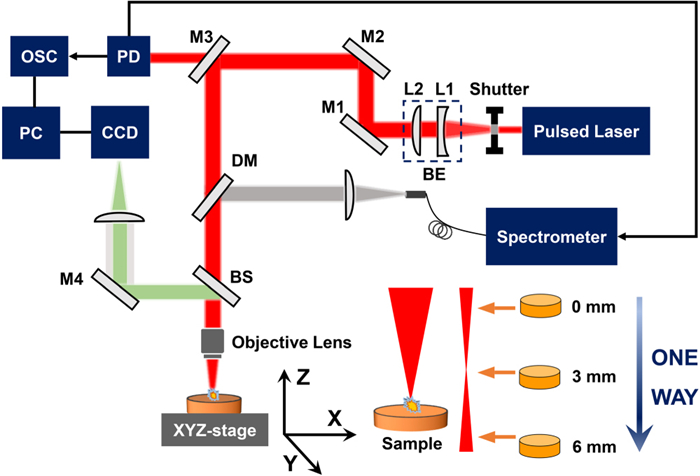
Citation: | Shoujie LI, Ronger ZHENG, Yoshihiro DEGUCHI, Wangquan YE, Ye TIAN, Jinjia GUO, Ying LI, Yuan LU. Spectra-assisted laser focusing in quantitative analysis of laser-induced breakdown spectroscopy for copper alloys[J]. Plasma Science and Technology, 2023, 25(4): 045510. DOI: 10.1088/2058-6272/aca5f4 |
Laser-induced breakdown spectroscopy (LIBS) is a capable technique for elementary analysis, while LIBS quantitation is still under development. In quantitation, precise laser focusing plays an important role because it ensures the distance between the laser and samples. In the present work, we employed spectral intensity as a direct way to assist laser focusing in LIBS quantitation for copper alloys. It is found that both the air emission and the copper line could be used to determine the position of the sample surface by referencing the intensity maximum. Nevertheless, the fine quantitation was only realized at the position where the air emission (e.g. O (I) 777.4 nm) reached intensity maximum, and also in this way, a repeatable quantitation was successfully achieved even after 120 days. The results suggested that the LIBS quantitation was highly dependent on the focusing position of the laser, and spectra-assisted focusing could be a simple way to find the identical condition for different samples' detection. In the future, this method might be applicable in field measurements for LIBS analysis of solids.
Laser-induced breakdown spectroscopy (LIBS) is an analytical technique for elements with great capabilities of in situ detection, real-time measurement, multi-element analysis, no sample preparation, etc [1, 2]. Due to these advantages, LIBS has been extensively applied in different fields with different degrees of success [3–12]. Laser focusing is the first step in LIBS to realize successful detection. Especially for solids analysis, it is vital to maintain the same focusing distance in the measurements, because a minor bias of focusing position would cause a great change in plasma status. This phenomenon has been well investigated by the studies of LTSD (laser-to-sample distance) [13–16], and the plasma performance was highly dependent on the selection of focusing positions. But, the LTSD studies were commonly applied to a single sample for mechanism investigation, and little work was devoted to finding a suitable focusing position to realize the quantitative application for multi-sample. For real applications, a repeatable and simple way for laser focusing would be a great help in the LIBS quantitation of solids. In the present work, we tried to use the LIBS intensity as a direct indicator to find an optimized position of laser focusing in the quantitation of copper alloys, and the method might be a practical way for solids analysis of LIBS.
There are different ways used for laser focusing in LIBS, and imaging is one common way [17, 18]. With imaging, the focal position of the laser could be easily determined by referencing the surface image of the sample, but the chromatic aberration between the illuminance and the laser might cause a position disparity in focusing. Using a laser pointer is another way to implement the focus positioning in LIBS [19, 20]. In this way, the light of the laser pointer is obliquely focused onto the focal spot of the pulsed laser, and the pointer light would move away once the sample surface is of the focal plane. The acoustic signal is also utilized to assist the laser focusing in LIBS [21, 22], and signal amplitude is usually used to track the sampling position because the acoustic signal is generated from the shock wave in the process of laser ablation. Recently, the plasma image was applied as a new proof to find the optimized focal position since the plasma morphology directly revealed the state of laser ablation [23]. In this work, we tried to use LIBS intensities to determine the position of laser focusing for quantitative analysis. This method is simple without the need for an extra device for positioning, and the intensity maximum around the focal point was employed as the reference to ensure consistent detection on different samples. It has been proved that this positioning way was free of calibration for LIBS mapping on a single target [24–26], while the quantitative application was not reported so far. So, in this work, we applied the positioning way for the LIBS quantitation of copper alloys. But it is found that better results were obtained by using the elemental emission, not the plasma intensity. Moreover, the quantitation repeatability could be well preserved in this positioning manner.
