: 10.1103/PhysRevFluids.2.062601
|
[22] |
Xue M et al 2020 AIAA J. 58 2428 doi: 10.2514/1.J057764
|
[1] | Ziqi FANG, Haohua ZONG, Yun WU, Hua LIANG, Zhi SU. Airfoil friction drag reduction based on grid-type and super-dense array plasma actuators[J]. Plasma Science and Technology, 2024, 26(2): 025503. DOI: 10.1088/2058-6272/ad0c99 |
[2] | Borui ZHENG, Yuanzhong JIN, Minghao YU, Yueqiang LI, Bin WU, Quanlong CHEN. Turbulent drag reduction by spanwise slot blowing pulsed plasma actuation[J]. Plasma Science and Technology, 2022, 24(11): 114003. DOI: 10.1088/2058-6272/ac72e2 |
[3] | Hesen YANG, Hua LIANG, Shanguang GUO, Yanhao LUO, Mengxiao TANG, Chuanbiao ZHANG, Yun WU, Yinghong LI. Experimental study on surface arc plasma actuation-based hypersonic boundary layer transition flow control[J]. Plasma Science and Technology, 2022, 24(9): 095503. DOI: 10.1088/2058-6272/ac6d42 |
[4] | Yueqiang LI (李跃强), Chao GAO (高超), Bin WU (武斌), Yushuai WANG (王玉帅), Haibo ZHENG (郑海波), Ming XUE (薛明), Yuling WANG (王玉玲). Turbulent boundary layer control with a spanwise array of DBD plasma actuators[J]. Plasma Science and Technology, 2021, 23(2): 25501-025501. DOI: 10.1088/2058-6272/abce0d |
[5] | Bin WU (武斌), Chao GAO (高超), Feng LIU (刘峰), Ming XUE (薛明), Yushuai WANG (王玉帅), Borui ZHENG (郑博睿). Reduction of turbulent boundary layer drag through dielectric-barrier-discharge plasma actuation based on the Spalding formula[J]. Plasma Science and Technology, 2019, 21(4): 45501-045501. DOI: 10.1088/2058-6272/aaf2e2 |
[6] | Lu MA (马璐), Xiaodong WANG (王晓东), Jian ZHU (祝健), Shun KANG (康顺). Effect of DBD plasma excitation characteristics on turbulent separation over a hump model[J]. Plasma Science and Technology, 2018, 20(10): 105503. DOI: 10.1088/2058-6272/aacdf0 |
[7] | Yadong HUANG (黄亚冬), Benmou ZHOU (周本谋). Active control of noise amplification in the flow over a square leading-edge flat plate utilizing DBD plasma actuator[J]. Plasma Science and Technology, 2018, 20(5): 54021-054021. DOI: 10.1088/2058-6272/aab5bb |
[8] | Junkai YAO (姚军锴), Danjie ZHOU (周丹杰), Haibo HE (何海波), Chengjun HE (何承军), Zhiwei SHI (史志伟), Hai DU (杜海). Experimental investigation of lift enhancement for flying wing aircraft using nanosecond DBD plasma actuators[J]. Plasma Science and Technology, 2017, 19(4): 44002-044002. DOI: 10.1088/2058-6272/aa57f1 |
[9] | R. KHOSHKHOO, A. JAHANGIRIAN. Numerical Simulation of Stall Flow Control Using a DBD Plasma Actuator in Pulse Mode[J]. Plasma Science and Technology, 2016, 18(9): 933-942. DOI: 10.1088/1009-0630/18/9/10 |
[10] | SUN Min (孙敏), YANG Bo (杨波), PENG Tianxiang (彭天祥), LEI Mingkai (雷明凯). Optimum Duty Cycle of Unsteady Plasma Aerodynamic Actuation for NACA0015 Airfoil Stall Separation Control[J]. Plasma Science and Technology, 2016, 18(6): 680-685. DOI: 10.1088/1009-0630/18/6/16 |
1. | Wang, M., Li, P., Han, R. et al. Study on electroaerodynamic characteristics of helium plasma jet under repetitive nanosecond pulsed discharge excitation. Journal of Physics D: Applied Physics, 2025, 58(13): 135209. DOI:10.1088/1361-6463/adb0d3 |
2. | Rezaei, H., Kazemi, M., Saeedi, M. et al. Experimental investigation of the effects of different DBD plasma actuators on the aerodynamic performance of the NACA0012 airfoil. Journal of Physics D: Applied Physics, 2025, 58(11): 115210. DOI:10.1088/1361-6463/ada804 |
3. | Abdullah, M., Galib, M.T., Khan, M.S.A. et al. Recent advancements in flow control using plasma actuators and plasma vortex generators. Heat Transfer, 2024, 53(8): 4244-4267. DOI:10.1002/htj.23131 |
4. | Fang, Z., Zong, H., Zhang, X. et al. Experimental investigation of a spanwise plasma jet array in a turbulent boundary layer for skin-friction drag reduction. Physics of Fluids, 2024, 36(10): 105112. DOI:10.1063/5.0226539 |
U∞ (m s−1) | δ (mm) | δ* (mm) | θ (mm) | uτ (m s−1) | δν (mm) | H | Reτ | Reδ* |
7.5 | 55 | 8.46 | 6.15 | 0.31 | 0.048 | 1.37 | 1140 | 4262 |