The experimental setup is shown in figure 1. A pulsed laser (ZY Laser, Penny 100) was employed to deliver 1064 nm pulses of 10 ns duration with a repetition rate of 1 Hz. The laser beam was expanded to 6 mm diameter by the combination of a concave lens L1 (f=−50.8 mm) and a convex lens L2 (f=100 mm). Using a 10x objective lens (Daheng, GCO-2122, Numerical Aperture 0.25, Working Distance 27 mm), the pulsed laser was tightly focused onto the sample surface to generate plasma under pulse energy of 12 mJ to avoid air breakdown. The energy fluctuation of the laser was less than 10%. In general, it is not necessary to use an objective lens in LIBS detection. But the objective lens utilization would allow a low-energy laser to support field measurement at a low cost. The plasma emission was reflected by a dichroic mirror (OptoSigma, TFMS-25.4, Reflection: 245–800 nm, Transmission: 850–1100 nm), and focused into an optical fiber (600 μm diameter) via a coupler to implement the spectral detection with a spectrometer (Avantes, AVASpec-ULS2048). Besides, a CCD camera was used to observe the sample surface via a tube lens by coupling the reflection from a beam splitter (Transmission/Reflection=9/1). In the measurement, the alloy sample was driven by a 3-axis translation stage (ZTGZ, ZT102H30) to realize the laser focusing in vertical and the sample movements in horizontal respectively. In the measurements, the spectrometer was triggered by a photodiode to take LIBS spectra with a spectral resolution of 0.4 nm. The detection was implemented under the integration time of 1.05 ms and a detection delay of 1.28 μs, as for including the whole duration of element emissions. The LIBS quantitation was carried out by 5 certified samples of metal alloys (GB 9097.1, Nanjing Mingshan Materials Inc.) with concentration ratios (Cu/Al) of 10/90, 40/60, 80/20, 95/5, and 99/1. It is noticed that we intended to select a large concentration range to simulate the actual situation of minerals, such as low-grade ores or high-grade ores. Before each measurement, the alloy sample was well polished and cleaned with distilled water. In the laser focusing, every sample was moved from a fixed position (0 mm) near the objective lens, and lowered down to an end position with a maximum distance of 6 mm. Since errors would be generated in the forward-backward moving, the 'one-way movement' was strictly conducted in the process of laser focusing with emphasis on no moving return. In the movement cycle, the alloy sample went through the focal point of the laser from a high position (sampling distance: 0 mm) to a low position (sampling distance: 6 mm).
It is shown in [24] that the spectral radiation of plasma could be used to determine the best focal position. The intensity of plasma radiation presented a Lorentzian profile under a single lens (f=20 mm) when the sampling distance was changing, and the position of the strongest radiation was regarded as the optimal sampling distance in LIBS. Following this protocol, we carried out the LIBS detection for a copper sample (99.999%), and the results are compared in figure 2(a) with different moving steps of 100 μm, 200 μm, and 500 μm. The plasma intensity is the total intensity of spectral emissions in the wavelength range of LIBS detection. It is interesting to find that the plasma intensity was not showing a regular pattern, especially under the higher spatial-resolution (moving step ~100 μm). More importantly, there are intensity dips presented at the sampling distance of 2.6 and 3.2 mm. These 2 positions are exactly in the range near the focal plane of laser ablation when referencing figure 2(b). It is seen that a symmetric variation was shown in the crater size, and the minimum crater was found at the sampling distance of around 3 mm. The result confirmed that laser focusing was normally performed. So, the irregular profile of intensity (figure 2(a)) was ought to be caused by the plasma itself. Because we used a 10x objective lens instead of the single lens to generate the plasma, and the focal depth was determined as 8 μm according to the formula [27, 28]:
dp=nλNA2 | (1) |
where, the 'n' is the refractive index, the 'λ' is the laser wavelength, and the 'NA' is the numerical aperture. It is evident that the objective lens offers a short focal depth at the micrometer level, and the generated plasma was supposed to be more sensitive to the LTSD under objective-lens focusing.
To better understand the irregular profile of plasma intensity, the variation of spectral emission was examined by specifying the contribution of each element. Figure 3 is the typical result of LIBS detection for copper alloys (Cu/Al=99/1). The recognized lines could be generally classified as 'sample elements' and 'air elements'. Copper and aluminum are the main elements in the alloy samples, and corresponding emissions could be found as Cu (I) 324.7, 327.4, 510.5, 515.3, 521.9 nm, Al (I) 308.3, 309.3, 394.4, 396.1 nm. For the air elements, the emissions of nitrogen, hydrogen, and oxygen were obtained as H (I) 656.3 nm, N (I) 746.8 nm, and O (I) 777.4 nm. In figure 3(b), the copper emissions seem to present a dramatic variation of intensity in the distance change, while the oxygen signal showed little variations. The result suggested that the alloy's emission was more sensitive to the focusing position when compared with the air emissions. More importantly, the air emissions cannot be directly obtained under the excitation of this work (pulse energy=12 mJ), and these emissions probably resulted from the laser ablation of alloys. So, the air is supposed to play a role in the LIBS detection of copper, and it might be an influence in the laser focusing.
Figure 4 is the emissions changing as a function of the sampling distance. It is seen that the sample signal (Cu and Al) was presented at the sampling distance from 1.5 to 5 mm, while the oxygen signal was obtained at the sampling distance of 2–4 mm. Evidently, the air was excited after the plasma generation on copper alloys, and the oxygen emission was probably formed in the process of sample ablation. Moreover, the oxygen emission presented a Gaussian profile with a high correlation (R2=0.995), but the Cu, Al intensity, and plasma intensity demonstrated irregular profiles. The intensity maximum of oxygen was only shown at the sampling distance of 3.2 mm. For copper and aluminum, 2.9 mm was the position where the highest intensity was reached. When referencing the craters in figure 2(b), the distance of 2.9–3.2 mm should be in the sample surface region. So, the emission was reasonable to be differently performed on different elements, because the laser ablation was conducted on the 'gas-solid' interface. Mao et al pointed out that the 'plasma shield' would be prominent at the solid surface when the power density was above 0.3 GW cm−2, and a portion of the laser light was reflected or scattered from the dense plasma before it reached the solid sample [29]. So, the plasma shield was supposed to take place in our case, and it might be the reason that the intensity maximum was presented differently on elements. As shown in figure 4, the copper emission actually reached the intensity maximum earlier than the oxygen emission did (distance: 2.9 mm versus 3.2 mm). At the position of 3.2 mm, the O (I) 777.4 nm emission demonstrated an intensity maximum, and it is implied that the air plasma probably formed a 'plasma shield'. That shield effect would reduce the energy deposition on the alloy sample. As a consequence, the copper and aluminum emissions showed decreased intensities at 3.2 mm (figures 4(b) and (c)), so that the total intensity of plasma presented an evident decline at 3.2 mm as well (figure 4(a)).
However, this phenomenon might be useful for LIBS, because the intensity maximum can be applied to indicate the positions in laser focusing. In figure 4, when the laser focus was approaching the sample surface, there are 2 positions of intensity maximum: 2.9 mm for Cu (I) 324.7 nm and 3.2 nm for O (I) 777.4 nm. So, the position information could be possibly retrieved by observing the intensity maximum of copper or oxygen. Figure 5 is the positioning results by referencing these intensity maximums, and the measured height was the subtracted value between every 2 stages' height determined by the method. It can be seen that the positioning performance was similar by using Cu (I) 324.7 nm and O (I) 777.4 nm. A higher precision could be achieved at the height of 80 and 230 μm, while the positioning performance was worsened at large heights (690 μm, 1180 μm). This positioning way might be more effective in a short range near the focal point, because the long-range displacement was a challenge for the stage positioning and the plasma stabilization.
With this positioning way, we tried to implement a quantitative analysis of copper alloys as results are shown in figure 6. It is seen that the calibration curve was well established with high linearity at the sampling distance of 3.2 mm, which is the position where O (I) 777.4 nm reached intensity maximum in the laser focusing. But, at the sampling distance of 2.9 mm, a typical self-absorption was observed on the calibration curve, and this is the position for the intensity maximum of Cu (I) 324.7 nm. Besides that, a lower standard deviation was also obtained when the sampling distance was shifted from 2.9 to 3.2 mm. So, the finer quantitation was preferably established by using the positioning of O (I) 777.4 nm than that by using the positioning of Cu (I) 324.7 nm. It is already known from figure 4 that, on the sampling distance of 3.2 mm, the plasma shield was probably intensified by oxygen emission. So, the laser energy was less deposited on the alloys to weaken the self-absorption effect, and the curve fitting was significantly linearized in spite of low intensities. More importantly, this positioning way is capable to maintain detection repeatability, and the results are shown in figures 6(c) and (d). The quantitation was carried out again after a long period (120 d), and the rebuilt calibration curve was finely in accord with the result 4 months ago.
In this work, we tried to utilize the spectral intensity to assist the laser focusing in LIBS, and no extra operation was needed except by observing the specified line (oxygen or copper) in the consecutive detections around the sample surface. It is a simple and direct way to ensure the focusing precision at the micrometer level on different samples. In conventional ways, the LIBS detection was carried out after the focusing position was determined. In our method, a series of LIBS measurements were implemented around the sample surface without concern for the focusing position. After measurement termination, the position of laser focusing was retrieved by finding the highest intensity where it was obtained. The results indicated that the positioning could be realized by referencing the emission of Cu (I) 324.7 nm or O (I) 777.4 nm, but the fine quantitation was only achieved at the position where O (I) 777.4 nm reached intensity maximum. The same results could also be obtained under other air emissions (e.g. nitrogen, hydrogen). Furthermore, this quantitation was successfully repeated after a long period of 120 d via positioning with O (I) 777.4 nm intensity. It is noticed that we carried out the LIBS detection by using a 10x objective lens under low energy (12 mJ). The findings might be helpful for field or on-site measurements since low energy was required for the laser and no extra device was needed for the positioning. Moreover, this positioning method is free of calibration even if the operating condition was changed. But this method is only applicable for the sample with a hard surface because multi-shot would be accumulated on the same detection point. Nevertheless, it is hoped that our method could be a solution for those LIBS systems without positioning devices.
This study was financially supported by the Provincial Key Research and Development Program of Shandong, China (No. 2019GHZ010), the Natural Science Foundation of Shandong Province (No. ZR2020MF123), National Natural Science Foundation of China (Nos. 61975190 and 12174359), and the Fundamental Research Funds for the Central Universities (No. 202161002).
[1] |
Xue B Y et al 2020 J. Anal. At. Spectrom. 35 2880 doi: 10.1039/D0JA00139B
|
[2] |
Xu W P et al 2019 J. Anal. At. Spectrom. 34 1018 doi: 10.1039/C8JA00359A
|
[3] |
Wiens R C et al 2013 Spectrochim. Acta B 82 1 doi: 10.1016/j.sab.2013.02.003
|
[4] |
Sobron P, Wang A L and Sobron F 2012 Spectrochim. Acta B 68 1 doi: 10.1016/j.sab.2012.01.002
|
[5] |
Li N et al 2021 J. Anal. At. Spectrom. 36 2660 doi: 10.1039/D1JA00266J
|
[6] |
Thornton B et al 2015 Deep-Sea. Res. Pt. I 95 20 doi: 10.1016/j.dsr.2014.10.006
|
[7] |
Yoshino S et al 2018 Spectrochim. Acta B 145 1 doi: 10.1016/j.sab.2018.03.015
|
[8] |
Xu W J et al 2020 J. Anal. At. Spectrom. 35 1641 doi: 10.1039/D0JA00157K
|
[9] |
Cui M C et al 2019 Plasma Sci. Technol. 21 034007 doi: 10.1088/2058-6272/aaeba7
|
[10] |
Dong F Z et al 2012 Front. Phys. 7 679 doi: 10.1007/s11467-012-0263-y
|
[11] |
Wang Y et al 2016 Plasma Sci. Technol. 18 1192 doi: 10.1088/1009-0630/18/12/09
|
[12] |
Singh V K et al 2018 Biophys. Rev. 10 1221 doi: 10.1007/s12551-018-0465-9
|
[13] |
Zhang D et al 2019 Plasma Sci. Technol. 21 034009 doi: 10.1088/2058-6272/aaec9b
|
[14] |
Jiang Z H et al 2018 Plasma Sci. Technol. 20 085503 doi: 10.1088/2058-6272/aabc5e
|
[15] |
Guo J et al 2017 J. Anal. At. Spectrom. 32 367 doi: 10.1039/C6JA00396F
|
[16] |
Wang Q Y et al 2022 Opt. Laser Technol. 122 105862 doi: 10.1016/j.optlastec.2019.105862
|
[17] |
Jolivet L et al 2019 Spectrochim. Acta B 151 41 doi: 10.1016/j.sab.2018.11.008
|
[18] |
Li C et al 2021 Biomed. Opt. Express 12 5214 doi: 10.1364/BOE.427099
|
[19] |
Wei W et al 2019 Plasma Sci. Technol. 21 034004 doi: 10.1088/2058-6272/aae383
|
[20] |
Motto-Ros V et al 2014 Spectrochim. Acta B 92 60 doi: 10.1016/j.sab.2013.12.008
|
[21] |
Alvarez-Llamas C et al 2022 Anal. Chem. 94 1840 doi: 10.1021/acs.analchem.1c04792
|
[22] |
Chide B et al 2019 Spectrochim. Acta B 153 50 doi: 10.1016/j.sab.2019.01.008
|
[23] |
Li Q Y et al 2020 J. Anal. At. Spectrom. 35 366 doi: 10.1039/C9JA00367C
|
[24] |
Beresko C, Kohns P and Ankerhold G 2014 Spectrochim. Acta B 99 20 doi: 10.1016/j.sab.2014.06.004
|
[25] |
He C J et al 2022 Spectrochim. Acta B 188 106340 doi: 10.1016/j.sab.2021.106340
|
[26] |
Cortez J et al 2017 Appl. Spectrosc. 71 634 doi: 10.1177/0003702816687571
|
[27] |
Levoy M et al 2006 ACM Trans. Graph. 25 924 doi: 10.1145/1141911.1141976
|
[28] |
Lim Y T et al 2012 Opt. Express 20 23480 doi: 10.1364/OE.20.023480
|
[29] |
Mao X L and Russo R E 1996 Appl. Phys. A 64 1 doi: 10.1007/s003390050437
|
[1] | Yaguang MEI (梅亚光), Shusen CHENG (程树森), Zhongqi HAO (郝中骐), Lianbo GUO (郭连波), Xiangyou LI (李祥友), Xiaoyan ZENG (曾晓雁), Junliang GE (葛军亮). Quantitative analysis of steel and iron by laser-induced breakdown spectroscopy using GA-KELM[J]. Plasma Science and Technology, 2019, 21(3): 34020-034020. DOI: 10.1088/2058-6272/aaf6f3 |
[2] | Jiamin LIU (刘佳敏), Ding WU (吴鼎), Cailong FU (付彩龙), Ran HAI (海然), Xiao YU (于潇), Liying SUN (孙立影), Hongbin DING (丁洪斌). Improvement of quantitative analysis of molybdenum element using PLS-based approaches for laser-induced breakdown spectroscopy in various pressure environments[J]. Plasma Science and Technology, 2019, 21(3): 34017-034017. DOI: 10.1088/2058-6272/aaf821 |
[3] | Congyuan PAN (潘从元), Jiao HE (何娇), Guangqian WANG (王广谦), Xuewei DU (杜学维), Yongbin LIU (刘永斌), Yahui SU (苏亚辉). An efficient procedure in quantitative analysis using laser-induced breakdown spectroscopy[J]. Plasma Science and Technology, 2019, 21(3): 34012-034012. DOI: 10.1088/2058-6272/aaf50f |
[4] | Qingdong ZENG (曾庆栋), Fan DENG (邓凡), Zhiheng ZHU (朱志恒), Yun TANG (唐云), Boyun WANG (王波云), Yongjun XIAO (肖永军), Liangbin XIONG (熊良斌), Huaqing YU (余华清), Lianbo GUO (郭连波), Xiangyou LI (李祥友). Portable fiber-optic laser-induced breakdown spectroscopy system for the quantitative analysis of minor elements in steel[J]. Plasma Science and Technology, 2019, 21(3): 34006-034006. DOI: 10.1088/2058-6272/aadede |
[5] | Xiaoyong HE (何小勇), Runhua LI (李润华), Fujuan WANG (王福娟). Elemental analysis of copper alloy by high repetition rate LA-SIBS using compact fiber spectrometer[J]. Plasma Science and Technology, 2019, 21(3): 34005-034005. DOI: 10.1088/2058-6272/aae1f1 |
[6] | Dan LUO (罗丹), Ying LIU (刘英), Xiangyu LI (李香宇), Zhenyang ZHAO (赵珍阳), Shigong WANG (王世功), Yong ZHANG (张勇). Quantitative analysis of C, Si, Mn, Ni, Cr and Cu in low-alloy steel under ambient conditions via laser-induced breakdown spectroscopy[J]. Plasma Science and Technology, 2018, 20(7): 75504-075504. DOI: 10.1088/2058-6272/aabc5d |
[7] | Yuqing XIONG (熊玉卿), Hengjiao GAO (高恒蛟), Ni REN (任妮), Zhongwei LIU(刘忠伟). Atomic layer deposition of copper thin film and feasibility of deposition on inner walls of waveguides[J]. Plasma Science and Technology, 2018, 20(3): 35507-035507. DOI: 10.1088/2058-6272/aa9cdf |
[8] | Shuxia ZHAO (赵书霞), Lei ZHANG (张雷), Jiajia HOU (侯佳佳), Yang ZHAO (赵洋), Wangbao YIN (尹王保), Weiguang MA (马维光), Lei DONG (董磊), Liantuan XIAO (肖连团), Suotang JIA (贾锁堂). Accurate quantitative CF-LIBS analysis of both major and minor elements in alloys via iterative correction of plasma temperature and spectral intensity[J]. Plasma Science and Technology, 2018, 20(3): 35502-035502. DOI: 10.1088/2058-6272/aa97ce |
[9] | ZHU Dehua (朱德华), CAO Yu (曹宇), ZHONG Rong (钟蓉), CHEN Xiaojing (陈孝敬). Quantitative Analysis of Composition Change in AZ31 Magnesium Alloy Using CF-LIBS After Laser Material Processing[J]. Plasma Science and Technology, 2015, 17(11): 909-913. DOI: 10.1088/1009-0630/17/11/03 |
[10] | MAO Yangwu(毛样武), GUO Beibei(郭贝贝), NIE Dunwei(聂敦伟), Domenico MOMBELLO. Tarnish Testing of Copper-Based Alloys Coated with SiO 2 -Like Films by PECVD[J]. Plasma Science and Technology, 2014, 16(5): 486-490. DOI: 10.1088/1009-0630/16/5/08 |
1. | Ren, L., Wang, F., Zhang, Y. et al. Rapid identification of Radix Astragali by data fusion of laser-induced breakdown spectroscopy and Raman spectroscopy coupled with deep learning. Talanta, 2025. DOI:10.1016/j.talanta.2024.127016 |
2. | Zhu, H., Fan, B., Zhang, Y. et al. Influence of the distance between the focused point and Al surface on atomic and molecular emission spectra in air. Journal of Analytical Atomic Spectrometry, 2024. DOI:10.1039/d4ja00209a |
3. | Clough, R., Fisher, A., Gibson, B. et al. Atomic spectrometry update: review of advances in the analysis of metals, chemicals and materials. Journal of Analytical Atomic Spectrometry, 2023, 38(11): 2215-2279. DOI:10.1039/d3ja90038j |
4. | Xue, Q., Tian, B., Yin, T. et al. Investigation of deformation comprised microstructure and precipitation of Cu–Sn–Ti alloy during hot deformation. Journal of Materials Research and Technology, 2023. DOI:10.1016/j.jmrt.2023.08.282 |